Se você já se deparou com as palavras Tipo 4, Tipo 5 ou T4, T5, T6 em relação a pasta de solda e se perguntou o que isso significava, você veio ao lugar certo.
Primeiro, observe que, embora pasta de solda A pasta de solda pode parecer uma bolha cinza uniforme, mas na verdade é uma mistura cuidadosamente projetada de metal em pó e um meio viscoso chamado fluxo. O pó confere à pasta de solda sua estrutura e funcionalidade, enquanto o fluxo permite que ela flua e adira aos componentes durante o refluxo.
Quando alguém fala sobre "pasta de solda tipo 4" ou "pasta T4", está se referindo ao tamanho das partículas de metal em pó dentro da pasta
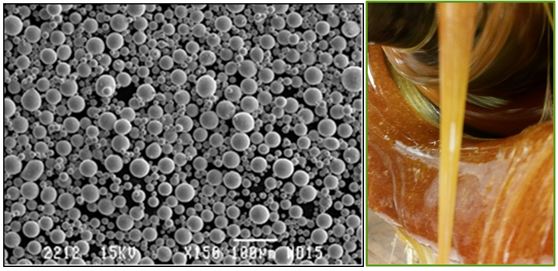
Neste artigo, descrevemos o que são os diferentes tamanhos de pó e por que temos esses diferentes tamanhos de pó em primeiro lugar.
Uma visão geral dos tamanhos relativos
Quando você dá um zoom microscópico, o pó assume a forma de pequenas esferas. Para cada tamanho ou tipo de pó, há um tamanho mínimo e máximo de esfera que o define. Esses tamanhos de esfera são medidos em micrômetros, sendo que 1 micrômetro (µm) = 0,000001 metro. A tabela abaixo mostra o tamanho mínimo e máximo da esfera para cada tipo de pó e dá uma ideia dos tamanhos relativos dessas esferas.
A pasta ou o pó de solda é classificado em uma escala que vai do Tipo 1 (maior) ao Tipo 10 (menor). Talvez isso seja contraintuitivo a princípio, pois 10 é um número maior que 1, mas se começássemos com 10 e quiséssemos fazer partículas cada vez menores, não poderíamos continuar depois de chegar a 1. Em contrapartida, podemos, no futuro, continuar aumentando o número - Tipo 11, Tipo 12 etc. - embora esses tipos ainda não existam de fato.
Como referência, o pó Tipo 1, que varia de 75 a 150 µm, tem aproximadamente o mesmo diâmetro de um fio de cabelo humano. O pó tipo 10, que varia de 1 a 3 µm, tem o tamanho aproximado de uma bactéria ou de uma organela celular.
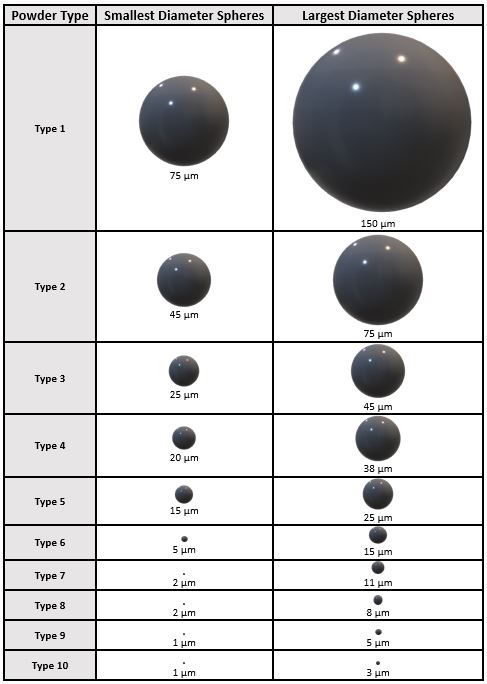
Por que o tamanho do pó é importante?
O tamanho das partículas de pó afeta o desempenho da pasta de solda em aplicações do mundo real. As partículas menores permitem que a pasta de solda flua através de aberturas de estêncil mais finas, o que é essencial à medida que os componentes e as placas de circuito impresso ficam menores. No entanto, as partículas mais finas também têm desvantagens, como serem mais propensas à oxidação e exigirem controles de processo mais rigorosos.
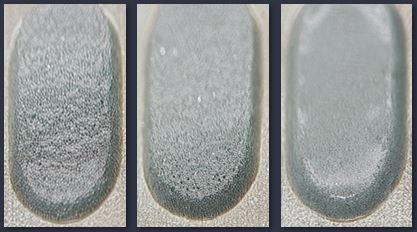
As necessidades do setor de eletrônicos estão sempre mudando, assim como seus padrões. Há pouco tempo, a pasta de solda Tipo 3 (tamanho de partícula: 25-45 µm) era a norma. Ela funcionava bem para componentes maiores, como 0805s e 0603s.
À medida que os componentes foram ficando menores e mais apertados, o Tipo 4 (20-38 µm) se tornou o padrão de referência, suportando passos mais finos, como 0201s e BGAs de 0,5 mm. Atualmente, o Tipo 4 domina a maioria das linhas de montagem SMT.
Mas a miniaturização não está diminuindo. Agora, estamos vendo uma mudança em direção ao Tipo 5 (15-25 µm) e até mesmo pós mais finos, como o Tipo 6 (5-15 µm) para tecnologias de ponta, como microLEDs, pacotes em escala de chip e projetos avançados de sistema em pacote (SiP).
Como escolher o tamanho certo do pó
Esta é uma regra geral: Use o maior tamanho de pó que sua aplicação permitir. Os pós menores oferecem precisão, mas têm desvantagens como custo mais alto e requisitos de processo mais rígidos.
Para orientar sua decisão, considere:
- A regra da bola 5: A menor abertura do estêncil deve ter pelo menos cinco vezes o diâmetro da maior partícula de pó. Por exemplo, o Tipo 4 pode lidar com aberturas de até ~190 µm, enquanto o Tipo 5 pode lidar com ~125 µm.
- Seus componentes: Se estiver trabalhando com 0201s ou BGAs de 0,5 mm, o Tipo 4 geralmente é suficiente. Para 01005s ou componentes de passo ultrafino, pode ser necessário o Tipo 5 ou mais fino.
- Seu equipamento: Os processos de impressão e refluxo podem precisar de ajustes para pós mais finos, como a redução da pressão do rodo ou a otimização das atmosferas de refluxo.
Para obter informações mais detalhadas, talvez você queira ler nosso artigo técnico Pasta de solda em pó: quando reduzir o tamanho.
Considerações finais
À medida que os eletrônicos continuam a encolher, o tamanho do pó da pasta de solda está se tornando mais importante do que nunca. Entender o tamanho necessário - e por quê - pode ajudá-lo a evitar problemas de produção e garantir resultados de montagem confiáveis.
Na AIM Solder, temos fabricado e aperfeiçoado pós de solda há décadas, oferecendo uma linha completa do Tipo 3 ao Tipo 7 e muito mais. Não importa se você está usando o padrão do setor, o Tipo 4, ou se está passando para pós mais finos, estamos aqui para ajudá-lo a fazer a escolha certa para as suas necessidades de fabricação.
Entender o tamanho do pó da pasta de solda pode parecer um pequeno detalhe, mas no mundo da eletrônica, esses detalhes fazem toda a diferença. Tem mais perguntas? Entre em contato conosco - estamos aqui para ajudá-lo a soldar de forma mais inteligente, não mais difícil!