A pasta de solda - a gosma cinza que vem em um frasco, cartucho ou seringa - é aplicada às placas de circuito para fixar componentes e criar conexões elétricas. Ela vem com Instruções de armazenamento e manuseio. Ele requer refrigeração. Não é possível deixá-lo aberto por muito tempo, ou ele estragará. É preciso ajustar cuidadosamente as configurações do processo para otimizar seu desempenho.
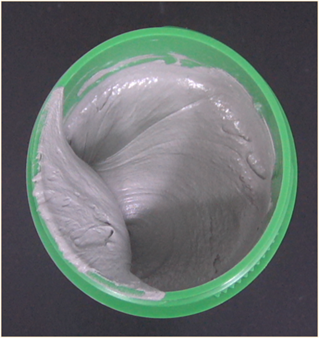
Mas por quê? De que é feita essa gosma cinza? Como ela é fabricada?
Noções básicas de pasta de solda
A pasta de solda é feita de pó de solda - pequenas esferas de metal ligado, combinadas com um meio de fluxo - resinas, resinas e outros produtos químicos projetados para promover a limpeza e evitar a oxidação.
Portanto, para fazer pasta de solda, você deve primeiro criar um liga. Em seguida, você deve transformar essa liga em pequenas esferas. Em seguida, você precisa de um meio de fluxo com a composição química correta. Por fim, você combina as pequenas esferas com o meio de fluxo em um ambiente cuidadosamente controlado.
O método exato pelo qual tudo isso é feito varia de um fabricante para outro, e os detalhes exatos costumam ser exclusivos e bem guardados. Dito isso, podemos lhe dar um esboço geral do processo.
Liga e atomização
Os processos de pré-atomização incluem a liga, o ensaio e a fundição do metal que será alimentado no atomizador. Um método de atomização envolve despejar um fluxo controlado de solda derretida em um disco giratório.
Quando o líquido atinge o disco, ele é desviado para gotículas que são formadas por tensão superficial em esferas individuais antes de congelarem, conforme mostrado no diagrama abaixo. Os parâmetros de atomização incluem temperatura de fusão, velocidade do disco, ambiente da câmara e outras variáveis que influenciam as principais características das partículas, como tamanho, forma e nível de óxido.
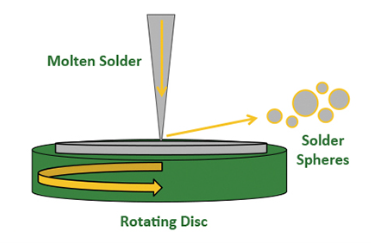
As operações de atomização geralmente são otimizadas para produzir um determinado tamanho de pó, sendo que as esferas fora da faixa desejada são consideradas subprodutos do processo. As formas esféricas são ideais, mas às vezes são formadas formas irregulares, como ossos de cachorro ou caudas, ou várias esferas se aglomeram. Essas geometrias indesejadas podem afetar a reologia e o desempenho de impressão de uma pasta de solda e são removidas no processamento subsequente.
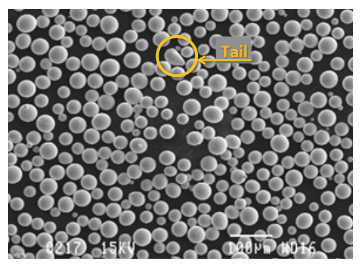
A oxidação é controlada pela manipulação dos níveis de gases inertes no ambiente de atomização.
Tamanhos/Tipos de pó de pasta de solda
As pastas de solda são classificadas com base na faixa de tamanho do pó de solda (pequenas esferas) que contêm. Os tamanhos de pó variam do Tipo 1 ao Tipo 10, sendo que os Tipos 3-6 são os mais usados atualmente na fabricação de produtos eletrônicos. O Tipo 4 é o tamanho mais popular no momento, com uma faixa de tamanho de partícula de 20 a 38 µm. Ele é capaz de imprimir 0201s e microBGAs.
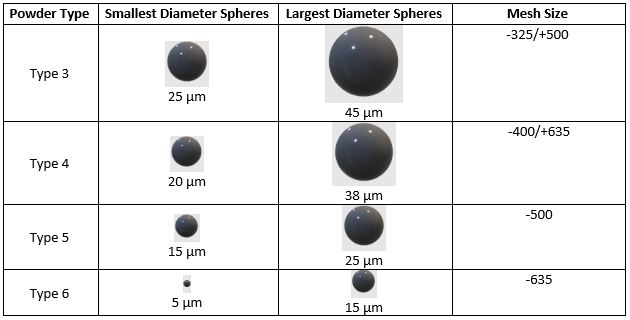
Quão pequeno é isso? Para referência, a espessura de um cabelo humano é de cerca de 100 µm e um glóbulo branco tem cerca de 10-20 µm de diâmetro. Portanto, essas partículas são realmente muito pequenas!
O pó tipo 5, com partículas de 15 a 25 µm, é adequado para aplicações mais finas, como QFNs e dispositivos 01005. Tipos 6 e menores se aventurar na ultraminiaturização, necessária para tecnologias de ponta.
Classificação e distribuição do tamanho do pó
Após a atomização, o pó é refinado e classificado por tamanho. Os métodos para fazer isso incluem classificação por ar e peneiramento.
O processo de classificação a ar segrega o pó de solda em diferentes classes com base na massa. O pó é soprado através de um fluxo de gás onde as partículas de tamanho alvo são concentradas. As partículas de tamanho menor são levadas pelo fluxo de gás e as partículas mais pesadas caem em uma área de coleta.
Esse processo permite a rápida peneiração do pó, onde as partículas de tamanho mais desejável estão fortemente concentradas. A classificação a ar torna a operação de peneiramento subsequente muito mais eficiente e eficaz.
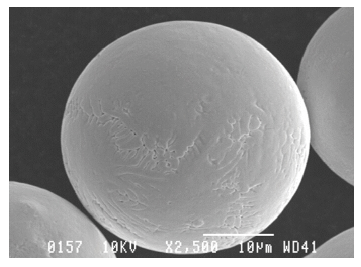
A peneiração separa o pó classificado usando peneiras grandes e vibratórias com telas progressivamente mais finas. As telas se correlacionam com o tamanho da malha que define o "tipo" de pó, conforme designado pela JEDEC e pela J-STD-005. A tabela da seção anterior mostra as classificações, tanto em termos de tamanho de malha para as peneiras quanto de tamanhos de partículas resultantes.
As esferas classificadas como Tipo 3, ou T3, passarão por uma tela de 325 mesh, mas não por uma tela de 500 mesh, daí o termo -325/+500. Isso equivale a tamanhos de partículas de 25 a 45 µm; 80% das partículas devem atender a esse requisito de tamanho. Da mesma forma, a pasta Tipo 4 passará por uma tela de 400 mesh, mas não por uma tela de 635 mesh, o que equivale a tamanhos de partículas de 20 a 38 µm.
Há uma sobreposição de tamanho entre as classes T3 e T4; portanto, a pasta de solda T4 pode oferecer uma ligeira vantagem na impressão de recursos finos sem apresentar problemas de refluxo.
No entanto, o tamanho da partícula cai rapidamente de 5 a 10 µm a 25 µm e, embora a capacidade de impressão de traços finos da pasta de solda tenha melhorado drasticamente, os efeitos dos óxidos de superfície podem começar a ser levados em conta; o prazo de validade pode ser afetado e o potencial para problemas de coalescência de refluxo aumenta.
Fluxo de pasta de solda
O fluxo é um agente químico que facilita a soldagem, limpando as superfícies metálicas, melhorando o fluxo da solda e evitando a oxidação durante o processo de refluxo.
O fluxo usado na pasta de solda é uma combinação de vários produtos químicos, incluindo ativadores, modificadores de reologia, solventes e plastificantes. A composição específica do fluxo depende da aplicação pretendida e das propriedades necessárias, como temperatura de ativação, viscosidade e requisitos de limpeza.
A etapa final: Combinação de pó com fluxo
A etapa final da fabricação da pasta de solda envolve a combinação de pó de liga de solda e fluxo em proporções específicas para garantir que a pasta seja uniforme e homogênea. A proporção típica é de cerca de 50/50 de fluxo para liga em volume ou 10/90 em peso, mas isso pode variar de acordo com os requisitos específicos da aplicação.
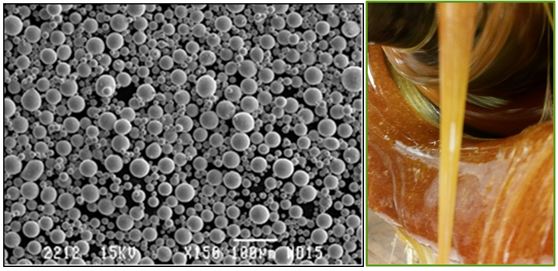
Os fabricantes de pasta de solda usam processos de mistura proprietários que envolvem misturadores cuidadosamente calibrados para garantir temperaturas estáveis e mistura consistente. Cada parte do processo é cuidadosamente medida, monitorada e mantida consistente de um lote para outro, garantindo que a pasta produzida seja uniforme e atenda a todas as especificações exigidas.
Após a mistura, a pasta é embalada em frascos, cartuchos ou seringas, dependendo de como será aplicada às placas de circuito.
O produto final é então submetido a testes rigorosos para garantir que atenda a todos os padrões relevantes. Isso inclui testes de viscosidade, slump, solder balling, umectação e prazo de validade, entre outros.
Mencionamos muito a oxidação. Do que se trata?
A oxidação é um processo químico natural que ocorre entre substâncias e o oxigênio do ar. Você vê oxidação o tempo todo - é o que faz com que maçãs fatiadas fiquem marrons quando deixadas em repouso, ou o que faz com que a ferrugem se forme em um carro velho. Ela também ocorre quando o metal em uma liga de solda entra em contato com o ar.
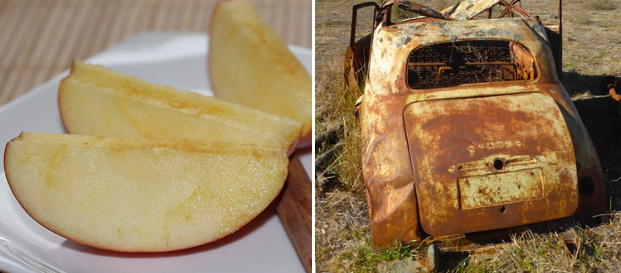
Quanto mais contato uma liga de solda tiver com o ar, maior será a propensão à oxidação. A oxidação também pode ser acelerada pela umidade, temperaturas mais altas e aquecimento. Quando as ligas de solda reagem com o oxigênio, elas formam uma camada de óxido em sua superfície. Essa camada de óxido é menos condutora e menos estável mecanicamente do que a liga pura, o que significa que dificulta a formação de boas conexões elétricas.
Por esse motivo, um dos principais objetivos ao criar e usar pasta de solda é minimizar a oxidação o máximo possível. De fato, uma das principais funções do meio de fluxo é remover os óxidos e evitar a oxidação. Ele faz isso por meio de interações químicas e também criando uma barreira entre o metal e o ar.
Essa propensão dos metais a reagir com o oxigênio é o motivo pelo qual a pasta de solda exige manuseio e armazenamento cuidadosos. É também por isso que o processo de fabricação da pasta deve ser cuidadosamente controlado. Muitas vezes, a formação do pó ocorre em um ambiente em que o oxigênio foi substituído por nitrogênio, um gás que não reage com o metal.
A propensão à oxidação é o motivo pelo qual alguns fabricantes usam atmosferas de nitrogênio durante o refluxo. E é também por isso que as pastas de solda mais finas são mais delicadas - quando o tamanho do pó fica menor, há uma proporção maior de área de superfície em relação à massa de metal. Como a oxidação ocorre na superfície, mais área de superfície significa mais chances de oxidação.
Palavras finais
Aí está! A gosma cinza é feita criando-se minúsculas esferas de liga metálica e combinando-as com uma pasta química otimizada para atenuar a oxidação e promover conexões elétricas fortes. A oxidação é inimiga tanto do processo quanto do produto final - e é o motivo das instruções de armazenamento e manuseio.