Por Timothy O'Neill
Na montagem de placas de circuito impresso (PCB), a integridade da máscara de solda é fundamental. Essa camada protetora, projetada para proteger as superfícies de cobre e evitar a formação de pontes de solda entre os componentes, desempenha um papel fundamental para garantir a confiabilidade e a funcionalidade dos dispositivos eletrônicos.
No entanto, as máscaras de solda podem apresentar vários problemas, como fissuras, delaminação, descascamento e a presença de resíduos cerosos ou oleosos. Esses defeitos podem levar a complicações como microesferas de solda, pontes e rastros de caracol de solda, especialmente perceptíveis após processos de solda por onda.
Esses desafios não apenas comprometem a qualidade e a confiabilidade de longo prazo da PCB, mas também podem levar a um retrabalho significativo na produção e a um aumento nos custos.
Causas comuns de problemas com máscaras de solda
Os problemas com máscaras de solda podem ser causados por vários fatores, desde o processo de fabricação até os materiais usados. Aqui estão algumas causas comuns:
- Preparação inadequada da superfície: Para que uma máscara de solda adira adequadamente, a superfície da placa de circuito impresso deve estar limpa e livre de contaminantes. Qualquer resíduo ou oxidação/umidade pode afetar significativamente a adesão da máscara.
- Cura incorreta: As máscaras de solda requerem cura adequada para obter adesão e durabilidade ideais. As máscaras de solda com cura insuficiente são suscetíveis a qualquer líquido e podem ser facilmente danificadas durante o processo de soldagem devido à absorção do fluxo e à volatilização inadequada. Um endurecedor insuficiente na composição da máscara de solda também pode fazer com que ela nunca endureça totalmente após a cura.
- Porosidade da máscara de solda: Às vezes, as máscaras de solda podem apresentar porosidade, dependendo do tipo de máscara de solda usada, do processo de aplicação e do processo de cura. Produtos químicos, como fluxo e agentes de limpeza, bem como umidade, podem se infiltrar por esses pequenos orifícios. Isso pode levar a problemas de confiabilidade, bem como à corrosão ou a outros danos ao longo do tempo.
- Fatores ambientais: A máscara de solda pode absorver produtos químicos durante a fabricação de PCBs, que podem se tornar altamente higroscópicos ou corrosivos. Quando expostas às condições de campo, essas substâncias absorvidas podem causar falhas na PCB devido aos efeitos combinados de umidade, calor e estresse elétrico.
Quase todos os casos de delaminação da máscara de solda estão relacionados à própria placa de circuito impresso, e não ao fluxo ou ao equipamento usado no processo de montagem. Se a máscara de solda apresentar danos visíveis ou se houver resíduos oleosos ou cerosos presentes, isso pode indicar problemas de adesão ou cura inadequada da máscara ou, possivelmente, uma combinação de ambos os fatores.
Outros sinais de um problema incluem rastros de caracol de solda, microesferas de solda ou pontes após o processo de soldagem. É fundamental identificar e resolver esses problemas para evitar o comprometimento do desempenho e da integridade da placa de circuito impresso.
Aqui estão alguns testes simples que o engenheiro pode fazer no chão de fábrica para ajudar a identificar a causa raiz.
Verificação de adesão: O teste da fita
Esse teste envolve a aplicação de um pedaço de fita adesiva transparente de pelo menos 2 polegadas de comprimento. Pressione a fita na placa e puxe-a rapidamente para cima em um ângulo de aproximadamente 90 graus em relação à superfície da placa de circuito impresso (Figura 1). Se a fita puxar a máscara, você está diante de um problema de adesão. O método de teste oficial do IPC (2-4-28) indica a fita de ½ polegada da marca 3M (também conhecida como "Scotch"), mas, se não for essa a fita que está em seu dispensador, use a que estiver lá.
Se a máscara se levantar, observe a condição do cobre embaixo dela. Se o cobre estiver brilhante, é provável que não tenha sido preparado adequadamente para a aplicação da máscara de solda. Um acabamento fosco indica a limpeza e o desbaste adequados das superfícies antes da aplicação da máscara.
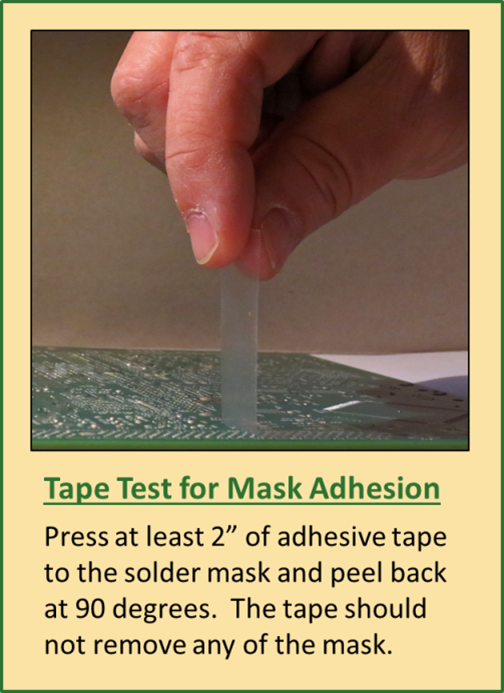
Verificações de cura e dureza
Você pode fazer os três testes a seguir para verificar a cura e a dureza da máscara.
O teste do lápis: Pegue um lápis de madeira e afie-o novamente. Segure-o em um ângulo de 45° e pressione-o firmemente para longe de você (Figura 2). Se a máscara de solda se levantar ou se abrir, ela não está suficientemente dura. Isso pode ser resultado de uma cura inadequada ou de um endurecedor insuficiente adicionado à máscara antes da cura.
O lápis que você usou provavelmente era um #2H (todos nós conhecemos esse tipo de lápis por causa dos testes padronizados). Os lápis são classificados em uma escala de dureza, e qualquer grafite classificado com menos de #6H não deve arranhar a máscara de solda. Se você quiser um #6H ou um kit completo de lápis de dureza variável, eles são vendidos em lojas de materiais de arte.
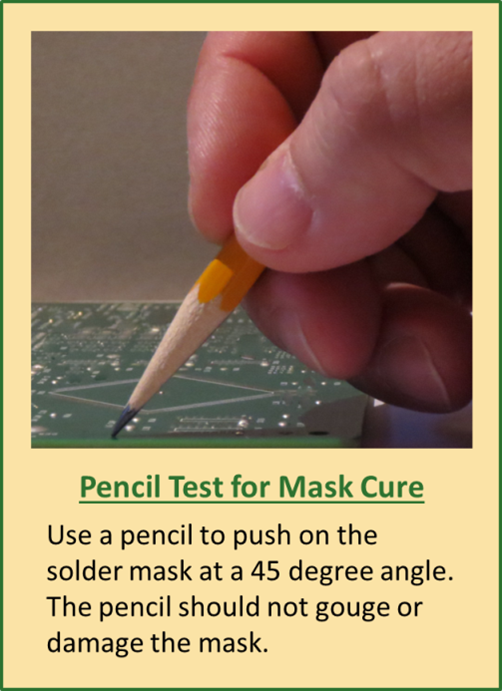
O teste de cozimento: Para realizar esse teste, coloque a placa de circuito impresso em um forno pré-aquecido a 175°C e permita que a temperatura da placa atinja 155°C. Uma vez nessa temperatura, mantenha a placa a 155°C por exatamente 60 minutos. Certifique-se de que o forno tenha ventilação adequada para remover quaisquer vapores e plastificantes nocivos, evitando que eles se redepositem nos acabamentos soldáveis, o que poderia resultar em problemas de umedecimento ou de umedecimento deficiente.
Se problemas como fissuras, delaminação e a presença de resíduos oleosos ou cerosos forem resolvidos após esse tratamento, isso indica que a máscara de solda estava com cura insuficiente e que o cozimento adicional ajudou a concluir o processo de cura.
No entanto, se os problemas persistirem, isso pode sugerir que a formulação da máscara de solda estava incorreta, possivelmente devido à adição de uma quantidade insuficiente de endurecedor durante a preparação.
Toalhetes de verificação da máscara de solda: A BLT Circuit Services oferece lenços de verificação de máscara de solda fáceis de usar. Esses lenços foram projetados para um teste qualitativo rápido para identificar a máscara de solda mal curada em PCBs. Para usar, remova um lenço da embalagem, certificando-se de que a embalagem esteja vedada novamente. Esfregue o pano na placa de circuito impresso com pressão moderada por cerca de 10 a 15 segundos em várias áreas.
Se a máscara de solda estiver mal curada, a cor da resistência será transferida para o pano, indicando problemas com a adesão ou a cura da máscara (Figura 3.). Se essa transferência ocorrer, isso sugere que a placa de circuito impresso pode ter defeitos e deve ser informada ao fornecedor para correção.
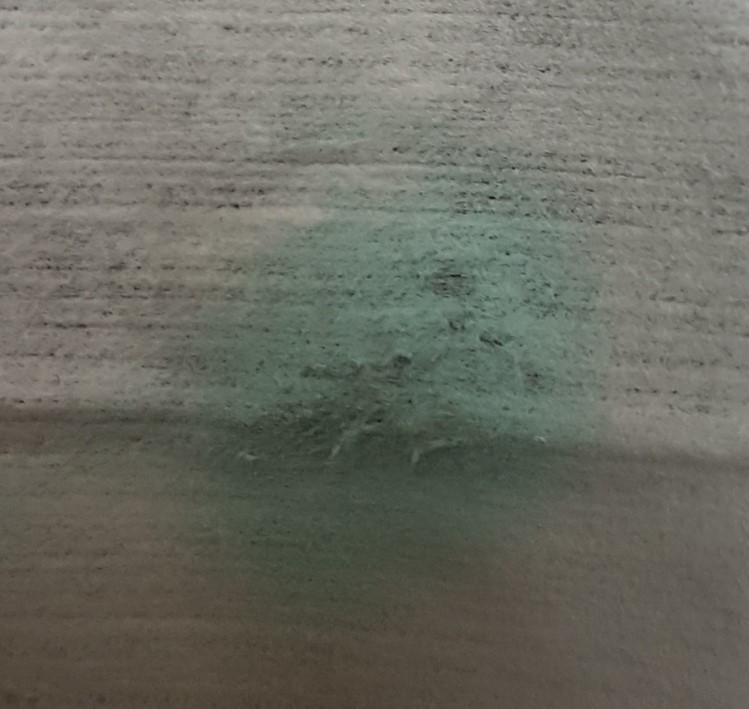
Estudo de caso: Como a química do fluxo pode agravar os problemas da máscara de solda
Embora os problemas com a máscara de solda normalmente resultem de problemas de aplicação que podem ser identificados pelas verificações descritas anteriormente, a interação entre a máscara e a química do fluxo também pode causar problemas em raras ocasiões. Aqui descrevemos uma situação em que o problema estava, pelo menos parcialmente, relacionado ao fluxo.
O problema
Nesse caso, um fluxo líquido parecia estar interagindo com a máscara de solda, fazendo com que ela parecesse nebulosa e enlouquecida, chegando até mesmo a levantá-la do substrato. O problema parecia ocorrer com mais frequência e gravidade ao redor dos traços. Uma análise do processo de solda por onda não indicou nenhuma etapa, parâmetro ou tempo de exposição incomum que pudesse causar danos à máscara de solda, e o fabricante da placa de circuito impresso insistiu que era um problema de fluxo.
Solução de problemas e testes de máscara de solda
Pedimos ao usuário que realizasse alguns dos testes simples de máscara de solda enquanto pesquisávamos o número do lote do fluxo para ver se havia alguma alteração na produção ou outras preocupações do cliente associadas a ele. Não encontramos nenhuma alteração ou preocupação registrada, mas esse fluxo em particular era um material altamente especializado e de lote pequeno. Levantamos a hipótese de que talvez algumas variações pudessem ter ocorrido durante sua vida útil, então testamos uma amostra enviada pelo usuário, mas novamente não encontramos problemas.
Enquanto isso, a máscara foi reprovada no teste de fita e no teste de limpeza da máscara de solda. Então, em nossa investigação mais aprofundada dos produtos químicos da máscara e do fluxo, descobrimos que a máscara era um produto mais novo, sem halogênio.
Identificação da causa
A composição exclusiva da máscara e a falta de cura suficiente fizeram com que ela permanecesse altamente porosa. Como resultado, o fluxo foi absorvido na subsuperfície da resistência de solda, onde não pôde se volatilizar adequadamente, como esperado, durante a fase de pré-aquecimento.
Quando a placa encontrava a onda de solda, o fluxo absorvido fervia entre a resistência e as camadas de cobre, prejudicando a adesão entre a resistência de solda e os trilhos de cobre da base. Essas informações, juntamente com as falhas no teste da máscara de solda, ajudaram o montador a demonstrar o problema ao fabricante da placa de circuito impresso e a encontrar uma solução.
Considerações finais
Não é incomum que o fornecedor de produtos químicos de solda conduza a análise da causa raiz dos problemas de solda. De fato, isso faz todo o sentido. A equipe de suporte técnico de soldagem vê tantos processos e problemas diferentes e variados que são solucionadores de problemas naturais e um ótimo recurso para os engenheiros de processo. A avaliação adequada do desempenho do material geralmente se baseia em testes baseados no conhecimento de causa e efeito que só é obtido por meio da experiência.
Um fornecedor de qualidade não deve tentar transferir a responsabilidade pelos problemas do processo para o final da linha, mas sim se comprometer a levar o cliente à solução mais rápida e eficaz, independentemente da falha. A estratégia de "passar a responsabilidade" pode ser um tiro pela culatra e prejudicar os negócios; no entanto, por alguma razão inexplicável, ela ainda é comumente implementada. Até que ela seja erradicada, continue chamando os soldadores; grande parte de nossa valiosa experiência é adquirida por meio dos desafios de nossos clientes.