A alternativa SAC305 de menor custo e melhor desempenho que você estava procurando
Este artigo explora REL61na evolução da solda sem chumbo, as vantagens exclusivas de sua formulação enriquecida com bismuto e seu desempenho em comparação com alternativas amplamente utilizadas, como a SAC305. Além disso, abordaremos seus casos de uso ideais, suas limitações e sua disponibilidade como uma solução versátil e global.
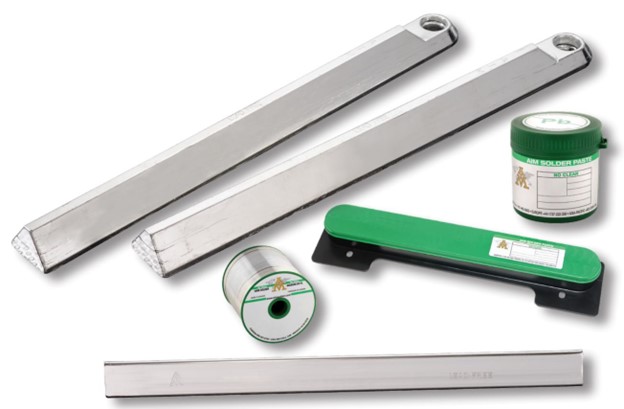
REL61 na evolução das ligas sem chumbo
Desde que as normas ambientais e os padrões do setor começaram a eliminar gradualmente as soldas tradicionais com chumbo, os fabricantes têm buscado alternativas que combinem confiabilidade, economia e facilidade de uso. Na primeira geração da transição sem chumboO SAC305 surgiu como um dos principais concorrentes. Embora continue popular até hoje, ele tem suas desvantagens, incluindo custo, fadiga térmica e outros problemas de desempenho.
Entre no REL61: A liga sem chumbo de terceira geração da AIM Solder, projetada para superar seus antecessores e atender às diversas necessidades da fabricação moderna. A REL61 é uma liga à base de SAC com baixo teor de prata que contém uma pequena porcentagem de bismuto.
Entendendo a função do bismuto
Embora o bismuto ofereça benefícios notáveis, sua adoção como componente de solda foi inicialmente limitada. Quando o bismuto e o chumbo se combinam, eles formam um eutético frágil e de fusão muito baixa. Portanto, se houvesse algum chumbo em um processo ou em componentes, o bismuto simplesmente não poderia ser usado.
Hoje, no entanto, os processos totalmente livres de chumbo se tornaram a norma em muitas instalações, colocando o bismuto novamente em consideração como um elemento prospectivo.
Algumas pessoas podem estar familiarizadas com o bismuto como um elemento comum em ligas de solda de baixa temperatura. Nesse espaço, ele ganhou uma infeliz reputação de fragilidade. Mas, embora seja verdade que, como principal constituinte das soldas de baixa temperatura, o bismuto contribui para a fragilidade, essas preocupações não se aplicam quando ele é usado como um aditivo menor em formulações de solda de alta confiabilidade.
De fato, em pequenas porcentagens, normalmente em torno de 1-6%, o bismuto realmente melhora o desempenho da solda em vez de prejudicá-lo. Nessas baixas concentrações, o bismuto atua para refinar a microestrutura da liga, melhorando propriedades como força, estabilidade térmica e até mesmo resistência à fadiga.
É por isso que o REL61, com sua composição SAC+Bi, tende a superar o SAC305 tradicional e outras alternativas com baixo teor ou sem prata na maioria das métricas. Melhor ainda, devido ao seu baixo teor de prata, ele custa 10-20% menos que o SAC305.
Comparação do REL61 com outras ligas sem chumbo
O REL61 foi projetado especificamente como uma alternativa de baixo custo para o SAC305 que ainda oferecia desempenho. Mas o resultado final foi que ele realmente superou o SAC305 e muitos outros produtos de 1st e 2nd ligas de geração.
O gráfico abaixo mostra como o REL61 se compara em termos de resistência à tração com outras ligas. Ele não só começa forte quando fundido pela primeira vez, mas também não perde resistência após o envelhecimento, como as outras ligas testadas.
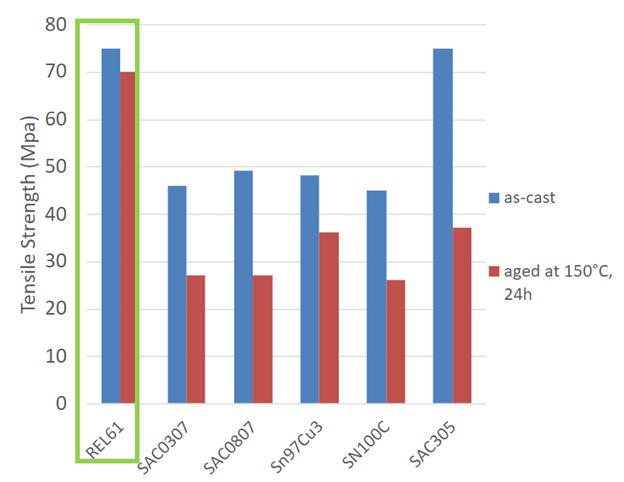
O motivo da resistência à fadiga térmica pode ser atribuído à microestrutura. A imagem a seguir mostra que, quando fundidos, tanto o SAC305 quanto o REL61 são semelhantes. Porém, depois de envelhecer a 150 °C por um dia, a diferença é bastante notável. O SAC305 forma estruturas em grande escala que contribuem para a falha, enquanto o REL61 não.
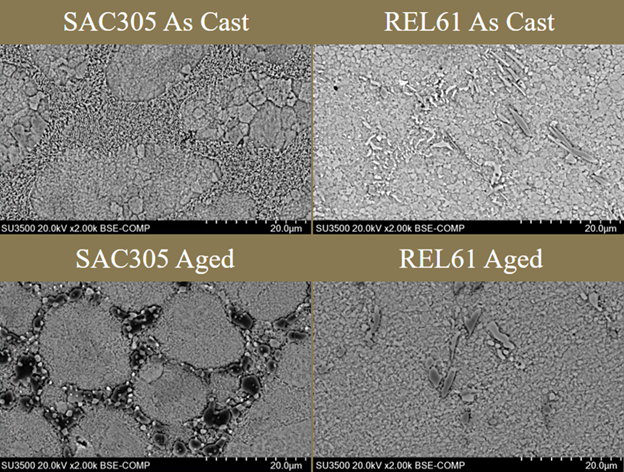
Apenas alguns dos benefícios adicionais do REL61 em relação ao SAC305 e ligas similares incluem
- Dureza aprimorada: O REL61 é quase duas vezes mais difícil que o SAC305
- Desempenho aprimorado de ciclagem térmica: O REL61 tem desempenho de 1 a 1,5 vezes melhor do que o SAC305 em testes de ciclo térmico
- Desempenho aprimorado de choque térmico: Após 1500 ciclos, 40% das juntas SAC305 falharam, em comparação com 0% das juntas REL61. Após 3000 ciclos, 80% de SAC305 falharam, em comparação com 40% de juntas REL61.
- Melhor preenchimento de furos em aplicações seletivas e de ondas: Muitos estudos demonstraram melhor preenchimento de furos e consistência com o REL61.
- Menos lixo: Em um estudo interno que comparou a geração de escória de várias ligas, o REL61 superou o SAC305, o SN100C e outras ligas com baixo teor de prata ou sem prata.
O que é e o que não é o REL61
O que é REL61
- Uma alternativa econômica para o SAC305: O REL61 representa uma solução de última geração para fabricantes que buscam uma alternativa econômica e de alto desempenho para o SAC305.
- Bom desempenho: O REL61 supera o SAC305 e muitas outras ligas com baixo teor de prata ou sem prata.
- Versátil: O REL61 é isento de fósforo, garantindo compatibilidade com processos de soldagem seletiva e oferecendo desempenho excepcional nas formas de barra, fio e pasta.
- Compatível sem chumbo: O REL61 é compatível com a maioria dos elementos em ambientes sem chumbo, incluindo ligas SAC, acabamentos de níquel e traços de germânio.
O que o REL61 não é
Apesar de seus muitos pontos fortes, o REL61 não está isento de limitações:
- Não compatível com ligas com chumbo: Para ambientes mistos onde pode haver solda com chumbo, SAC305 continua sendo a melhor opção. O uso de REL61 nesses ambientes pode resultar em juntas frágeis devido a incompatibilidades com o chumbo.
- Não é de alta confiabilidade: Embora o REL61 supere o SAC305 e outras ligas semelhantes em muitas métricas, ele não é classificado como uma liga de alta confiabilidade. Para aplicações que exigem o máximo de confiabilidade, como aeroespacial ou automotiva, a AIM Solder recomenda sua liga de alta confiabilidade REL22 como a solução ideal.
Aplicativos e disponibilidade
As propriedades excepcionais do REL61 o tornam adequado para uma ampla gama de aplicações, inclusive:
- Solda seletiva: Sua formulação sem fósforo minimiza o entupimento dos bicos e garante um desempenho consistente.
- Solda por onda: A formação mínima de escória, os requisitos mais baixos de temperatura da panela e a excelente umectação tornam o REL61 ideal para a produção de alto volume.
- Tecnologia de montagem em superfície (SMT): O REL61 em forma de pasta oferece resultados confiáveis para montagens SMT, garantindo juntas de alta qualidade e processamento eficiente.
- Solda robótica e manual: O REL61 também está disponível em fios sólidos e fluxados com diferentes porcentagens de fluxo para aplicações de soldagem robótica e manual.
Disponibilidade global
A rede de fabricação global da AIM Solder garante fornecimento e suporte consistentes para a REL61. Com instalações de produção e parceiros de distribuição em todo o mundo, os clientes podem contar com a AIM para atender às suas demandas, independentemente do local. O compromisso da AIM com a qualidade, combinado com sua equipe de suporte técnico, garante a integração perfeita do REL61 em qualquer linha de produção.
Centenas de fabricantes em todo o mundo já adotaram o REL61 com resultados excepcionais, destacando sua eficácia e versatilidade em todos os setores.
Conclusão
A escolha da REL61 para suas necessidades de soldagem proporciona o equilíbrio perfeito entre desempenho, custo e inovação. Para saber mais ou solicitar uma cotação, entre em contato com AIM Solder hoje.