ABSTRAKT
Ponieważ przemysł elektroniczny nieustannie dąży do innowacji i wydajności w procesach montażu i przeróbek, eksploracja niskotemperaturowych (LT) stopów lutowniczych zyskała znaczną uwagę. Niniejszy artykuł zawiera kompleksową analizę lutów LT, w szczególności koncentrując się na ich zastosowaniu w procesach przeróbek i szerszych implikacjach dla produkcji elektroniki. Zagłębiamy się w różne aspekty lutów LT, badając zarówno potencjalne korzyści, jak i wyzwania związane z ich zastosowaniem.
W badaniu dokonano przeglądu wcześniejszych prac nad lutem LT w przeróbkach, oferując szczegółowe podsumowanie i sugerując ostrożne podejście ze względu na zwiększone koszty i złożoność związaną z drutem lutowniczym zawierającym bizmut, a także brak znaczących różnic w wytrzymałości i niezawodności połączeń w porównaniu z tradycyjnymi metodami. Dodatkowo, artykuł odnosi się do szerszych rozważań na temat lutu LT, w tym korzyści i wad, kompromisów w zakresie wydajności oraz obszarów wymagających dalszych badań.
Badania nad lutem LT zostały dodatkowo wzbogacone o nowe dane dotyczące czyszczenia pozostałości tlenku bizmutu oraz wpływu temperatury grota i czasu kontaktu na tworzenie IMC podczas przeróbki. Zapewniając dokładny przegląd istniejących badań i nowych ustaleń, niniejszy artykuł ma na celu zaoferowanie cennych spostrzeżeń producentom, inżynierom i badaczom, przyczyniając się do świadomych decyzji dotyczących przyjęcia i integracji lutu LT w przeróbce i montażu elektroniki.
WPROWADZENIE
W erze, w której innowacyjność i wydajność stały się najważniejsze, branża produkcji elektroniki nieustannie poszukuje sposobów na usprawnienie procesów, obniżenie kosztów i zwiększenie niezawodności produktów. Wśród różnych badanych rozwiązań, lutowanie niskotemperaturowe (LT) pojawiło się jako obiecująca alternatywa dla tradycyjnych metod lutowania, zwłaszcza przy rozprzestrzenianiu się skomplikowanej, zminiaturyzowanej elektroniki.
Historycznie, stosowanie lutów LT było motywowane ich unikalnymi właściwościami, takimi jak obniżona temperatura topnienia oraz potencjał oszczędności energii i materiałów.[1]
Jednak, podobnie jak w przypadku każdej znaczącej zmiany w metodologii, wdrożenie lutowania LT przyniosło szereg wyzwań. Wyzwania te, od niezawodności, przez obawy związane z przeróbkami, po zarządzanie pozostałościami, wymagają głębszego zbadania i zrozumienia.
Niniejszy artykuł zagłębia się w zawiłości lutowania LT, szczególnie w dziedzinie przeróbek i montażu elektroniki. Poprzez rygorystyczne badanie oraz połączenie danych eksperymentalnych i spostrzeżeń branżowych, staramy się rzucić światło na prawdziwy potencjał, korzyści i rozważania dotyczące stosowania lutu LT we współczesnej produkcji elektroniki.
TŁO
Informacje o kluczowych cechach i kwestiach związanych z lutowaniem LT są często rozbieżne, a zarówno trwające, jak i istniejące badania są pogrążone w różnicach metodologicznych, uwikłaniu w działania marketingowe i braku metaanalitycznych wniosków wystarczająco solidnych, aby zapewnić producentom bezpośrednie i praktyczne spostrzeżenia. Niniejszy dokument ma na celu rozpoczęcie procesu łączenia istniejących informacji w spójny obraz, identyfikując zarówno korzyści, jak i wyzwania związane z lutowaniem LT w różnych wymiarach, jednocześnie jasno określając pozostałe pytania i obszary badań, a także ujednolicone wnioski z istniejących prac.
Stopy niskotemperaturowe
Luty LT charakteryzują się unikalnym składem metali, obejmującym głównie cynę (Sn) i bizmut (Bi). W przeszłości obecność ołowiu (Pb) w stopach lutowniczych była powszechna, ale wraz z przejściem na procesy bezołowiowe, bizmut stał się bardziej opłacalnym składnikiem.[2] Znaczenie cyny i bizmutu w tych stopach oznacza znaczącą zmianę w technologii lutowania. Bizmut, wcześniej pomijany ze względu na jego niekompatybilność z procesami opartymi na Pb, jest obecnie integralną częścią lutów LT, zwłaszcza że większość procesów lutowania przeszła na wolne od Pb. To przejście pobudziło rozwój nowych generacji lutów LT. Podczas gdy pojawia się coraz więcej różnych kompozycji lutowniczych LT, niniejszy artykuł skupi się przede wszystkim na eutektycznej cynie-bizmucie i cynie-bizmucie z niewielkim dodatkiem srebra (Ag), ponieważ te kompozycje stanowią znaczną część obecnych zastosowań lutowniczych LT.
Podstawowe zalety i wady lutowania LT
Podstawową zaletą lutów LT jest niższa temperatura topnienia w porównaniu do tradycyjnych lutów. Ta cecha prowadzi do kilku korzyści. Pierwszą z nich jest mniejsze zużycie energii. Niższa temperatura topnienia pozwala na oszczędność energii podczas procesu lutowania, ponieważ wymagana jest mniejsza ilość ciepła. W rzeczywistości niektóre badania wykazały potencjalne oszczędności energii do 20-40% przy użyciu niskotemperaturowych profili rozpływowych w porównaniu do tradycyjnych SAC305.[3]
Kolejną zaletą jest zmniejszone wypaczanie komponentów. Niższe temperatury zmniejszają ryzyko wypaczenia wrażliwych komponentów podczas lutowania, zwiększając tym samym integralność produktu.
Korzyści te są jednak równoważone przez pewne wady. W szczególności bizmut, choć korzystny ze względu na obniżenie temperatury topnienia, wprowadza kruchość do połączeń lutowanych. Może to wpływać na niezawodność i trwałość połączeń lutowanych, zwłaszcza w środowiskach, w których występują naprężenia mechaniczne.
Kolejna wada związana jest z wrażliwością na temperaturę. Podczas gdy niższe temperatury są korzystne dla oszczędności energii i zmniejszenia wypaczenia, wymagają one również starannej kontroli i kalibracji podczas procesu lutowania, aby zapewnić integralność połączenia.
Pojawiają się również pytania związane z tworzeniem połączeń hybrydowych (często SAC+LT) w różnych scenariuszach oraz charakterystyką i trybami awarii takich połączeń.[4] Jest to coś, co wcześniej badaliśmy w przypadku przeróbek przy użyciu lutu niskotemperaturowego. Zmiany w procesie to kolejny obszar badań, taki jak dostosowywanie szybkości ramp i używanie pieców rozpływowych ze strefami chłodzenia. [5][6]
Lutowanie w niskiej temperaturze
Jednym z pytań zadawanych przez wielu producentów podczas wdrażania procesów lutowania w niskich temperaturach jest to, czy mogą lub powinni oni również używać lutu niskotemperaturowego do wszelkich przeróbek wykonywanych na komponentach, które zostały przylutowane lutem LT. Pytanie to jest dwojakie - po pierwsze, czy lut LT w procesie wymaga lutu LT w przeróbce, aby zachować integralność połączenia, a po drugie, czy użycie lutu LT w przeróbce przynosi dodatkowe korzyści i oszczędności, podobnie jak w przypadku lutu LT stosowanego w lutowaniu rozpływowym i na fali.
Dyskusja ma na celu zapewnienie kompleksowego zrozumienia roli lutu LT w przeróbkach, podkreślając kluczowe kwestie dla producentów rozważających jego przyjęcie w swoich protokołach napraw i konserwacji.
Podsumowanie poprzedniego badania
Pierwotne badanie dotyczyło możliwości zastosowania stopów LT w scenariuszach przeróbek.[7] Zaobserwowano, że do obróbki stopów LT można z powodzeniem stosować drut stały o niskiej temperaturze topnienia i topnik zewnętrzny, a także drut lutowniczy SAC305 z rdzeniem topnikowym. Luty LT wykazywały różne charakterystyki przetwarzania w porównaniu do lutów SAC, ale nie utrudniały one tworzenia wysokiej jakości połączeń lutowanych.
Co najważniejsze, połączenia lutowane wykonane lutem LT spełniały kryteria IPC klasy 1, 2, 3, co sugeruje, że lut LT jest realną opcją dla szeregu klas produktów. Wyniki testów ścinania były jednak zmienne, odzwierciedlając nieodłączne wyzwania związane z procesami przeróbek. Połączenia lutowane SAC wykazały większą plastyczność w porównaniu do ich odpowiedników z bizmutem, co jest zgodne ze znanymi właściwościami materiałowymi tych stopów. Gdy użyto drutu lutowniczego z rdzeniem topnikowym SAC305, proces przypominał tradycyjne metody przeróbki SAC/SAC, z naciskiem na wykorzystanie drobniejszych średnic drutu dla mniejszych komponentów.
Badanie podkreśliło znaczenie umiejętności operatora, podkreślając potrzebę odpowiedniego szkolenia przy wdrażaniu przeróbek LT. Jest to szczególnie istotne, biorąc pod uwagę zmienny charakter wyników przeróbek, nawet pod okiem bardzo doświadczonego operatora.
Nierozwiązane pytania z badania wstępnego
Kilka kwestii pozostało nierozstrzygniętych, co wymaga dalszych badań. Jedną z kluczowych nierozwiązanych kwestii jest możliwość oczyszczenia pozostałości tlenku bizmutu po przepływie i ponownej obróbce. Aspekt ten ma kluczowe znaczenie dla zapewnienia długoterminowej niezawodności i wydajności połączeń lutowanych.
Oryginalne badanie wykazało również, że zmienne w technikach lutowania ręcznego, w szczególności temperatura grota i czas kontaktu, znacząco wpływają na tworzenie się związków międzymetalicznych (IMC). Zrozumienie tych zmiennych jest niezbędne do optymalizacji procesów przeróbek i zapewnienia integralności połączeń lutowanych.
Te nierozstrzygnięte kwestie zostały zbadane w sposób opisany w kolejnych dwóch sekcjach.
Czystość pozostałości tlenku bizmutu
Jedną z głównych obaw związanych ze stosowaniem lutów LT jest możliwość pozostania pozostałości tlenku bizmutu po procesach ponownego rozpływu i przeróbki. Obecność tego osadu może wpływać na jakość i niezawodność połączenia lutowanego, choć jest on uważany głównie za element kosmetyczny. We współpracy z MicroCare przeprowadzono badanie w celu ustalenia, czy pozostałości te można usunąć i który środek czyszczący jest najlepszy.
Cel eksperymentu
Badanie miało na celu ocenę skuteczności różnych chemikaliów czyszczących w usuwaniu pozostałości z połączeń lutowniczych utworzonych przy użyciu lutowia niskotemperaturowego (LT). Badanie to koncentrowało się w szczególności na ocenie zdolności różnych środków czyszczących do czyszczenia pozostałości tlenku bizmutu powstałych w wyniku procesów lutowania LT.
Użyte materiały
W tym badaniu zastosowano różne materiały lutownicze. Wybór obejmował pastę AIM M8 SAC305, pastę NC273LT Sn42/Bi57/Ag1, drut z rdzeniem topnikowym SAC305 oraz lity Sn42/Bi57/Ag1 w połączeniu z topnikiem NC280 (dla komponentów PTH) lub NC217 (dla komponentów SMT).
Aby ocenić proces czyszczenia, wzięto pod uwagę trzy różne chemikalia czyszczące. Dwa z nich były fluorowanymi środkami czyszczącymi, oznaczonymi jako środki czyszczące X i Y, podczas gdy trzeci był niefluorowanym środkiem czyszczącym o nazwie środek czyszczący Z.
Układ eksperymentalny i procedura
Na etapie montażu i testowania dla każdego badanego środka czyszczącego utworzono kupony testowe (PCB016). Proces montażu obejmował wiele etapów. Kupony A i B zostały ponownie zalane lutem LT i przerobione przy użyciu drutu LT i zewnętrznego topnika. Kupon C został poddany lutowaniu rozpływowemu lutem LT i przeróbce przy użyciu drutu SAC305 z rdzeniem topnikowym. Kupon D został poddany zarówno lutowaniu rozpływowemu, jak i przeróbce przy użyciu drutu SAC305. Wreszcie, kupon E został ponownie zalany lutem LT i nie został poddany żadnej przeróbce. Początkowy krok w tej fazie obejmował wykonanie zdjęć "przed" wszystkich komponentów.
Kolejna procedura czyszczenia stanowiskowego obejmowała zastosowanie rozpuszczalnika czyszczącego za pomocą narzędzia dozującego. Proces obejmował cykl szorowania na mokro i na sucho, składający się z 20-sekundowego szorowania na mokro, 20-sekundowego szorowania i 30-60-sekundowego okresu suszenia. Czystość kuponów została następnie dokładnie przeanalizowana pod mikroskopem, po czym wykonano zdjęcia "po".
Wyniki
Po dokładnych eksperymentach środek czyszczący X okazał się najskuteczniejszym środkiem czyszczącym dla rozważanych próbek. Skuteczność czyszczenia została dodatkowo oceniona poprzez zbadanie konkretnych kuponów testowych. Kupony testowe B, C i E wykazały najbardziej zadowalające wyniki czyszczenia środkiem czyszczącym X, co oznacza pomyślne usunięcie pozostałości odpowiednio z LT+LT, LT+SAC i LT bez przeróbek (patrz rysunek 1). Jednak kupon testowy A (LT+LT) wykazywał niewielkie pozostałości w niektórych obszarach, w przeciwieństwie do jego bliźniaka, kuponu testowego B. Kupon testowy D (SAC+SAC) wykazywał kilka obszarów zauważalnych pozostałości po czyszczeniu, jak pokazano na rysunkach 2 i 3.
Rysunek 1. Elementy na kuponie testowym C przed (po lewej) i po (po prawej) czyszczeniu środkiem czyszczącym X
Rysunek 2. Kupon testowy A przed (po lewej) i po (po prawej) czyszczeniu środkiem Cleaner X
Rysunek 3. Kupon testowy D przed (po lewej) i po (po prawej) czyszczeniu środkiem czyszczącym X
Wnioski
Badanie wykazało, że choć proces czyszczenia przy użyciu środka czyszczącego X był skuteczny w przypadku większości próbek testowych, występowała znaczna zmienność w usuwaniu pozostałości z różnych próbek. Badanie podkreśla znaczenie wyboru odpowiedniej chemii czyszczącej i rygorystycznego przestrzegania procedury czyszczenia w celu zapewnienia skutecznego usuwania pozostałości.
Rozważania i zmienne dotyczące wzrostu IMC w technikach lutowania ręcznego
Wzrost związków międzymetalicznych (IMC) jest kluczowym czynnikiem w ocenie niezawodności połączenia lutowanego. Wstępne badania wykazały porównywalne wyniki między różnymi kombinacjami lutowania pod względem testów ścinania i grubości IMC. Jednak tempo wzrostu IMC i znaczenie czasu przebywania w tej formacji są nadal przedmiotem intensywnych badań. Odkrycie dynamiki wzrostu IMC w kontekście lutu LT może zapewnić większą jasność co do długoterminowej żywotności lutu.
Wpływ zmienności lutowania ręcznego na IMC i inne cechy
Badanie to zostało zainicjowane w celu odpowiedzi na drugie pytanie wynikające z pierwotnego dokumentu dotyczącego niskotemperaturowej obróbki.[7] Metcal, firma specjalizująca się w produkcji sprzętu do lutowania ręcznego, zbadała wpływ temperatury grotu i czasu kontaktu na tworzenie się związków międzymetalicznych (IMC) i innych cech podczas używania lutu niskotemperaturowego (LTS).
Użyte materiały
W badaniu wykorzystano stop Sn42/Bi57/Ag1 zarówno do lutowania rozpływowego, jak i ponownego, a wraz z drutem zastosowano topnik AIM NC280. Lutowane komponenty składały się z pięciu elementów z platerowanymi otworami przelotowymi (PTH), w tym trzech rezystorów i dwóch kondensatorów, na jednym modelu płytki drukowanej. Lutowanie ręczne wykonano za pomocą lutownicy CVC-6CH0025S z grotem o średnicy 2,5 mm.
Układ eksperymentalny i procedura
W tym eksperymencie zmieniono warunki lutowania, obejmujące dwie różne temperatury grotu, a mianowicie 285°C i 343°C, z odpowiednimi korektami czasów kontaktu. W szczególności, dla 285°C, czasy kontaktu zostały ustawione na 3s, 4s (linia bazowa), 5s i 6s. Tymczasem w temperaturze 343°C czasy kontaktu wynosiły 2 s (wartość wyjściowa), 3 s, 4 s i 5 s.
Parametry oceny koncentrowały się na kompleksowej analizie różnych aspektów, w tym połączeń lutowanych, charakterystyki pozostałości, właściwości zwilżających, korozji, kształtu połączenia lutowanego, potwierdzenia wypełnienia beczki, grubości IMC i obecności pustek.
Wyniki
Podczas badania połączeń lutowanych zaobserwowano, że niektóre połączenia wykazywały kąt styku przekraczający 90 ° w temperaturze 285 ° C, co było szczególnie widoczne przy 3-sekundowym czasie kontaktu. I odwrotnie, w temperaturze 343°C niektóre połączenia wykazywały nadmiar lutu na górnej stronie, jak pokazano na rysunku 4.
Rysunek 4. Kąt zwilżania styku kondensatora po przeróbce w temperaturze 285°C, czas zwilżania 3 sekundy
Jeśli chodzi o pozostałości, kolor ciemniał w korelacji z czasem kontaktu dla obu temperatur końcówki, jak pokazano na rysunku 5.
Rysunek 5. Spodnia pozostałość przerobionych komponentów w 343°C
Właściwości zwilżające lutu były godne uwagi, prezentując błyszczący, gładki wygląd i zapewniając dobre pokrycie powierzchni padów w większości połączeń.
W analizowanych PCB nie wykryto żadnych przypadków korozji.
Warunki temperaturowe miały wpływ na kształt połączeń lutowanych. Komponenty poddane działaniu temperatury 343°C tworzyły lepsze połączenia lutowane przy różnych czasach kontaktu w porównaniu do tych w temperaturze 285°C. Wszystkie beczki, z wyjątkiem rezystora z 3 i 4 sekundami czasu kontaktu w temperaturze 285°C, zostały wypełnione do 100%.
Badanie grubości IMC wykazało, że w temperaturze 343°C IMC PCB/lut było wyższe w porównaniu do IMC Pin/lut. Grubość IMC była większa dla komponentów z 3 i 4 sekundami czasu kontaktu niż dla tych z 2 i 5 sekundami. W temperaturze 285°C, IMC pinów/lutów była wyższa niż IMC PCB/lutów, szczególnie w przypadku rezystorów o czasie kontaktu 6 i 5 sekund. Kondensatory w temperaturze 285°C nie wykazywały mierzalnej IMC pin/lut, co sugeruje, że była ona mniejsza niż 1 µm. Szczegółowe informacje można znaleźć na Rysunku 6, w Tabeli 1 i Tabeli 2.
Rysunek 6. Grubość IMC po ponownej obróbce styku rezystora w temperaturze 343°C, czas kontaktu 4 sekundy
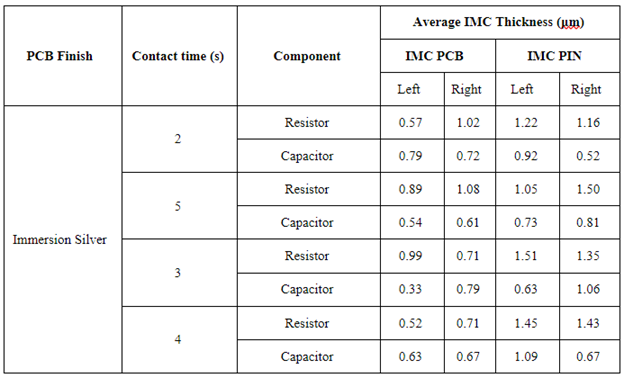
Tabela 1. Średnia grubość IMC 343°C
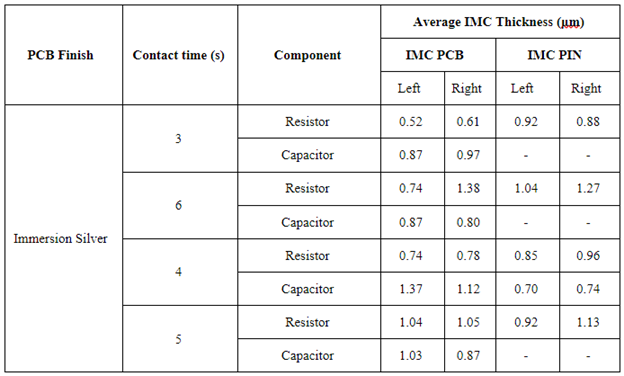
Tabela 2. Średnia grubość IMC 285°C
Wreszcie, obecność pustych przestrzeni była powszechną obserwacją, przy czym ponad 80% szpilek wykazywało puste przestrzenie dla obu temperatur i różnych czasów kontaktu.
Wnioski
Wyniki wskazują, że różne temperatury i różne czasy kontaktu wpływają na jakość połączenia lutowanego i tworzenie IMC. Na pytanie, czy użycie lutu LT w przeróbce może wydłużyć żywotność grotu lub zaoszczędzić energię, odpowiedź wydaje się przecząca. Ogólnie rzecz biorąc, wyższa temperatura, 343°C, przyniosła najlepsze wyniki, a 3-4 sekundy to idealny czas kontaktu.
Dalsze rozważania na temat rozwoju IMC
Różne podejścia do przeróbek, takie jak LT+LT, LT+SAC i SAC+SAC, mogą w unikalny sposób wpływać na powstawanie IMC. Ponieważ producenci rozważają zastosowanie lutu LT do przeróbek, konieczne jest zrozumienie tych subtelnych różnic i ich potencjalnych implikacji. Wiele ostatnich badań dotyczyło wzrostu IMC, a także migracji bizmutu w BGA, porównując efekty LT+LT, LT+SAC i SAC+SAC.[8] Jednak wyniki poszczególnych badań nie wykazują jednoznacznego trendu. Istnieją również dowody na to, że rampa temperaturowa, szybkość chłodzenia i czas przebywania mogą znacząco wpływać na integralność połączenia, jeśli chodzi o lutowie niskotemperaturowe, niezależnie od tego, czy są, czy nie są częścią połączenia hybrydowego, jak wspomniano wcześniej. Wydaje się to wskazywać na możliwość dalszych różnic w wynikach lutowania ręcznego, w zależności od ustawień sprzętu, a także doświadczenia operatora.
Przedstawienie argumentów przemawiających za lutowaniem LT w przeróbkach
Analizując potencjalne korzyści płynące z zastosowania lutów niskotemperaturowych (LT) w procesach przeróbek, należy wziąć pod uwagę kilka kluczowych czynników. Nasze badania dostarczyły wglądu w każdy z tych aspektów, kształtując nasze zrozumienie praktyczności i skuteczności lutu LT w scenariuszach przeróbek.
Oszczędność kosztów materiałów lutowniczych
Wbrew oczekiwaniom dotyczącym opłacalności, drut lutowniczy LT jest znacznie droższy niż SAC305. Wynika to z faktu, że kluczowy składnik lutu LT, bizmut, nie jest bardzo plastyczny, co sprawia, że produkcja drutu lutowniczego LT jest z natury trudniejsza. Ten wyższy koszt podważa jedną z potencjalnych zalet stosowania lutu LT w procesach przeróbek, czyniąc go mniej atrakcyjną opcją z finansowego punktu widzenia.
Łatwość użytkowania
Łatwość użycia to kolejny obszar, w którym lut LT niekoniecznie oferuje korzyści. Wymóg stosowania drutu bezrdzeniowego i zewnętrznego topnika komplikuje proces przeróbki. Dodatkowo wymaga od operatora wyższego poziomu wiedzy i precyzji. Czynniki te przyczyniają się do trudniejszego i bardziej skomplikowanego procesu przeróbki.
Oszczędność energii
Podczas gdy lut LT topi się w niższych temperaturach, co sugeruje potencjalne oszczędności energii, nasze wyniki wskazują, że integralność połączenia i tworzenie IMC jest lepsze, gdy używana jest wyższa temperatura grota i umiarkowany czas kontaktu. Oznaczałoby to, że nie ma możliwości uzyskania oszczędności energii podczas przeróbek bez uszczerbku dla integralności pracy.
Tip Life
Chociaż istnieje teoretyczna możliwość wydłużenia żywotności grotu ze względu na niższe temperatury pracy, nasze badania ponownie sugerują, że nie zostanie to potwierdzone ze względu na lepsze wyniki podczas lutowania w wyższej temperaturze.
Integralność połączenia
Nasze wstępne badanie porównało wydajność konfiguracji SAC+SAC, LT+SAC i LT+LT pod względem testów ścinania i grubości IMC. Wyniki wskazały, że wszystkie te kombinacje były porównywalne pod względem wydajności. Pozostają jednak pytania dotyczące tempa wzrostu IMC i czasu przebywania, które wymagają dalszych badań, aby w pełni zrozumieć wpływ na integralność połączenia.
Wymagania dotyczące temperatury podzespołów/podłoża
Ważną kwestią przy stosowaniu lutu LT jest jego wpływ na komponent i podłoże. Jeśli przyjęcie lutu LT w procesach rozpływowych prowadzi do stosowania tańszych podłoży i komponentów, mogą one mieć określoną wrażliwość na temperaturę podczas przeróbki, którą należy starannie zarządzać. Ten aspekt użycia lutu LT wymaga szczegółowego zrozumienia zastosowanych materiałów i ich odpowiednich tolerancji temperaturowych.
Możliwość czyszczenia pozostałości
Stopy lutownicze zawierające bizmut mogą pozostawiać resztki tlenku bizmutu, zarówno po rozpływie, jak i po przeróbce. W rzeczywistości wiele z tych pozostałości zaobserwowano na przerobionych komponentach w badaniu zmiennej lutownicy. Ustalono jednak, że istnieje roztwór czyszczący i proces, który praktycznie eliminuje te pozostałości.
Wnioski
W oparciu o skumulowane spostrzeżenia z naszych badań i analiz, argumenty przemawiające za stosowaniem lutów LT w procesach przeróbek nie znajdują silnego poparcia. Chociaż istnieją teoretyczne korzyści, praktyczne realia i ustalenia z naszych badań sugerują, że korzyści są albo minimalne, albo negowane przez inne wyzwania. Producenci muszą dokładnie rozważyć te czynniki, rozważając przyjęcie lutu LT do celów przeróbek.
Podstawowe zastosowania lutów niskotemperaturowych
Na koniec chcielibyśmy ponownie ocenić szerszy zakres zastosowań lutów niskotemperaturowych (LT), biorąc pod uwagę zarówno ich nieodłączne ograniczenia, jak i obszary, w których są obiecujące.
Przypomnijmy, że luty LT wykazują niższą niezawodność w scenariuszach związanych z naprężeniami mechanicznymi, takimi jak wstrząsy spowodowane upadkiem, gdzie kruchość może być znaczącą przeszkodą. Mogą one jednak dobrze nadawać się do elektroniki eksploatacyjnej, gdzie wysoka trwałość jest mniej krytyczna, a utrzymanie niskich kosztów produkcji ma zasadnicze znaczenie dla utrzymania rentowności.
Kontrolowane środowiska aplikacji
W przypadkach, w których nie oczekuje się, że urządzenie będzie poddawane znacznym obciążeniom mechanicznym, na przykład w stacjonarnych lub kontrolowanych środowiskach, kruchość lutu cynowo-bizmutowego może nie być głównym problemem.
Połączenie z innymi stopami
Czasami lut cynowo-bizmutowy może być łączony z innymi stopami w celu złagodzenia jego kruchości. Na przykład dodanie srebra (Ag) może poprawić jego wytrzymałość mechaniczną, czyniąc go bardziej odpowiednim do zastosowań wymagających pewnego poziomu odporności na wstrząsy.
Komponenty nadmiarowe lub niekrytyczne
W niektórych projektach, szczególnie w branży motoryzacyjnej i lotniczej, lut cynowo-bizmutowy może być stosowany do komponentów, które są nadmiarowe lub nie są krytyczne dla podstawowej funkcji systemu, zmniejszając w ten sposób ryzyko związane z awarią złącza lutowniczego.
Elastyczna elektronika
W elastycznej elektronice często kładzie się nacisk na elastyczność, a nie na odporność na wstrząsy mechaniczne. W tym przypadku niska temperatura lutu cynowo-bizmutowego jest korzystna dla materiałów wrażliwych na temperaturę stosowanych w tych urządzeniach. Same urządzenia mogą być zaprojektowane tak, aby doświadczać minimalnych uderzeń lub wstrząsów.
Użycie w chronionych komponentach
Zarówno w zastosowaniach motoryzacyjnych, jak i lotniczych, komponenty lutowane cyną-bizmutem mogą być umieszczane w obszarach chronionych mechanicznie, w których prawdopodobieństwo wystąpienia wstrząsów spowodowanych upadkiem jest zminimalizowane.
Aplikacja selektywna
Lut cynowo-bizmutowy może być stosowany selektywnie w połączeniu z innymi rodzajami lutów w jednym zespole, stosowanym tylko w określonych obszarach, w których jego niska temperatura topnienia jest korzystna, a jego kruchość nie jest znaczącą wadą.
Zaawansowane techniki pakowania
Niektóre nowoczesne techniki pakowania elektronicznego mogą złagodzić skutki kruchości lutowia, takie jak stosowanie materiałów wypełniających lub stosowanie specjalnych projektów PCB, które zmniejszają naprężenia na połączeniach lutowanych.
Części nieruchome
W przemyśle motoryzacyjnym i lotniczym może być stosowany do nieporuszających się części lub w zastosowaniach, w których połączenia lutowane nie są poddawane częstym lub silnym naprężeniom mechanicznym.
Spotlight na temat elektroniki użytkowej
Segment elektroniki użytkowej jest szczególnie intrygujący, jeśli chodzi o zastosowanie lutów LT. Są to produkty często projektowane z myślą o krótkim cyklu życia, od akcesoriów mobilnych po niedrogie słuchawki douszne. Należy pamiętać, że podczas gdy urządzenia jednorazowego użytku wykorzystujące lut LT mogą negować pozytywne korzyści dla środowiska wynikające z zastosowania lutu LT, przyczyniając się do nadmiaru odpadów, na określonych rynkach, na których urządzenia elektroniczne muszą być jednorazowe (np. w niektórych zastosowaniach medycznych lub bezpieczeństwa), lut LT może pomóc w utrzymaniu opłacalności.
Przyszłe kierunki i zalecenia
Eksploracja lutowia niskotemperaturowego (LT), jego zastosowanie w przeróbkach i jego szersze implikacje dla przemysłu elektronicznego niewątpliwie przyniosły bogactwo wiedzy. Jednak, jak w przypadku każdego przedsięwzięcia naukowego, podróż ta odkryła tyle samo pytań, na ile odpowiedziała. Opierając się na zebranych do tej pory spostrzeżeniach, wyłania się kilka przyszłych kierunków i zaleceń.
Rozwój i standaryzacja stopów
W badaniu iNEMI respondenci wskazali, że chcieliby, aby istniał standardowy stop w LT, zanim będą chcieli zainwestować w zmianę.[9] Jak wspomniano powyżej, podczas gdy eutektyczna cyna z bizmutem jest "podstawowym" modelem, do którego często porównuje się bardziej wyrafinowane stopy LT lub modyfikuje je w celu rozwiązania istniejących problemów, wciąż trwa wiele eksperymentów z dodawaniem domieszek i innych pierwiastków.
Poprawa niezawodności niskotemperaturowych lutów cynowo-bizmutowych (Sn-Bi) często wiąże się z dodaniem do stopu innych pierwiastków. Dodatki te mają na celu poprawę pewnych właściwości, takich jak wytrzymałość mechaniczna, odporność na cykle termiczne i zmniejszenie kruchości. Niektóre z najbardziej skutecznych pierwiastków do tego celu obejmują:
- Srebro (Ag): Dodawanie srebra do stopów Sn-Bi jest jedną z najpopularniejszych metod poprawy ich wytrzymałości mechanicznej i odporności na zmęczenie cieplne. Srebro może zwiększyć ogólną wytrzymałość połączenia lutowanego, czyniąc je mniej podatnym na uszkodzenia pod wpływem naprężeń mechanicznych lub cykli termicznych.
- Miedź (Cu): Miedź jest kolejnym pierwiastkiem często dodawanym do lutów Sn-Bi. Może ona poprawić charakterystykę zwilżania lutu i poprawić jego właściwości mechaniczne. Miedź pomaga również w zmniejszeniu tempa wzrostu IMC (Intermetallic Compound), co może być korzystne dla długoterminowej niezawodności.
- Nikiel (Ni): Nikiel jest stosowany w celu poprawy właściwości mechanicznych lutu i stabilizacji warstwy międzymetalicznej, zmniejszając wzrost kruchych faz. Może to być szczególnie korzystne w zastosowaniach, w których połączenia lutowane są poddawane naprężeniom mechanicznym.
- Antymon (Sb): Antymon może być dodawany do lutów Sn-Bi w celu poprawy ich właściwości termicznych i mechanicznych. Pomaga on w udoskonaleniu mikrostruktury lutu, prowadząc do lepszej wydajności podczas cykli termicznych i naprężeń.
- Ind (In): Ind może zwiększyć plastyczność lutu, czyniąc go mniej kruchym. Może to być szczególnie przydatne w zastosowaniach, w których ważna jest elastyczność i odporność na zmęczenie cieplne.
Każdy z tych elementów w różny sposób przyczynia się do ogólnej wydajności lutu. Wybór elementu (elementów) do dodania zależy od konkretnych wymagań aplikacji, takich jak środowisko pracy, rodzaje naprężeń, które napotkają połączenia lutowane, oraz pożądana równowaga między kosztami a wydajnością. Proporcje tych dodatków muszą być dokładnie kontrolowane, ponieważ nadmierne ilości mogą prowadzić do innych problemów, takich jak zwiększona kruchość lub zmniejszona zdolność zwilżania.
Określanie uzasadnienia biznesowego dla lutowania niskotemperaturowego dziś i w przyszłości
Określenie uzasadnienia biznesowego dla lutów niskotemperaturowych (LT) obejmuje ocenę zarówno natychmiastowych, jak i długoterminowych czynników w produkcji elektroniki. Kluczowe kwestie obejmują porównanie kosztów lutów LT i tradycyjnych, uwzględnienie potencjalnych długoterminowych oszczędności wynikających ze zmniejszonego zużycia energii i możliwości stosowania tańszych komponentów. Kompatybilność lutu LT z istniejącymi liniami produkcyjnymi, wraz z wymaganiami dotyczącymi modyfikacji sprzętu, stanowi krytyczną część tej oceny.
Należy wziąć pod uwagę wymagania specyficzne dla produktu, szczególnie w przypadku komponentów wrażliwych na temperaturę, a także niezawodność i wydajność lutów LT w różnych warunkach. Ponadto istotną rolę w tej ocenie odgrywają korzyści środowiskowe i zgodność z przepisami, dostosowane do globalnych trendów zrównoważonego rozwoju.
Ważne są również perspektywy na przyszłość, takie jak trend w kierunku miniaturyzacji urządzeń elektronicznych i zmiany rynkowe w kierunku bardziej przyjaznych dla środowiska procesów produkcyjnych. Biznesowe uzasadnienie dla lutów LT zależy zatem od równowagi między natychmiastowymi potrzebami operacyjnymi, długoterminowymi korzyściami i dostosowaniem do zmieniających się trendów branżowych i wymagań konsumentów.
Znaczenie współpracy branżowej
Droga naprzód wymaga wspólnych wysiłków w zakresie wspólnych badań, łączących wiedzę specjalistyczną ze środowisk akademickich, produkcji i technologii lutowania w celu zbadania takich obszarów, jak zużycie energii, interakcje materiałowe i inne. Ustanowienie otwartych platform wymiany wiedzy, w połączeniu ze wzmocnionymi więzami między przemysłem a środowiskiem akademickim, będzie miało kluczowe znaczenie dla rozwiązania nierozwiązanych kwestii i wspierania innowacji. Takie wspólne podejście obiecuje uwolnić pełny potencjał lutowania LT w produkcji elektroniki, przekształcając wyzwania w kamienie milowe dla postępu i wydajności w tej rozwijającej się dziedzinie.
WNIOSKI
Nasze kompleksowe badanie lutowia niskotemperaturowego (LT) w montażu elektroniki i przeróbkach podkreśliło jego złożoną rolę w nowoczesnej produkcji. Analiza porównawcza różnych strategii przeróbek ujawniła zniuansowane różnice pod względem jakości połączeń, wzrostu IMC i czasu procesu, rzucając światło na najlepsze praktyki dostosowane do konkretnych celów produkcyjnych. Podsumowując, lepsze przerobione połączenia powstały przy użyciu wyższych temperatur końcówki żelazka i umiarkowanych czasów kontaktu. Ponadto byliśmy w stanie potwierdzić, że pozostałości tlenku bizmutu powstałe w wyniku przeróbki lub ponownego rozpływu lutów zawierających bizmut w niskiej temperaturze można oczyścić, jeśli stanowią one problem.
Ostatecznie doszliśmy do wniosku, że podczas gdy lut LT ma wiele zalet w lutowaniu rozpływowym, nie ma zbyt wielu argumentów przemawiających za użyciem lutu LT do przeróbek ze względu na złożoność, koszty i względny brak jakichkolwiek korzyści w porównaniu z przeróbkami przy użyciu SAC. Co więcej, dopóki dalsze odkrycia nie przyniosą bardziej niezawodnych stopów LT, widzimy wady związane z kruchością i awariami spowodowanymi wstrząsami, które należy zrównoważyć z oszczędnością energii i kosztów lutowania LT, wskazując, że elektronika eksploatacyjna jest prawdopodobnie najlepszym obecnie przypadkiem użycia.
Patrząc w przyszłość, rozwój i szersze zastosowanie lutów LT będzie zależało od sprostania wyzwaniom poprzez wspólne innowacje, ciągłe badania i dostosowanie do nowych wymagań branżowych. Podróż przez zawiłości lutu LT sugeruje ścieżkę ciągłego uczenia się i adaptacji, gdzie współpraca branżowa może wykorzystać jego potencjał, aby sprostać rosnącym wymaganiom produkcji elektroniki.
ODNIESIENIA
[1] Tang, K. K., Aspandiar, R. F., Mokler, S., Chen, O., & Jiang, A. (2015). SMT Soldering with Low Temperature Solder Paste. Intel Corporation.
[2] Mei, Zequn & Hua, Fay & Glazer, J. & Chung, C. Key. (1997). Lutowanie w niskiej temperaturze. Circuit World. 10. 463 - 476. 10.1109/IEMT.1997.626966.
[3] Intel. (2017). Wprowadzenie do lutowania niskotemperaturowego (LTS). Intel Corporation. Copyright 2017.
[4] Coyle, R., Anselm, M., Hadian, F., Kempaiah, S., Raj, A., Popowich, R., Clark, L., Fullerton, J., & Johnson, C. (2021, 1 listopada). The Effect of Peak Reflow Temperature on Thermal Cycling Performance and Failure Mode of Hybrid Low Temperature Solder Joints. SMTA International 2021, 1 listopada 2021 r.
[5] Dušek, K. & Bušek, David & Veselý, Petr & Pražanová, Anna & Plaček, Martin & Re, Julia. (2022). Zrozumienie wpływu profilu rozpływu na właściwości metalurgiczne lutów cynowo-bizmutowych. Metals. 12. 121. 10.3390/met12010121.
[6] Sloan, M., Flanagan, K., Sandy-Smith, B., Allen, M. B. (2018). Reflow Profiling for Next-Generation Solder Alloys. Indium Corporation. Clinton, NY, USA.
[7] O'Neill, T., Fijalkowski, J., Tafoya, C., Xu, Y., Hrcek, S., Lambert, L., Willis, B., Hamasha, S. (Year). Rozwiązywanie problemów związanych z obróbką w niskich temperaturach. AIM Solder. Montreal, Quebec, Kanada.
[8] Fu, Haley & Aspandiar, Raiyomand & Chen, Jimmy & Cheng, Shunfeng & Chen, Qin & Coyle, Richard & Feng, Sophia & Hardin, Bill & Krmpotich, Mark & Mokler, Scott & Radhakrishnan, Jagadeesh & Ribas, Morgana & Sandy-Smith, Brook & Tang, Kok & Wu, Greg & Zhang, Anny & Zhen, Wilson. (2018). Projekt iNEMI dotyczący rozwoju procesu niskotemperaturowych past lutowniczych na bazie BISN - Część II: Charakterystyka połączeń lutowniczych BGA ze stopów mieszanych. 1-17. 10.23919/PanPacific.2018.8318989.
[9] iNEMI. (2019). iNEMI Survey Summary Report: Gotowość do lutowania niskotemperaturowego (LTS) do montażu płytek drukowanych. Opublikowano w maju 2019 r.
ZATWIERDZONY PRZEZ
Timothy O'Neill, Gayle Towell
AIM Solder
Cranston, Rhode Island, USA
Elizabeth Norwood
MicroCare
New Britain, Connecticut, USA
Hoa Nguyen
Metcal
Cypress, Kalifornia, USA
*PRESENTED AT IPC APEX 2024
PODZIĘKOWANIA
Autorzy chcieliby podziękować Yanci Gomez, AIM Solder R&D Technical i Itzayana Lopez, AIM Solder R&D Chemist za pomoc w analizie przekrojowej.