Timothy O'Neill i Logan Jelinske
Streszczenie
Pomimo przewidywań dotyczących upadku komponentów z otworami przelotowymi, pozostają one powszechne w całej branży. Jednak ich użycie spada, a zespoły mogą zawierać tylko jeden lub dwa elementy przelotowe. Alternatywną techniką lutowania elementów przewlekanych, eliminującą potrzebę oddzielnego procesu lutowania, jest metoda Pin-in-Paste (PiP) lub Intrusive Reflow. PiP wykorzystuje drukowanie pasty lutowniczej i procesy rozpływowe SMT do lutowania urządzeń z otworami przelotowymi. Technika PiP może być bardziej opłacalna dzięki wyeliminowaniu konieczności stosowania procesu lutowania na fali lub lutowania selektywnego i związanych z tym kosztów. W niniejszym artykule szczegółowo omówiono proces PiP, w tym kwestie związane z projektowaniem płytek drukowanych i szablonów, a także wybór pasty lutowniczej i wytyczne dotyczące ponownego rozpływu.
Kontekst
W miarę jak urządzenia elektroniczne stają się coraz mniejsze i bardziej wydajne, komponenty przewlekane są wdrażane coraz rzadziej, a siłą napędową są ograniczenia przestrzenne nowoczesnych urządzeń. Jednak urządzenia z otworami przelotowymi oferują przewagę wydajności nad SMT, ponieważ mają solidne połączenia ze zgodnymi przewodami, które zwiększają niezawodność mechaniczną i elektryczną. Lutowanie PiP może zapewnić równoważną wydajność procesu i produktu z lutowaniem na fali, selektywnym i ręcznym podczas montażu SMT, zmniejszając w ten sposób koszty. Obsługa maszyny do lutowania na fali lub selektywnego może być kosztowna, a dodatkowy etap procesu można wyeliminować. PiP może również wyeliminować potrzebę niewykorzystanego sprzętu i zwiększyć przestrzeń na hali produkcyjnej.
Rozważania dotyczące PiP
Rozważania dotyczące implementacji PiP przy użyciu elementów przewlekanych są następujące:
- Komponenty są weryfikowane pod kątem odporności na temperatury procesu SMT i ustalana jest metoda wstawiania. Po wydrukowaniu pasty lutowniczej komponenty mogą być umieszczane ręcznie lub automatycznie.
- Komponent musi mieć odpowiedni prześwit, aby zapobiec kontaktowi lutowia z dolną częścią komponentu, co jest wadą zgodnie z IPC-610G 7.3.5.
- Stosunek ołowiu do otworu musi być tak mały, jak to tylko możliwe. Zbyt duży stosunek ołowiu do otworu spowoduje zwiększenie objętości pasty, powstawanie pustych przestrzeni i możliwość wypłynięcia lutowia z otworu przelotowego podczas rozpływu. Zbyt mały stosunek ołowiu do otworu spowoduje niewystarczające wypełnienie cylindra i problemy z wkładaniem.
- Długość przewodu powinna być jak najkrótsza. Nadmierna długość przewodu spowoduje wyparcie pasty podczas wkładania i może odprowadzić lut z cylindra, zwiększając zapotrzebowanie na objętość lutowia.
Wymagania dotyczące objętości pasty w celu uzyskania odpowiedniego wypełnienia beczki muszą być zrównoważone z wymaganiami SMT, aby zapobiec mostkowaniu/zwarciom itp. Pasta lutownicza na masce/nadruku jest akceptowaną techniką zwiększania objętości pasty, ale jest ograniczona odstępami między komponentami i innymi cechami płytki. Dodatkowo, zróżnicowanie opcji stopów może wpływać / zmniejszać siłę zwilżania i odciągania wymaganą do skutecznego nadruku.
Szablony krokowe mogą być wdrażane w celu uzyskania odpowiedniego wypełnienia beczki bez negatywnego wpływu na inne połączenia lutowane. Postępy w technikach mikrospawania szablonów lutowniczych wyeliminowały wiele niespójności związanych z wcześniejszymi technologiami. Rozpylana pasta lutownicza jest najnowszym osiągnięciem, które zapewnia bezdotykowy sposób zwiększania lokalnej objętości pasty. Preformy lutownicze mogą być również wykorzystane do zwiększenia objętości lutowia.
Drobne korekty procesu można wprowadzić w celu zwiększenia wypełnienia cylindra poprzez eksperymentowanie z ustawieniami drukarki, w tym druk bezdotykowy, manipulowanie prędkością rakli, ciśnieniem, kątem natarcia i liczbą skoków.
Obliczanie objętości złącza lutowniczego
Wymagana objętość złącza lutowniczego, Vsjest obliczana na podstawie różnicy objętości otworu przelotowego i objętości sworznia. Wzór jest następujący:
Objętość połączenia lutowanego = objętość otworu przelotowego - objętość sworznia + (2 x objętość spoiny lutowniczej)
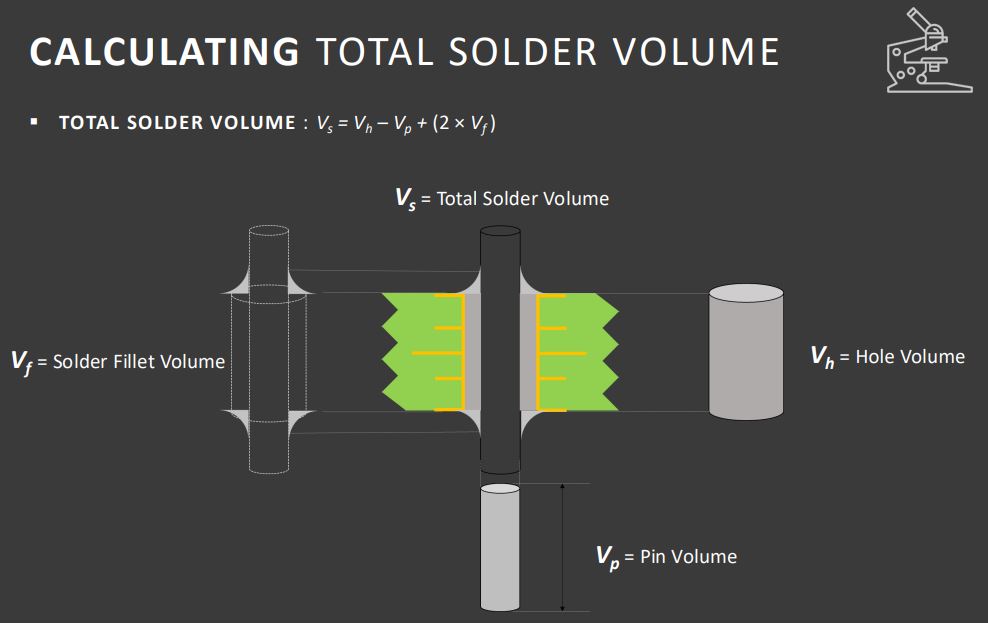
Wzór ten uwzględnia ilość lutowia potrzebną do prawidłowego wypełnienia otworu przelotowego. Dla objętości otworu przelotowego, Vh:
Vh = πRo2H
Gdzie Ro to promień otworu przelotowego, a H to wysokość otworu przelotowego lub grubość płytki drukowanej. Objętość zaokrąglenia lutu, Vfmożna obliczyć za pomocą następującego wzoru, wyprowadzonego z twierdzenia Pappusa o centroidach:
Vf = 2πA(0,2234R2 + Rt)
Gdzie promień zaokrąglenia, Rjest równa różnicy promienia podkładki i promienia sworznia (R = Rp-Rt). Obszar filetu, Awynosi 0,215R2. Aby obliczyć objętość szpilki, Vp:
Vp = πRt2H
Raz Vh, Vforaz Vp jest obliczana, wzór na objętość złącza lutowniczego sprowadza się do poniższego:
Vs = Vh - Vp + (2 x Vf)
Ponieważ pasta lutownicza ma objętość około 50% lutu, współczynnik redukcji, Fjest potrzebny do określenia ilości potrzebnej pasty lutowniczej. Współczynnik redukcji wynosi zazwyczaj od 0,45 do 0,55 w zależności od składu pasty lutowniczej. Wzór na obliczenie objętości pasty lutowniczej, Vspjest:
Vsp = Vs/F
Otwory szablonu
Po określeniu objętości pasty lutowniczej, następnym krokiem jest zaprojektowanie szablonu używanego w procesie. W przypadku ogólnego projektu okrągłego otworu należy użyć:
Vsp = πr2t
Gdzie r to promień przysłony, a t to grubość szablonu. Dla ogólnego prostokątnego otworu należy użyć:
Vsp = lwt
Gdzie l to długość, w to szerokość, a t to grubość szablonu. Użyj arytmetyki, aby dostosować promień dla okrągłych otworów lub długość i szerokość dla prostokątnych otworów, aby uzyskać wymaganą objętość pasty lutowniczej, Vsp. W zależności od wymaganego zastosowania, korzystne mogą być różne kształty otworów. Jak widać na rysunku 2, różne kształty i rozmiary otworów mogą być stosowane w celu zwiększenia wydajności podczas procesu.
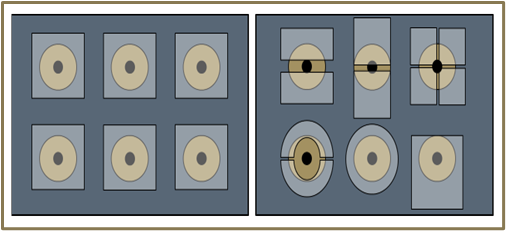
Uwagi dotyczące PCB
Głównym celem procesu PiP jest stworzenie wysokiej jakości połączenia lutowanego. Istnieje kilka czynników PCB, które mogą ułatwić wdrożenie.
Podkładka otaczająca lufę powinna być jak najmniejsza przy zachowaniu odpowiednich właściwości mechanicznych. Ogólnie rzecz biorąc, jest to 2x średnica platerowanego cylindra. Ma to tę zaletę, że zmniejsza ilość pasty wymaganej do spełnienia normy IPC-610G 4.3.2.1.
Kolejną kwestią związaną z płytką drukowaną jest stosunek wyprowadzeń do otworów. Jak wspomniano wcześniej, powinien on być jak najmniejszy, ale powinien uwzględniać tolerancje złącza i płytki drukowanej, aby umożliwić zmienność dokładności umieszczenia, wymagając jednocześnie minimalnych sił wkładania.
Aby spełnić wymagania dotyczące objętości lutowia dla procesu PiP, konieczne jest drukowanie pasty lutowniczej na masce lutowniczej PCB, jak pokazano na rysunku 3. Nadruk na masce lutowniczej może być ograniczony przez przestrzeń i lokalizację na płytce drukowanej. Maska lutownicza i wykończenie powierzchni padu mogą mieć znaczący wpływ na wynik. Maska lutownicza o wysokiej energii powierzchniowej będzie utrzymywać stopiony lut płasko, podczas gdy lut rozpływowy na masce o niskiej energii powierzchniowej będzie miał tendencję do perełek i może zakłócać działanie komponentu podczas liquidus ze względu na wysoki kąt zwilżania. Maska lutownicza powinna być również nałożona na odsłoniętą miedź, aby zapewnić przepływ stopionego lutowia do cylindra, a wszystkie nietestowe przelotki powinny być namiotowe. Dodatkowo, łatwo lutowalne wykończenia powierzchni, takie jak HASL i ENIG, będą promować zwilżanie i poprawiać wyniki.
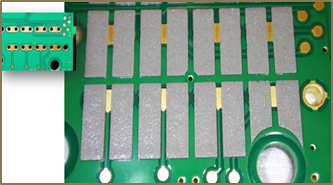
Wybór pasty lutowniczej
Kluczową zmienną w lutowaniu PiP jest używana pasta lutownicza. Istnieje wiele właściwości pasty, które mogą mieć duży wpływ na powodzenie lutowania PiP. Niektóre z najbardziej znaczących to wydajność opadania na gorąco, wydajność zwilżania, rodzaj stopu i charakterystyka pozostałości. Odpadanie pasty lutowniczej na gorąco jest testowane zgodnie z IPC TM-650 2.4.35 Sec. 5.2.2. Test ten określa zdolność osadu pasty lutowniczej do odporności na odkształcenia w temperaturze 150°C przez 10-15 minut. Jest to istotna właściwość, ponieważ pasta, która jest odporna na opadanie, jest mniej podatna na wypadnięcie z beczki, zanim stanie się płynna. Pasta lutownicza o lepszych właściwościach zwilżających poprawi wydajność procesu i może przezwyciężyć niektóre z wyżej wymienionych problemów. Chemia topnika i stopu może mieć wpływ na wydajność zwilżania. Na przykład, gdy badane są stopy niskotemperaturowe, należy ocenić wpływ właściwości zwilżających na wydajność PiP.
Rozważania dotyczące reflow
Profil rozpływu pasty lutowniczej może być manipulowany, aby wpłynąć na wynik jakości połączenia lutowanego dla całego zespołu PCB, a nie tylko komponentu PiP. Istnieje szereg czynników, które należy wziąć pod uwagę podczas dostosowywania profilu, aby osiągnąć najlepszy możliwy wynik. Najczęstsze czynniki ograniczające podczas opracowywania profilu rozpływowego obejmują zalecenia dotyczące pasty lutowniczej, ograniczenia temperatury komponentów, charakterystykę masy termicznej zespołu, możliwości i ograniczenia pieca. Zastosowany profil musi uwzględniać te ograniczenia, jednocześnie spełniając cele jakościowe aplikacji.
Ocena jakości
Jakość połączeń lutowanych PiP powinna spełniać kryteria IPC-610 dla klas 1, 2 i 3. Nieniszczące badania rentgenowskie i niszczące przekroje poprzeczne mogą dostarczyć ostatecznych dowodów na to, czy proces zakończył się sukcesem.
Procesy niższego szczebla
Włączenie procesu PiP może mieć nieoczekiwane konsekwencje dla szeregu procesów po lutowaniu rozpływowym. Ponieważ pasta lutownicza ma objętość topnika 50%, dodanie dodatkowej pasty do PCB w celu wypełnienia beczki może znacznie zwiększyć ilość pozostałości topnika po lutowaniu. Należy pamiętać, że płynny topnik stosowany w lutowaniu na fali i lutowaniu selektywnym pozostawia bardzo mało pozostałości. Zwiększona ilość pozostałości pasty lutowniczej może powodować szereg problemów:
- Estetyka - Mówiąc najprościej, zwiększone pozostałości topnika nie są atrakcyjne wizualnie.
- ICT - Zwiększona ilość pozostałości topnika może zakłócać kontakt sond testowych z obszarem testowym, prowadząc do "fałszywych wywołań". Może być wymagana zwiększona konserwacja oprzyrządowania testowego, wymiana sond i czyszczenie.
- Piec rozpływowy - Zwiększona ilość pasty prowadzi do zwiększenia ilości lotnych związków topnika generowanych podczas procesu rozpływowego. Skutkuje to gromadzeniem się pozostałości topnika w piecu, co powoduje zwiększone czyszczenie systemu zarządzania topnikiem i kapanie topnika w piecu rozpływowym. Dodatkowo, pasta wyparta z cylindra podczas procesu wkładania może spaść z końcówki trzpienia i gromadzić się na dnie pieca rozpływowego.
- Pozostałości topnika i/lub pasty lutowniczej mogą wypłynąć na koniec złącza, co może naruszać standardy jakości lub kolidować z ograniczeniami luzu i tolerancji.
Wnioski
Komponenty z otworami przelotowymi są nadal powszechne i jest mało prawdopodobne, że zostaną wyeliminowane w dającej się przewidzieć przyszłości. Współcześni monterzy nieustannie wdrażają nowe procesy i optymalizują istniejące. Udowodniono, że PiP może pomóc obniżyć koszty operacyjne, uprościć proces produkcji, zmniejszyć ślad linii montażowej i oszczędzać energię. Wraz z wprowadzaniem nowych stopów, mniejszych urządzeń i nowych technologii, PiP pozostaje przydatną techniką w branży montażu PCB.