por Timothy O'Neill e Logan Jelinske
Resumo
Apesar das previsões do fim dos componentes com orifício de passagem, eles continuam sendo comuns em todo o setor. Entretanto, seu uso está em declínio e as montagens podem incorporar apenas um ou dois componentes com orifício de passagem. Uma técnica alternativa para soldar componentes com orifício de passagem, eliminando a necessidade de um processo de soldagem separado, é o método Pin-in-Paste (PiP) ou Intrusive Reflow. O PiP utiliza a impressão de pasta de solda e os processos de refluxo SMT para soldar dispositivos com furo passante. A técnica PiP pode ser mais econômica, pois elimina a necessidade de um processo de solda por onda ou seletiva e os custos associados. Este documento detalhará o processo PiP, incluindo considerações sobre o projeto de PCB e estêncil, bem como a seleção da pasta de solda e as diretrizes de refluxo.
Histórico
Como os dispositivos eletrônicos continuam a se tornar menores e mais capazes, os componentes com orifício passante são implementados com menos frequência, pois as restrições de espaço dos dispositivos modernos são a força motriz. No entanto, os dispositivos com orifício de passagem oferecem vantagens de desempenho em relação ao SMT, pois têm interconexões robustas com condutores compatíveis que aumentam a confiabilidade mecânica e elétrica. A solda PiP pode proporcionar um processo e um desempenho de produto equivalentes à solda por onda, seletiva e manual durante a montagem SMT, reduzindo assim o custo. A operação de uma máquina de solda por onda ou seletiva pode ser cara e a etapa adicional do processo pode ser eliminada. A PiP também pode eliminar a necessidade de equipamentos subutilizados e aumentar o espaço na área de produção.
Considerações sobre o PiP
As considerações para a implementação do PiP usando componentes de furo passante são:
- Os componentes são verificados quanto à capacidade de suportar as temperaturas do processo SMT e o método de inserção é estabelecido. Depois que a pasta de solda é impressa, os componentes podem ser colocados manualmente ou por inserção automatizada.
- O componente deve ter uma folga adequada para evitar que a solda entre em contato com a parte inferior do componente, um defeito de acordo com o IPC-610G 7.3.5.
- A relação entre chumbo e furo precisa ser a mais estreita possível. Uma relação grande entre o eletrodo e o furo resultará em um aumento no volume da pasta, em vazamentos e na possibilidade de a solda fluir para fora do furo de passagem durante o refluxo. Uma relação muito estreita entre o eletrodo e o furo resultará em preenchimento insuficiente do cilindro e problemas de inserção.
- O comprimento do cabo deve ser mantido o mais curto possível. O excesso de comprimento do eletrodo deslocará a pasta na inserção e poderá afastar a solda do cilindro, aumentando a necessidade de volume de solda.
Os requisitos de volume de pasta para obter o preenchimento adequado do cilindro devem ser equilibrados com os requisitos SMT para evitar pontes/curtos etc. A pasta de solda na máscara/sobreimpressão é uma técnica aceita para aumentar o volume de pasta, mas é limitada pelo espaçamento entre os componentes e outras características da placa. Além disso, a diversificação das opções de ligas pode afetar/reduzir a força de umedecimento e o pull-back necessários para que a sobreimpressão seja eficaz.
Os estênceis em etapas podem ser implementados para obter o preenchimento adequado do cilindro sem afetar negativamente outras juntas de solda. Os avanços nas técnicas de microssoldagem de estêncil de solda eliminaram muitas das inconsistências associadas às tecnologias anteriores. O jato de pasta de solda é um desenvolvimento recente que oferece um meio sem contato de aumentar o volume de pasta local. As pré-formas de solda também podem ser utilizadas para aumentar o volume de solda.
Pequenos ajustes no processo podem ser feitos para aumentar o preenchimento do cilindro experimentando as configurações da impressora, incluindo a impressão sem contato, manipulando a velocidade do rodo, a pressão, o ângulo de ataque e a contagem de cursos.
Cálculo do volume da junta de solda
O volume necessário da junta de solda, Vsé calculado pela diferença entre o volume do orifício de passagem e o volume do pino. A fórmula é a seguinte:
Volume da junta de solda = Volume do orifício de passagem - Volume do pino + (2 x volume do filete de solda)
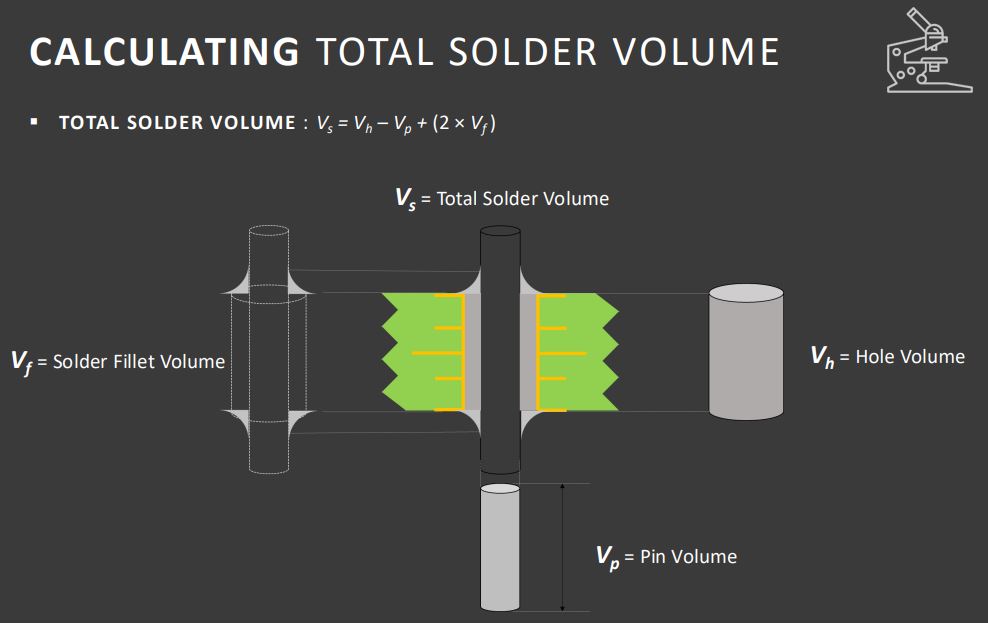
Essa fórmula levará em conta a quantidade de solda necessária para garantir o preenchimento adequado do cilindro do orifício de passagem. Para o volume do orifício de passagem, Vh:
Vh = πRo2H
Onde Ro é o raio do orifício de passagem e H é a altura do orifício de passagem ou a espessura da placa de circuito impresso. O volume do filete de solda, Vfpode ser calculado usando a seguinte fórmula, derivada do Teorema do Centroide de Pappus:
Vf = 2πA(0,2234R2 + Rt)
Onde o raio de filete, Ré igual à diferença entre o raio da almofada e o raio do pino (R = Rp-Rt). Área do filé, Aé igual a 0,215R2. Para calcular o volume do pino, Vp:
Vp = πRt2H
Uma vez Vh, Vfe Vp são calculados, a fórmula do volume da junta de solda se reduz ao seguinte:
Vs = Vh - Vp + (2 x Vf)
Como a pasta de solda é aproximadamente 50% de solda por volume, um fator de redução, FO fator de redução, que é necessário para determinar a quantidade de pasta de solda necessária. O fator de redução geralmente fica entre 0,45 e 0,55, dependendo da formulação da pasta de solda. A fórmula para calcular o volume de pasta de solda, Vspé:
Vsp = Vs/F
Aberturas de estêncil
Uma vez determinado o volume de pasta de solda, a próxima etapa é projetar o estêncil usado no processo. Para um projeto geral de abertura circular, use:
Vsp = πr2t
Onde r é o raio da abertura e t é a espessura do estêncil. Para uma abertura retangular geral, use:
Vsp = lwt
Onde l é o comprimento, w é a largura, e t é a espessura do estêncil. Use a aritmética para ajustar o raio das aberturas circulares ou o comprimento e a largura das aberturas retangulares para atender ao volume necessário de pasta de solda, Vsp. Dependendo da aplicação necessária, diferentes formatos de abertura podem ser benéficos. Como visto na Figura 2, vários formatos e tamanhos de abertura podem ser usados para aumentar o desempenho durante o processo.
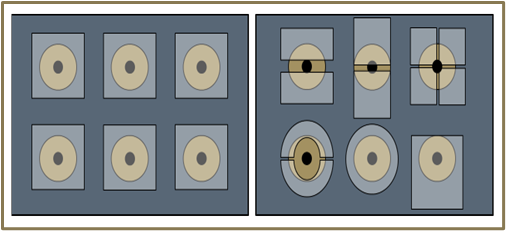
Considerações sobre PCB
O objetivo principal de um processo PiP é criar uma junta de solda de qualidade. Há várias considerações sobre o PCB que podem facilitar a implementação.
A almofada que envolve o cilindro deve ser a menor possível, mantendo as propriedades mecânicas adequadas. Em geral, isso corresponde a 2x o diâmetro do cilindro revestido. Isso tem a vantagem de reduzir a pasta necessária para atender ao padrão IPC-610G 4.3.2.1.
Outra consideração sobre a placa de circuito impresso é a relação entre o cabo e o furo. Como mencionado anteriormente, essa relação deve ser mantida a menor possível, mas deve levar em conta as tolerâncias do conector e da PCB para permitir variações na precisão do posicionamento e, ao mesmo tempo, exigir forças mínimas de inserção.
Para atender ao requisito de volume de solda para um processo PiP, é necessário imprimir a pasta de solda na máscara de solda da placa de circuito impresso, conforme mostrado na Figura 3. A impressão sobreposta na máscara de solda pode ser limitada pelo espaço e pela localização na PCB. A máscara de solda e o acabamento da superfície da almofada podem ter uma influência significativa no resultado. A máscara de solda com alta energia de superfície manterá a solda derretida plana, ao passo que a solda refluída em uma máscara com baixa energia de superfície tenderá a formar grânulos e poderá interferir no componente enquanto estiver líquido devido a um alto ângulo de umedecimento. A máscara de solda também deve ser aplicada ao cobre exposto para garantir que a solda derretida flua para dentro do cilindro e todas as vias que não sejam de teste devem ser protegidas. Além disso, acabamentos de superfície facilmente soldáveis, como HASL e ENIG, promoverão a umectação e melhorarão os resultados.
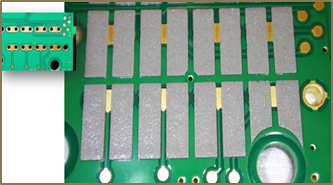
Seleção de pasta de solda
Uma variável importante na soldagem PiP é a pasta de solda em uso. Há várias propriedades da pasta que podem ter uma forte influência no sucesso da solda PiP. Algumas das mais significativas são o desempenho de queda a quente, o desempenho de umectação, o tipo de liga e as características dos resíduos. A queda a quente da pasta de solda é testada de acordo com o IPC TM-650 2.4.35 Sec. 5.2.2. Esse teste quantifica a capacidade de um depósito de pasta de solda de resistir à deformação a 150°C por 10-15 minutos. Essa é uma propriedade importante, pois a pasta que resiste à deformação tem menos probabilidade de cair e sair do cilindro antes de se tornar líquida. A pasta de solda com melhores propriedades de umectação melhorará a capacidade do processo e poderá superar alguns dos problemas mencionados anteriormente. A química do fluxo e a liga podem afetar o desempenho de umectação. Por exemplo, à medida que as ligas de baixa temperatura são investigadas, o impacto das propriedades de umectação no desempenho da PiP deve ser avaliado.
Considerações sobre refluxo
O perfil de refluxo da pasta de solda pode ser manipulado para afetar o resultado da qualidade da junta de solda para toda a montagem da placa de circuito impresso, não apenas para o componente PiP. Há uma série de considerações ao fazer ajustes de perfil para obter o melhor resultado possível. Os fatores de restrição mais comuns ao desenvolver um perfil de refluxo incluem recomendações de pasta de solda, limitações de temperatura do componente, características de massa térmica do conjunto, capacidade e limitações do forno. O perfil usado deve acomodar essas restrições e, ao mesmo tempo, atender aos objetivos de qualidade da aplicação.
Avaliação da qualidade
A qualidade da junta de solda PiP deve atender aos critérios da IPC-610 para as Classes 1, 2 e 3. O raio X não destrutivo e a seção transversal destrutiva podem fornecer evidências definitivas sobre o sucesso do processo.
Processos downstream
A incorporação de um processo PiP pode ter implicações inesperadas em vários processos de pós-refluxo. Como a pasta de solda é um fluxo 50% em volume, a adição de pasta adicional à PCB para realizar o preenchimento do cilindro pode aumentar significativamente a quantidade de resíduos de fluxo pós-solda. Lembre-se de que o fluxo líquido usado na solda por onda e na solda seletiva deixa muito pouco resíduo. O aumento do resíduo de pasta de solda pode causar vários problemas:
- Estética - Em termos simples, o aumento do resíduo de fluxo não é visualmente atraente.
- ICT - O aumento do resíduo de fluxo pode interferir no contato das sondas de teste com a área de teste, levando a "chamadas falsas". Pode ser necessário aumentar a manutenção do dispositivo de teste, a substituição da sonda e a limpeza.
- Forno de refluxo - O aumento da pasta leva à geração de mais voláteis de fluxo durante o processo de refluxo. Isso resulta no acúmulo de resíduos de fluxo no forno, causando maior limpeza do sistema de gerenciamento de fluxo e gotejamento de fluxo no forno de refluxo. Além disso, a pasta deslocada do cilindro durante o processo de inserção pode cair da ponta do pino e se acumular na parte inferior do forno de refusão.
- Resíduos de fluxo e/ou pasta de solda podem fluir para a extremidade do conector, o que pode violar os padrões de qualidade ou interferir nas limitações de folga e tolerância.
Conclusão
Os componentes com orifícios de passagem continuam sendo comuns e é improvável que sejam eliminados em um futuro próximo. Os montadores modernos estão constantemente adotando novos processos e otimizando os existentes. Está comprovado que o PiP pode ajudar a reduzir os custos operacionais, simplificar o processo de produção, reduzir o espaço ocupado pela linha de montagem e economizar energia. À medida que novas ligas, dispositivos menores e novas tecnologias são incorporadas, a PiP continua sendo uma técnica útil para o setor de montagem de PCBs.