AIM APPLICATIONS ADVICE
Optimized & Engineer Approved
Solder Paste Print Setting Recommendations
Print settings are crucial for optimal solder paste application. This guide provides insights into key parameters like snap-off, separation distance, separation, speed, print speed, and squeegee pressure. Understanding and adjusting these settings can improve the quality and reliability of solder paste deposition.
Recommended Snap-Off Settings: 0.00 (on-contact)
What is Snap-Off?
Snap-off refers to the gap between the substrate (printed circuit board) and the screen or stencil. Adjusting the snap-off distance helps release solder paste from the stencil and control the amount of paste deposited on the substrate.
The Role of Snap-Off in Solder Application
During printing, the squeegee blade applies pressure to the stencil and seals the area being printed. As the blade passes, the stencil returns to the preset snap-off distance, separating from the solder paste left on the substrate.
Snap-off is primarily a carryover from the days of printing through screens, though it may improve paste release through a poorly cut stencil and may still be necessary for specific equipment or applications.
Snap-Off Printing Considerations
Positive snap-off distances can negatively impact the desired “gasketing” effect, causing paste spread and bridges between component pads. Snap-off can also lead to uneven paste deposition and inconsistent printing results.
Setting the snap-off distance to 0.00 (on-contact printing) provides benefits like full gasketing, preventing bleed out and bridging, even for fine-pitch components. On-contact printing also results in more uniform paste deposition and consistent paste height.
How to Adjust Snap-Off Settings
To establish 0.00 snap-off (on-contact) printing, follow these steps:
- Select a flat substrate.
- Position the substrate under the stencil.
- Lower the stencil or raise the board to the print height.
- Turn off any vacuum holding the board.
- Adjust the stencil snap-off to create a definite gap between the stencil and substrate surface.
- Slowly lower the snap-off distance by deflecting the stencil towards the substrate until it just makes contact across the printable area.
- For manual printers, lock the stencil height and reset dial indicators to 0.00. For automated printers, record the new snap-off distance and repeat steps 2, 3, and 6 to verify the adjustment.
Notes
Some computer-controlled equipment requires additional calibration for snap-off settings. Always verify your adjustments. Also, remember to check the entire board area for contact with the stencil, particularly the outer edges. Examine the board support and ensure the board is not warped if contact occurs prematurely.
Recommended Separation Distance: 0.010″ to 0.050″ (0.25 to 1.25 mm) depending on board thickness, snap-off, and downstop settings.
What is Separation Distance?
Separation distance refers to the distance the Z-tower, or board support, lowers at a controlled speed to clear the stencil before returning to its home position. It is important to separate the stencil carefully from the PCB after printing to ensure clean separation of solder paste from the stencil apertures. The separation distance is usually traversed at a selected speed to aid in this process.
The role of separation distance in solder application
Once the print cycle is complete, the Z-tower holding the printed substrate lowers at a specified speed to the set separation distance. After reaching this distance, the Z-tower lowers at full speed to its home position. Vibrations in some board supports, caused by slow motor rotation, also assist in releasing the solder paste.
Separation Distance Considerations
Setting a separation distance promotes better release of solder paste from stencil apertures. It also contributes to more uniform solder paste deposits and minimizes peaking. Though using a separation distance slows down the overall print cycle time, the impact on production time is minimal for small separation distances or faster separation speeds but becomes more significant as limits are approached.
How to Adjust Separation Distance
Start by setting the separation distance in the setup menu to 0.005” (0.125 mm) more than the stencil thickness. For example, if the stencil thickness is 0.006″ (0.15 mm), set the starting separation distance to 0.011″ (0.28 mm). Then execute the following steps:
- Lower the stencil or raise the board to the print height.
- Ensure that the vacuum holding the board is turned off.
- Adjust the separation distance gradually, ensuring proper clearance between the stencil and substrate.
- Verify the separation distance by printing and inspecting the solder paste deposition.
Notes: Fine-tuning the separation distance may be necessary based on specific equipment or requirements. Test and validate the adjusted separation distance to ensure optimal results.
Consider the impact on overall production time when adjusting the separation distance. Find a balance between optimal paste release and efficient printing.
It is essential to monitor and maintain the separation distance to avoid issues such as solder paste smearing or inadequate release. Regularly inspect and clean the stencil and equipment to ensure proper functioning.
Recommended Separation Speed: 0.010″ to 0.020″ per second (0.254 mm to 0.508 mm per second), 1-2, or 10-20% of the axis speed for fine pitch and micro-BGA components. For noncritical printing, a speed of 0.030″ to 0.050″ per second (0.762 mm to 1.27 mm per second), 3-5, or 30-50% can be used.
What is Separation Speed?
Separation speed refers to the measured velocity at which the squeegee separates from the stencil. As with separation distance, this parameter is designed to aid the separation of solder paste from the stencil apertures. Separation speed can be indicated in thousands of an inch, millimeters, or as a percentage of axis speed.
The Role of Separation Speed in Solder Application
Once the print cycle is complete, controlling the separation speed of the squeegee helps in achieving a clean separation of solder paste from the stencil apertures. A well-controlled separation speed contributes to consistent and uniform paste deposits, minimizing defects and ensuring better solder joint quality. By carefully adjusting the separation speed, you can optimize the printing process for improved results.
Separation Speed Considerations
Setting an appropriate separation speed is crucial for achieving optimal solder paste application. It helps in avoiding issues like dog-ears, peaking, wicking, and inadequate paste coverage. While slower separation speeds are generally preferred for better control, it is important to strike a balance between reliable paste deposition and efficient printing. Consider factors such as component types, board designs, and solder paste characteristics when determining the suitable separation speed for your application.
How to Adjust Separation Speed
To adjust the separation speed effectively, follow these steps:
- Access the setup menu or software settings.
- Locate the separation speed parameter.
- Start by setting a conservative value based on the recommended range for your specific application.
- Execute a test print and inspect the solder paste deposition for quality and consistency.
- Fine-tune the separation speed gradually, taking into account the performance and results obtained.
- Repeat the test printing and inspection process until the desired solder paste application is achieved.
Notes: Fine-tuning the separation speed may be necessary based on specific equipment or requirements. Test and validate the adjusted separation speed to ensure optimal results.
It is essential to monitor and maintain the separation speed to avoid issues such as solder paste smearing or inadequate release. Regularly inspect and clean the stencil and equipment to ensure proper functioning.
When printing fine pitch, i.e. LGA, QFN, and micro-BGA, set separation speed to a minimum.
Recommended Print Speed Settings: Depending on the formulation and viscosity of the solder paste, maximum recommended print speeds range from 1 to 8 inches per second (25 to 200 mm per second).
What is Print Speed?
Print speed refers to the speed at which the squeegee assembly moves across the stencil during the print cycle.
The Role of Print Speed in Solder Application
Print speed should be set in conjunction with other parameters like squeegee pressure, paste chemistry, stencil aperture size, and more. Adjusting the print speed is necessary to achieve a clean wipe of the stencil surface, especially when using high-viscosity solder paste at higher speeds.
Print Speed Considerations
High-speed printing typically refers to speeds between 4 to 8 inches per second (100 to 200 mm per second). Achieving good print quality at high speeds depends on selecting the right solder paste viscosity and rheology, as well as appropriate stencil design.
During high-speed printing, shear forces from the squeegee cause temporary viscosity reduction (shear thinning) in solder pastes. Higher speeds and increased squeegee pressure exacerbate shear thinning, potentially leading to pad-to-pad shorting if the paste does not quickly return to its normal viscosity. Inadequate stencil aperture filling and insufficient pad coverage can also occur at high speeds.
High-speed printing requires additional pressure and speed settings, which can impact transducers, servo motors, squeegee blades, and stencil life. The primary benefit of high-speed printing is reduced production time and increased throughput.
How to Adjust Print Speed
Due to the number of variables involved, it is recommended to consult your AIM Solder technician for advice on print speed adjustment.
Notes: In general, slower printing results in better print quality, but this should be balanced with production needs. Adjust the print speed to optimize cycle time without slowing down the rest of your production line.
Consider adjusting print settings to an on-demand cycle rate to minimize waiting time between cycles. This optimization facilitates stable solder paste rheology and improved print cycle time.
If high print speeds are necessary for your production process, ensure that your solder paste is designed to withstand these speeds. Providing adequate board support can also minimize bending during the print cycle.
Recommended Squeegee Pressure: 1 to 1.5 lbs per linear inch (0.45 to 0.70 kg per 25 mm) of squeegee blade
What is Squeegee Pressure?
Squeegee pressure refers to the downward pressure exerted by the squeegee blade onto the stencil surface during the print cycle.
The Role of Squeegee Pressure in Solder Application
During the print cycle, the squeegee pushes the solder paste across the printable area, filling the apertures and wiping the stencil surface clean. Proper squeegee pressure, evenly distributed along the blade’s length, ensures consistent paste height, uniform deposition control, and reduced wear on the blade and stencil.
Squeegee Pressure Considerations
Applying the right amount of pressure is essential to ensure consistent and reliable solder paste deposits while avoiding potential issues. Excessive pressure can lead to damaged stencils, coining, and breaking of webbing between fine pitch apertures. These issues can negatively impact the printing process and result in poor solder joint quality. Conversely, using too little pressure may result in skips if the stencil is not adequately wiped clean. It is important to find the balance between applying sufficient pressure for stencil filling and avoiding excessive force that can cause damage.
How to Adjust Squeegee Pressure
To establish proper squeegee pressure, assuming the blades are correctly installed and adjusted, follow these steps:
- Select a flat substrate.
- Position the substrate under the stencil.
- Adjust the squeegee pressure so that excess solder remains on the aperture area of the stencil surface after a print cycle.
- Apply solder paste to the stencil and perform a print cycle.
- Observe the amount of solder paste remaining on the stencil surface.
- Slightly increase the squeegee pressure and perform another print cycle.
- Again, observe the amount of solder paste remaining on the stencil surface, which should be slightly less than the previous pass.
- Repeat steps 6 and 7 until only a very thin skim coat of solder paste remains visible on the aperture area of the stencil surface.
Notes: Adjusting other print parameters, such as print speed or stencil design, can also influence the required squeegee pressure.
Regular inspection and maintenance of squeegee blades ensure optimal performance and consistent pressure application.
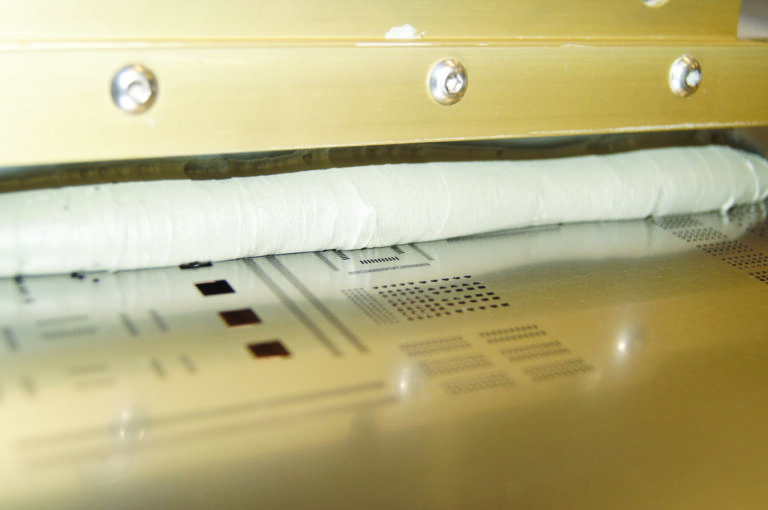