AIM APPLICATIONS ADVICE
Optimized & Engineer Approved
Solder Paste Handling Tips
Proper handling is crucial for maintaining solder paste quality and achieving optimal results in electronic manufacturing processes. Here are some important tips to follow for transporting, storing, and preparing solder paste, as well as recommendations for stencil application and environmental conditions.
TRANSPORT & SHIPPING TIP #1
Ship solder paste overnight whenever possible to minimize exposure to environmental conditions, especially during hot and humid weather.
TRANSPORT & SHIPPING TIP #2
For international shipments, aim for a transit time of two or three days maximum, as overnight shipping may not be available. Avoid shipping solder paste by sea.
TRANSPORT & SHIPPING TIP #3
Consider using special packaging materials or including ice for shipments during very hot weather, international shipping, or for extremely sensitive paste compositions.
TRANSPORT & SHIPPING TIP #4
Note that solder paste transport and solder paste storage are distinct. Brief excursions unrefrigerated will generally not damage the paste. Most formulations are sufficiently robust to survive brief trips outside of storage during transportation.
STORAGE TIP #1
Transfer solder paste to a proper storage area immediately upon receipt and avoid leaving it on the dock.
STORAGE TIP #2
Store solder paste at room temperature (< 25°C or < 77°F) for a typical shelf life of three to six months. Refrigerated storage at temperatures of 0°C – 12°C (32°F – 55°F) can double the shelf life while protecting it from environmental fluctuations.
STORAGE TIP #3
Do not mix new and used solder paste in the same container, as it will degrade the new paste.
PREPERATION TIP #1
Allow solder paste to reach ambient (room) temperature naturally before breaking the seal. Avoid forcing warming of the paste. Overnight (8 hours) exposure to room temperature is recommended for optimal results.
PREPERATION TIP #2
Lightly and thoroughly stir the paste for one minute before application, using a spatula. Stirring ensures even distribution of any separated material resulting from storage. Cartridges do not require mixing as shear thinning occurs as paste is dispensed from the cartridge.
PREPERATION TIP #3
Never use an automated mixer for stirring as this can damage the rheological properties of the paste.
Stencil Application Tip #1
Apply a sufficient amount of solder paste for a smooth and even roll during the print cycle. A roll diameter of ⅜” to ½” (9.5 to 12.5 mm) is typically suitable for most stencils. Initially, apply two or three times the desired roll size to allow the squeegee blade to distribute the paste evenly.
Stencil Application Tip #2
The length of the roll should match the length of the squeegee blade. The squeegee should be slightly larger (1/2″ or 12.5 mm on each side) than the printable area.
Stencil Application Tip #3
Add small amounts of fresh solder paste to the stencil at controlled intervals to maintain its chemistry and workable properties. It’s better to add smaller amounts frequently than larger amounts less often.
Stencil Application Tip #4
Proceed with the SMT process promptly after printing to prevent the solder paste from drying out on the PCB.
Stencil Application Tip #5
A compatible under stencil cleaner can extend stencil print life. However, avoid using isopropyl alcohol (IPA) as it can degrade the solder paste.
Application Environment Tip #1
Maintain a stable temperature and humidity during printing, populating, and reflow processes for optimal results. A temperature of 22° – 26°C (72° – 80°F) at 45% ± 5% relative humidity is ideal, allowing for open/tack times of up to 24 hours.
Application Environment Tip #2
In environments with excessive temperature or humidity, solder paste functionality may decrease more quickly, leading to potential defects like slumping, solder balling, and viscosity changes.
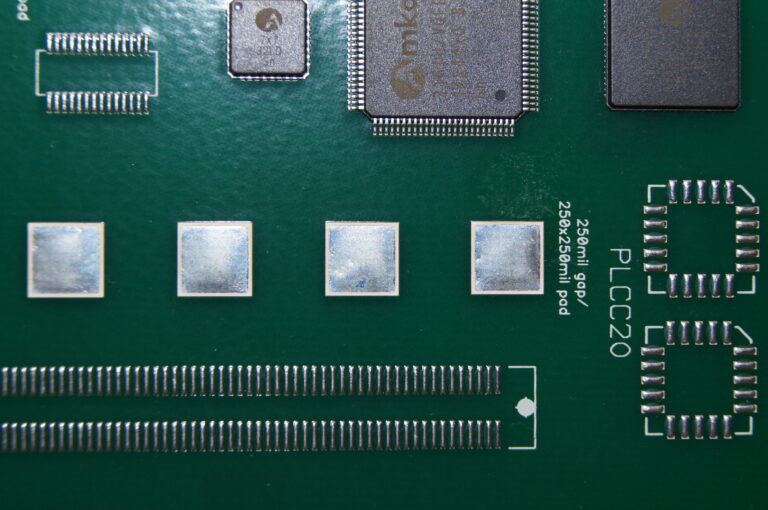
Solder Paste Handling FAQs
Most frequently asked questions and answers
A: Freezing solder paste is generally not recommended as it can cause activators to precipitate out of the paste, which can adversely affect wetting and print performance. However, most solder paste formulations will maintain their integrity down to 0°C (32°F) and survive freezing near this temperature without issue. What is not advisable is going much below this temperature.
A: Forcefully warming the paste by exposing it to heat or stirring vigorously can alter its rheological properties and negatively impact its performance.
A: The shelf life of solder paste varies depending on the specific type but AIM solder pastes typically have a shelf life of 3-6 months when stored at room temperature.
A: Using an automatic mixer can introduce varied and unpredictable forces that may cause changes in the solder paste’s viscosity and other properties, thereby adversely affecting its functionality. We recommend hand stirring only.
A: It is not advisable to combine new and used solder paste in the same container as it can contaminate and degrade the unused paste.
A: Paste should not be refrigerated after opening. Instead, reseal any open material and store it at room temperature when not in use.
A: Syringes and cartridges should ideally be stored vertically with the application tips pointing down to prevent flux separation and maintain consistent performance.
A: While we cannot guarantee the quality or usability of paste after its expiration date, if you choose to use it beyond this date, make sure to test it first to determine if it still meets your requirements. Keep in mind it might cost more in problems to use expired paste than you would save, and that it’s often safer and more economically efficient to discard it and use fresh paste.
A: One common sign of mishandling is the separation of the flux and alloy within the paste. Other, more subtle signs may only manifest as manufacturing defects.
A: No. Different types or brands of solder paste have different compositions and properties, which can lead to unpredictable results and potential performance issues.
A: It is generally not recommended to reuse leftover solder paste. The paste may have been exposed to contaminants or have undergone changes in its composition, which can affect its performance and reliability. It’s best to use fresh solder paste for optimal results.
A: You should throw it away. Attempting to adjust the viscosity with additives is unlikely to yield proper soldering results.
A: Disposal methods for expired or unusable solder paste may vary depending on local regulations. It is recommended to consult with local authorities or waste management facilities for proper disposal procedures to ensure compliance with environmental guidelines. You may also consult your metals recycler to see if it can be recycled along with your dross.
A: Solder paste can be used for rework or repair applications, but it is important to assess the compatibility of the solder paste with the existing solder and components. Proper rework techniques and temperature profiles should be followed to ensure successful and reliable results.
A: No, unless there is evidence from the manufacturer that there is compatibility. Mixing can alter the paste’s properties and may lead to performance issues or reliability concerns.
A: Though modern solder pastes generally no longer contain lead, they still contain other metals and substances which may be harmful. Follow safety guidelines such as wearing appropriate personal protective equipment (PPE), ensuring good ventilation in the workspace, and avoiding direct contact with skin or eyes. Consult the safety data sheet (SDS) provided by the manufacturer for specific precautions and guidelines. Keep in mind that solder paste has a way of getting on everything in trace amounts. You might want to consider changing clothes and footwear when leaving the production environment.
A: Solder paste will usually survive unrefrigerated transport for up to 72 hours without issue. It may be packed with ice to ensure its integrity. Don’t be alarmed if ice packs are completely melted upon arrival. This is simply an indication that these packs did their job absorbing excess heat.