ACONSELHAMENTO SOBRE APLICATIVOS DE DESTINO
Otimizado e aprovado pelo engenheiro
Recomendações de configuração de impressão de pasta de solda
As configurações de impressão são cruciais para a aplicação ideal de pasta de solda. Este guia fornece informações sobre os principais parâmetros, como snap-off, distância de separação, separação, velocidade, velocidade de impressão e pressão do rodo. A compreensão e o ajuste dessas configurações podem melhorar a qualidade e a confiabilidade da deposição de pasta de solda.
Configurações recomendadas para o Snap-Off: 0,00 (em contato)
O que é Snap-Off?
O snap-off refere-se ao espaço entre o substrato (placa de circuito impresso) e a tela ou estêncil. O ajuste da distância de snap-off ajuda a liberar a pasta de solda do estêncil e a controlar a quantidade de pasta depositada no substrato.
O papel do Snap-Off na aplicação de solda
Durante a impressão, a lâmina do rodo aplica pressão ao estêncil e veda a área que está sendo impressa. À medida que a lâmina passa, o estêncil retorna à distância de encaixe predefinida, separando-se da pasta de solda deixada no substrato.
O snap-off é principalmente uma herança dos dias de impressão por meio de telas, embora possa melhorar a liberação da pasta por meio de um estêncil mal cortado e ainda possa ser necessário para equipamentos ou aplicações específicas.
Considerações sobre a impressão Snap-Off
As distâncias positivas de encaixe podem afetar negativamente o efeito de "vedação" desejado, causando espalhamento da pasta e pontes entre as almofadas dos componentes. O snap-off também pode levar à deposição desigual de pasta e a resultados de impressão inconsistentes.
A configuração da distância de snap-off para 0,00 (impressão em contato) oferece benefícios como vedação total, evitando sangramento e formação de pontes, mesmo para componentes de passo fino. A impressão em contato também resulta em uma deposição de pasta mais uniforme e em uma altura de pasta consistente.
Como ajustar as configurações de Snap-Off
Para estabelecer a impressão de 0,00 snap-off (em contato), siga estas etapas:
- Selecione um substrato plano.
- Posicione o substrato sob o estêncil.
- Abaixe o estêncil ou levante a placa até a altura da impressão.
- Desligue qualquer vácuo que esteja segurando a placa.
- Ajuste o encaixe do estêncil para criar um espaço definido entre o estêncil e a superfície do substrato.
- Diminua lentamente a distância de encaixe, desviando o estêncil em direção ao substrato até que ele faça contato apenas com a área imprimível.
- Para impressoras manuais, trave a altura do estêncil e redefina os indicadores do mostrador para 0,00. Para impressoras automatizadas, registre a nova distância de encaixe e repita as etapas 2, 3 e 6 para verificar o ajuste.
Notas
Alguns equipamentos controlados por computador exigem calibração adicional para as configurações de snap-off. Sempre verifique seus ajustes. Além disso, lembre-se de verificar se toda a área da placa está em contato com o estêncil, principalmente as bordas externas. Examine o suporte da placa e certifique-se de que a placa não esteja deformada se o contato ocorrer prematuramente.
Distância de separação recomendada: 0,010″ a 0,050″ (0,25 a 1,25 mm), dependendo da espessura da placa, do encaixe e das configurações de downstop.
O que é distância de separação?
A distância de separação refere-se à distância que a torre Z, ou o suporte da placa, abaixa em uma velocidade controlada para limpar o estêncil antes de retornar à sua posição inicial. É importante separar cuidadosamente o estêncil da placa de circuito impresso após a impressão para garantir a separação limpa da pasta de solda das aberturas do estêncil. A distância de separação geralmente é percorrida em uma velocidade selecionada para ajudar nesse processo.
O papel da distância de separação na aplicação da solda
Após a conclusão do ciclo de impressão, a torre Z que está segurando o substrato impresso desce em uma velocidade especificada até a distância de separação definida. Depois de atingir essa distância, a torre Z desce em velocidade máxima até sua posição inicial. As vibrações em alguns suportes de placa, causadas pela rotação lenta do motor, também ajudam a liberar a pasta de solda.
Considerações sobre a distância de separação
A definição de uma distância de separação promove uma melhor liberação da pasta de solda das aberturas do estêncil. Isso também contribui para depósitos mais uniformes de pasta de solda e minimiza o pico. Embora o uso de uma distância de separação diminua o tempo total do ciclo de impressão, o impacto no tempo de produção é mínimo para pequenas distâncias de separação ou velocidades de separação mais rápidas, mas se torna mais significativo à medida que os limites se aproximam.
Como ajustar a distância de separação
Comece definindo a distância de separação no menu de configuração para 0,005" (0,125 mm) a mais do que a espessura do estêncil. Por exemplo, se a espessura do estêncil for 0,006″ (0,15 mm), defina a distância de separação inicial como 0,011″ (0,28 mm). Em seguida, execute as etapas a seguir:
- Abaixe o estêncil ou levante a placa até a altura da impressão.
- Certifique-se de que o vácuo que está segurando a placa esteja desligado.
- Ajuste a distância de separação gradualmente, garantindo a folga adequada entre o estêncil e o substrato.
- Verifique a distância de separação imprimindo e inspecionando a deposição da pasta de solda.
Observações: O ajuste fino da distância de separação pode ser necessário com base em equipamentos ou requisitos específicos. Teste e valide a distância de separação ajustada para garantir os melhores resultados.
Considere o impacto no tempo total de produção ao ajustar a distância de separação. Encontre um equilíbrio entre a liberação ideal da pasta e a impressão eficiente.
É essencial monitorar e manter a distância de separação para evitar problemas como manchas na pasta de solda ou liberação inadequada. Inspecione e limpe regularmente o estêncil e o equipamento para garantir o funcionamento adequado.
Velocidade de separação recomendada: 0,010″ a 0,020″ por segundo (0,254 mm a 0,508 mm por segundo), 1-2 ou 10-20% da velocidade do eixo para componentes de passo fino e micro-BGA. Para impressão não crítica, pode ser usada uma velocidade de 0,030″ a 0,050″ por segundo (0,762 mm a 1,27 mm por segundo), 3-5 ou 30-50%.
O que é velocidade de separação?
A velocidade de separação refere-se à velocidade medida na qual o rodo se separa do estêncil. Assim como a distância de separação, esse parâmetro foi projetado para ajudar na separação da pasta de solda das aberturas do estêncil. A velocidade de separação pode ser indicada em milhares de polegadas, milímetros ou como uma porcentagem da velocidade do eixo.
O papel da velocidade de separação na aplicação de solda
Após a conclusão do ciclo de impressão, o controle da velocidade de separação do rodo ajuda a obter uma separação limpa da pasta de solda das aberturas do estêncil. Uma velocidade de separação bem controlada contribui para depósitos de pasta consistentes e uniformes, minimizando defeitos e garantindo melhor qualidade da junta de solda. Ao ajustar cuidadosamente a velocidade de separação, você pode otimizar o processo de impressão para obter melhores resultados.
Considerações sobre a velocidade de separação
A definição de uma velocidade de separação adequada é fundamental para obter a aplicação ideal da pasta de solda. Ela ajuda a evitar problemas como "dog-ears" (orelhas de cachorro), "peaking" (picos), "wicking" (absorção) e cobertura inadequada da pasta. Embora velocidades de separação mais lentas sejam geralmente preferidas para melhor controle, é importante encontrar um equilíbrio entre a deposição confiável de pasta e a impressão eficiente. Considere fatores como tipos de componentes, projetos de placas e características da pasta de solda ao determinar a velocidade de separação adequada para sua aplicação.
Como ajustar a velocidade de separação
Para ajustar a velocidade de separação de forma eficaz, siga estas etapas:
- Acessar o menu de configuração ou as configurações do software.
- Localize o parâmetro de velocidade de separação.
- Comece definindo um valor conservador com base na faixa recomendada para sua aplicação específica.
- Execute uma impressão de teste e inspecione a deposição da pasta de solda quanto à qualidade e à consistência.
- Faça o ajuste fino da velocidade de separação gradualmente, levando em conta o desempenho e os resultados obtidos.
- Repita o processo de teste de impressão e inspeção até obter a aplicação desejada da pasta de solda.
Observações: O ajuste fino da velocidade de separação pode ser necessário com base em equipamentos ou requisitos específicos. Teste e valide a velocidade de separação ajustada para garantir os melhores resultados.
É essencial monitorar e manter a velocidade de separação para evitar problemas como manchas na pasta de solda ou liberação inadequada. Inspecione e limpe regularmente o estêncil e o equipamento para garantir o funcionamento adequado.
Ao imprimir com passo fino, ou seja, LGA, QFN e micro-BGA, defina a velocidade de separação como mínima.
Configurações de velocidade de impressão recomendadas: Dependendo da formulação e da viscosidade da pasta de solda, as velocidades máximas de impressão recomendadas variam de 25 a 200 mm por segundo (1 a 8 polegadas por segundo).
O que é velocidade de impressão?
A velocidade de impressão refere-se à velocidade na qual o conjunto do rodo se move pelo estêncil durante o ciclo de impressão.
O papel da velocidade de impressão na aplicação de solda
A velocidade de impressão deve ser definida em conjunto com outros parâmetros, como pressão do rodo, química da pasta, tamanho da abertura do estêncil, entre outros. O ajuste da velocidade de impressão é necessário para obter uma limpeza limpa da superfície do estêncil, especialmente ao usar pasta de solda de alta viscosidade em velocidades mais altas.
Considerações sobre a velocidade de impressão
A impressão em alta velocidade normalmente se refere a velocidades entre 4 e 8 polegadas por segundo (100 a 200 mm por segundo). A obtenção de uma boa qualidade de impressão em altas velocidades depende da seleção da viscosidade e da reologia corretas da pasta de solda, bem como do design adequado do estêncil.
Durante a impressão em alta velocidade, as forças de cisalhamento do rodo causam uma redução temporária da viscosidade (afinamento por cisalhamento) nas pastas de solda. Velocidades mais altas e o aumento da pressão do rodo exacerbam o afinamento por cisalhamento, podendo levar a um curto-circuito entre as almofadas se a pasta não retornar rapidamente à sua viscosidade normal. O preenchimento inadequado da abertura do estêncil e a cobertura insuficiente da almofada também podem ocorrer em altas velocidades.
A impressão em alta velocidade requer configurações adicionais de pressão e velocidade, que podem afetar os transdutores, os servomotores, as lâminas do rodo e a vida útil do estêncil. O principal benefício da impressão em alta velocidade é a redução do tempo de produção e o aumento do rendimento.
Como ajustar a velocidade de impressão
Devido ao número de variáveis envolvidas, recomenda-se consulte seu técnico da AIM Solder para obter orientação sobre o ajuste da velocidade de impressão.
Observações: Em geral, a impressão mais lenta resulta em melhor qualidade de impressão, mas isso deve ser equilibrado com as necessidades de produção. Ajuste a velocidade de impressão para otimizar o tempo de ciclo sem desacelerar o restante da linha de produção.
Considere a possibilidade de ajustar as configurações de impressão para uma taxa de ciclo sob demanda para minimizar o tempo de espera entre os ciclos. Essa otimização facilita a reologia estável da pasta de solda e melhora o tempo do ciclo de impressão.
Se forem necessárias altas velocidades de impressão para seu processo de produção, certifique-se de que sua pasta de solda seja projetada para suportar essas velocidades. O fornecimento de suporte adequado para a placa também pode minimizar a flexão durante o ciclo de impressão.
Pressão recomendada do rodo: 1 a 1,5 lb por polegada linear (0,45 a 0,70 kg por 25 mm) da lâmina do rodo
O que é pressão do rodo?
A pressão do rodo refere-se à pressão para baixo exercida pela lâmina do rodo sobre a superfície do estêncil durante o ciclo de impressão.
O papel da pressão da racleta na aplicação da solda
Durante o ciclo de impressão, o rodo empurra a pasta de solda pela área imprimível, preenchendo as aberturas e limpando a superfície do estêncil. A pressão adequada do rodo, distribuída uniformemente ao longo do comprimento da lâmina, garante uma altura de pasta consistente, controle de deposição uniforme e desgaste reduzido da lâmina e do estêncil.
Considerações sobre a pressão do rodo
Aplicar a quantidade certa de pressão é essencial para garantir depósitos consistentes e confiáveis de pasta de solda e, ao mesmo tempo, evitar possíveis problemas. A pressão excessiva pode causar danos aos estênceis, formação de moedas e ruptura da fita entre as aberturas de passo fino. Esses problemas podem afetar negativamente o processo de impressão e resultar em má qualidade da junta de solda. Por outro lado, o uso de pouca pressão pode resultar em saltos se o estêncil não for limpo adequadamente. É importante encontrar o equilíbrio entre aplicar pressão suficiente para o preenchimento do estêncil e evitar força excessiva que possa causar danos.
Como ajustar a pressão do rodo
Para estabelecer a pressão adequada do rodo, supondo que as lâminas estejam corretamente instaladas e ajustadas, siga estas etapas:
- Selecione um substrato plano.
- Posicione o substrato sob o estêncil.
- Ajuste a pressão do rodo de modo que o excesso de solda permaneça na área de abertura da superfície do estêncil após um ciclo de impressão.
- Aplique pasta de solda no estêncil e execute um ciclo de impressão.
- Observe a quantidade de pasta de solda restante na superfície do estêncil.
- Aumente ligeiramente a pressão do rodo e execute outro ciclo de impressão.
- Novamente, observe a quantidade de pasta de solda remanescente na superfície do estêncil, que deve ser um pouco menor do que na passagem anterior.
- Repita as etapas 6 e 7 até que apenas uma camada muito fina de pasta de solda permaneça visível na área de abertura da superfície do estêncil.
Observações: O ajuste de outros parâmetros de impressão, como a velocidade de impressão ou o design do estêncil, também pode influenciar a pressão necessária do rodo.
A inspeção e a manutenção regulares das lâminas do rodo garantem o desempenho ideal e a aplicação consistente da pressão.
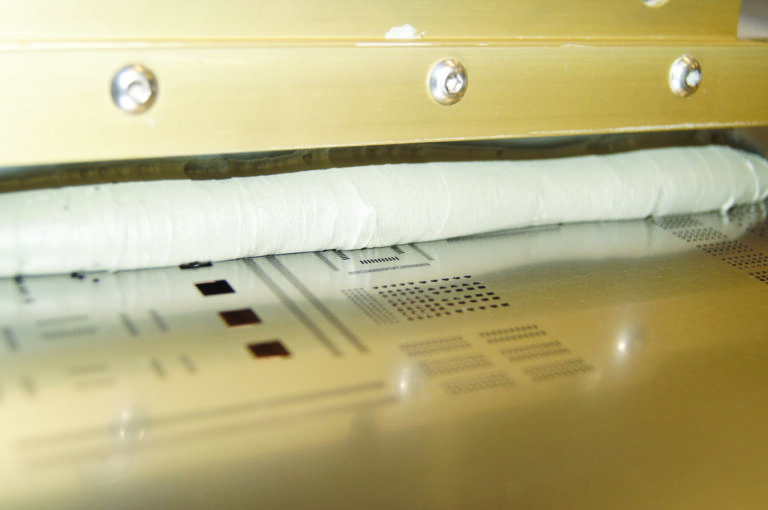