PORADY DOTYCZĄCE APLIKACJI CELOWYCH
Zoptymalizowany i zatwierdzony przez inżyniera
Zalecenia dotyczące ustawień drukowania pasty lutowniczej
Ustawienia drukowania mają kluczowe znaczenie dla optymalnego nakładania pasty lutowniczej. Niniejszy przewodnik zapewnia wgląd w kluczowe parametry, takie jak oderwanie, odległość separacji, separacja, prędkość, prędkość drukowania i nacisk rakli. Zrozumienie i dostosowanie tych ustawień może poprawić jakość i niezawodność osadzania pasty lutowniczej.
Zalecane ustawienia Snap-Off: 0.00 (w kontakcie)
Co to jest Snap-Off?
Snap-off odnosi się do odstępu między podłożem (płytką drukowaną) a ekranem lub szablonem. Regulacja odległości oderwania pomaga uwolnić pastę lutowniczą z szablonu i kontrolować ilość pasty osadzonej na podłożu.
Rola funkcji Snap-Off w procesie lutowania
Podczas drukowania rakla wywiera nacisk na szablon i uszczelnia drukowany obszar. Gdy ostrze przechodzi, szablon powraca do ustawionej odległości oderwania, oddzielając się od pasty lutowniczej pozostawionej na podłożu.
Snap-off jest przede wszystkim pozostałością po czasach drukowania za pomocą sit, choć może poprawić uwalnianie pasty przez źle wycięty szablon i może być nadal konieczne w przypadku określonego sprzętu lub aplikacji.
Rozważania dotyczące drukowania Snap-Off
Dodatnie odległości odrywania mogą negatywnie wpływać na pożądany efekt "uszczelnienia", powodując rozprzestrzenianie się pasty i mostki między podkładkami komponentów. Oderwanie może również prowadzić do nierównomiernego osadzania pasty i niespójnych wyników drukowania.
Ustawienie odległości oderwania na 0,00 (drukowanie na styk) zapewnia korzyści, takie jak pełne uszczelnienie, zapobieganie wyciekom i mostkowaniu, nawet w przypadku elementów o drobnej podziałce. Drukowanie na styk zapewnia również bardziej równomierne osadzanie pasty i stałą wysokość pasty.
Jak dostosować ustawienia Snap-Off
Aby ustanowić drukowanie 0,00 snap-off (na styk), wykonaj następujące kroki:
- Wybierz płaskie podłoże.
- Umieść podłoże pod szablonem.
- Opuść szablon lub podnieś płytę do wysokości drukowania.
- Wyłącz podciśnienie utrzymujące płytę.
- Wyreguluj odrzutnik szablonu, aby utworzyć wyraźną szczelinę między szablonem a powierzchnią podłoża.
- Powoli zmniejszaj odległość oderwania, odchylając szablon w kierunku podłoża, aż zetknie się z obszarem drukowania.
- W przypadku drukarek ręcznych zablokuj wysokość szablonu i zresetuj wskaźniki pokrętła do 0,00. W przypadku drukarek automatycznych zapisz nową odległość oderwania i powtórz kroki 2, 3 i 6, aby zweryfikować regulację.
Uwagi
Niektóre urządzenia sterowane komputerowo wymagają dodatkowej kalibracji ustawień odłączania. Zawsze należy zweryfikować ustawienia. Należy również pamiętać o sprawdzeniu całego obszaru płytki pod kątem kontaktu z szablonem, zwłaszcza zewnętrznych krawędzi. Sprawdź podparcie płytki i upewnij się, że płytka nie jest wypaczona, jeśli kontakt nastąpi przedwcześnie.
Zalecana odległość: Od 0,010″ do 0,050″ (od 0,25 do 1,25 mm) w zależności od grubości płyty, ustawień zatrzasku i ogranicznika.
Co to jest odległość separacji?
Odległość separacji odnosi się do odległości, na jaką wieża Z lub wspornik płytki obniża się z kontrolowaną prędkością, aby usunąć szablon przed powrotem do pozycji wyjściowej. Ważne jest, aby ostrożnie oddzielić szablon od płytki drukowanej po wydrukowaniu, aby zapewnić czyste oddzielenie pasty lutowniczej od otworów szablonu. Odległość separacji jest zwykle pokonywana z wybraną prędkością, aby pomóc w tym procesie.
Rola odległości separacji w aplikacji lutowia
Po zakończeniu cyklu drukowania wieża Z przytrzymująca zadrukowane podłoże opuszcza się z określoną prędkością do ustawionej odległości separacji. Po osiągnięciu tej odległości wieża Z opuszcza się z pełną prędkością do pozycji wyjściowej. Wibracje w niektórych podporach płyt, spowodowane powolnymi obrotami silnika, również pomagają w uwalnianiu pasty lutowniczej.
Rozważania dotyczące odległości
Ustawienie odległości separacji sprzyja lepszemu uwalnianiu pasty lutowniczej z otworów szablonu. Przyczynia się również do bardziej jednolitych osadów pasty lutowniczej i minimalizuje szczyt. Chociaż stosowanie odległości separacji spowalnia ogólny czas cyklu drukowania, wpływ na czas produkcji jest minimalny w przypadku małych odległości separacji lub szybszych prędkości separacji, ale staje się bardziej znaczący w miarę zbliżania się do limitów.
Jak dostosować odległość separacji
Rozpocznij od ustawienia odległości separacji w menu ustawień na 0,005" (0,125 mm) więcej niż grubość szablonu. Na przykład, jeśli grubość szablonu wynosi 0,006″ (0,15 mm), ustaw początkową odległość separacji na 0,011″ (0,28 mm). Następnie wykonaj następujące kroki:
- Opuść szablon lub podnieś płytę do wysokości drukowania.
- Upewnij się, że podciśnienie przytrzymujące płytę jest wyłączone.
- Stopniowo dostosuj odległość separacji, zapewniając odpowiedni odstęp między szablonem a podłożem.
- Zweryfikuj odległość separacji, drukując i sprawdzając osadzanie pasty lutowniczej.
Uwagi: Dokładne dostosowanie odległości separacji może być konieczne w zależności od konkretnego sprzętu lub wymagań. Przetestuj i zweryfikuj dostosowaną odległość separacji, aby zapewnić optymalne wyniki.
Podczas dostosowywania odległości separacji należy wziąć pod uwagę wpływ na całkowity czas produkcji. Znajdź równowagę między optymalnym uwalnianiem pasty a wydajnym drukowaniem.
Ważne jest, aby monitorować i utrzymywać odległość separacji, aby uniknąć takich problemów, jak rozmazywanie pasty lutowniczej lub nieodpowiednie uwalnianie. Regularnie sprawdzaj i czyść szablon i sprzęt, aby zapewnić prawidłowe działanie.
Zalecana prędkość separacji: 0,010″ do 0,020″ na sekundę (0,254 mm do 0,508 mm na sekundę), 1-2 lub 10-20% prędkości osi dla elementów o drobnej podziałce i mikro-BGA. W przypadku drukowania niekrytycznego można użyć prędkości od 0,030″ do 0,050″ na sekundę (od 0,762 mm do 1,27 mm na sekundę), 3-5 lub 30-50%.
Czym jest prędkość separacji?
Prędkość separacji odnosi się do zmierzonej prędkości, z jaką rakla oddziela się od szablonu. Podobnie jak w przypadku odległości separacji, parametr ten został zaprojektowany w celu ułatwienia oddzielania pasty lutowniczej od otworów szablonu. Prędkość separacji może być wskazana w tysiącach cali, milimetrach lub jako procent prędkości osi.
Rola prędkości separacji w procesie lutowania
Po zakończeniu cyklu drukowania, kontrolowanie prędkości separacji rakli pomaga w osiągnięciu czystego oddzielenia pasty lutowniczej od otworów szablonu. Dobrze kontrolowana prędkość separacji przyczynia się do spójnego i jednolitego nakładania pasty, minimalizując defekty i zapewniając lepszą jakość połączeń lutowanych. Starannie dostosowując prędkość separacji, można zoptymalizować proces drukowania w celu uzyskania lepszych wyników.
Rozważania dotyczące prędkości separacji
Ustawienie odpowiedniej prędkości separacji ma kluczowe znaczenie dla osiągnięcia optymalnej aplikacji pasty lutowniczej. Pomaga to uniknąć takich problemów, jak "psie uszy", szczytowanie, odprowadzanie wilgoci i nieodpowiednie pokrycie pastą. Podczas gdy wolniejsze prędkości separacji są ogólnie preferowane dla lepszej kontroli, ważne jest, aby znaleźć równowagę między niezawodnym osadzaniem pasty a wydajnym drukowaniem. Przy określaniu odpowiedniej prędkości separacji dla danego zastosowania należy wziąć pod uwagę takie czynniki, jak typy komponentów, projekty płyt i właściwości pasty lutowniczej.
Jak dostosować prędkość separacji
Aby skutecznie dostosować prędkość separacji, wykonaj następujące kroki:
- Dostęp do menu konfiguracji lub ustawień oprogramowania.
- Znajdź parametr prędkości separacji.
- Zacznij od ustawienia konserwatywnej wartości w oparciu o zalecany zakres dla konkretnego zastosowania.
- Wykonaj wydruk testowy i sprawdź osadzanie pasty lutowniczej pod kątem jakości i spójności.
- Stopniowo dostrajaj prędkość separacji, biorąc pod uwagę wydajność i uzyskane wyniki.
- Powtarzaj proces drukowania testowego i inspekcji, aż do uzyskania pożądanej aplikacji pasty lutowniczej.
Uwagi: Precyzyjna regulacja prędkości separacji może być konieczna w zależności od konkretnego sprzętu lub wymagań. Przetestuj i zweryfikuj dostosowaną prędkość separacji, aby zapewnić optymalne wyniki.
Niezbędne jest monitorowanie i utrzymywanie prędkości separacji, aby uniknąć problemów, takich jak rozmazywanie pasty lutowniczej lub nieodpowiednie uwalnianie. Regularnie sprawdzaj i czyść szablon i sprzęt, aby zapewnić prawidłowe działanie.
Podczas drukowania drobnych podziałek, tj. LGA, QFN i micro-BGA, ustaw prędkość separacji na minimum.
Zalecane ustawienia prędkości druku: W zależności od składu i lepkości pasty lutowniczej, maksymalna zalecana prędkość druku wynosi od 1 do 8 cali na sekundę (od 25 do 200 mm na sekundę).
Czym jest szybkość druku?
Prędkość drukowania odnosi się do prędkości, z jaką zespół rakli przesuwa się po szablonie podczas cyklu drukowania.
Rola prędkości druku w aplikacji lutowniczej
Prędkość drukowania należy ustawić w połączeniu z innymi parametrami, takimi jak nacisk rakli, skład chemiczny pasty, rozmiar otworu szablonu i inne. Dostosowanie prędkości drukowania jest konieczne, aby uzyskać czyste czyszczenie powierzchni szablonu, szczególnie w przypadku stosowania pasty lutowniczej o wysokiej lepkości przy wyższych prędkościach.
Rozważania dotyczące prędkości druku
Drukowanie z dużą prędkością zazwyczaj odnosi się do prędkości od 4 do 8 cali na sekundę (od 100 do 200 mm na sekundę). Osiągnięcie dobrej jakości druku przy dużych prędkościach zależy od wyboru odpowiedniej lepkości i reologii pasty lutowniczej, a także odpowiedniego projektu szablonu.
Podczas drukowania z dużą prędkością, siły ścinające rakli powodują tymczasowe zmniejszenie lepkości (rozrzedzenie ścinające) past lutowniczych. Wyższe prędkości i zwiększony nacisk rakli nasilają rozrzedzanie ścinające, potencjalnie prowadząc do zwarć między padami, jeśli pasta nie powróci szybko do swojej normalnej lepkości. Nieodpowiednie wypełnienie otworu szablonu i niewystarczające pokrycie padów może również wystąpić przy dużych prędkościach.
Drukowanie z dużą prędkością wymaga dodatkowych ustawień ciśnienia i prędkości, co może mieć wpływ na przetworniki, serwomotory, rakle i żywotność szablonów. Podstawową zaletą drukowania z dużą prędkością jest skrócenie czasu produkcji i zwiększenie przepustowości.
Jak dostosować prędkość drukowania
Ze względu na liczbę zmiennych, zaleca się, aby skonsultuj się z technikiem AIM Solder w celu uzyskania porady dotyczącej regulacji prędkości druku.
Uwagi: Ogólnie rzecz biorąc, wolniejsze drukowanie zapewnia lepszą jakość druku, ale należy to zrównoważyć z potrzebami produkcyjnymi. Dostosuj prędkość drukowania, aby zoptymalizować czas cyklu bez spowalniania reszty linii produkcyjnej.
Rozważ dostosowanie ustawień drukowania do szybkości cyklu na żądanie, aby zminimalizować czas oczekiwania między cyklami. Taka optymalizacja ułatwia uzyskanie stabilnej reologii pasty lutowniczej i skraca czas cyklu drukowania.
Jeśli w procesie produkcyjnym konieczne są wysokie prędkości drukowania, należy upewnić się, że pasta lutownicza została zaprojektowana tak, aby wytrzymać takie prędkości. Zapewnienie odpowiedniego podparcia płytki może również zminimalizować zginanie podczas cyklu drukowania.
Zalecany nacisk ściągaczki: Od 1 do 1,5 funta na cal liniowy (od 0,45 do 0,70 kg na 25 mm) listwy ssącej
Co to jest ciśnienie ściągaczki?
Nacisk rakli odnosi się do nacisku wywieranego w dół przez listwę rakli na powierzchnię szablonu podczas cyklu drukowania.
Rola nacisku rakli w procesie lutowania
Podczas cyklu drukowania rakla przesuwa pastę lutowniczą po obszarze drukowania, wypełniając otwory i wycierając powierzchnię szablonu do czysta. Odpowiedni nacisk rakli, równomiernie rozłożony na całej długości rakli, zapewnia stałą wysokość pasty, jednolitą kontrolę osadzania oraz mniejsze zużycie rakli i szablonu.
Rozważania dotyczące ciśnienia ściągaczki
Stosowanie odpowiedniej siły nacisku ma zasadnicze znaczenie dla zapewnienia spójnego i niezawodnego osadzania pasty lutowniczej przy jednoczesnym unikaniu potencjalnych problemów. Nadmierny nacisk może prowadzić do uszkodzenia szablonów, koiningu i zerwania taśmy między otworami o drobnej podziałce. Problemy te mogą mieć negatywny wpływ na proces drukowania i skutkować niską jakością połączeń lutowanych. I odwrotnie, użycie zbyt małego nacisku może spowodować przeskoki, jeśli szablon nie zostanie odpowiednio wyczyszczony. Ważne jest, aby znaleźć równowagę między stosowaniem wystarczającego nacisku do wypełnienia szablonu a unikaniem nadmiernej siły, która może spowodować uszkodzenie.
Jak wyregulować nacisk ściągaczki
Aby ustalić prawidłowy nacisk belki ssącej, zakładając, że łopatki są prawidłowo zamontowane i wyregulowane, należy wykonać następujące kroki:
- Wybierz płaskie podłoże.
- Umieść podłoże pod szablonem.
- Wyregulować docisk rakli tak, aby nadmiar lutu pozostał na powierzchni otworu szablonu po zakończeniu cyklu drukowania.
- Nałóż pastę lutowniczą na szablon i wykonaj cykl drukowania.
- Obserwować ilość pasty lutowniczej pozostałej na powierzchni szablonu.
- Nieznacznie zwiększ nacisk rakli i wykonaj kolejny cykl drukowania.
- Ponownie obserwuj ilość pasty lutowniczej pozostałej na powierzchni szablonu, która powinna być nieco mniejsza niż w poprzednim przejściu.
- Powtarzaj kroki 6 i 7, aż na powierzchni szablonu pozostanie widoczna tylko bardzo cienka warstwa pasty lutowniczej.
Uwagi: Dostosowanie innych parametrów drukowania, takich jak prędkość drukowania lub konstrukcja szablonu, może również wpływać na wymagany nacisk rakli.
Regularna kontrola i konserwacja rakli zapewnia optymalną wydajność i stały nacisk.
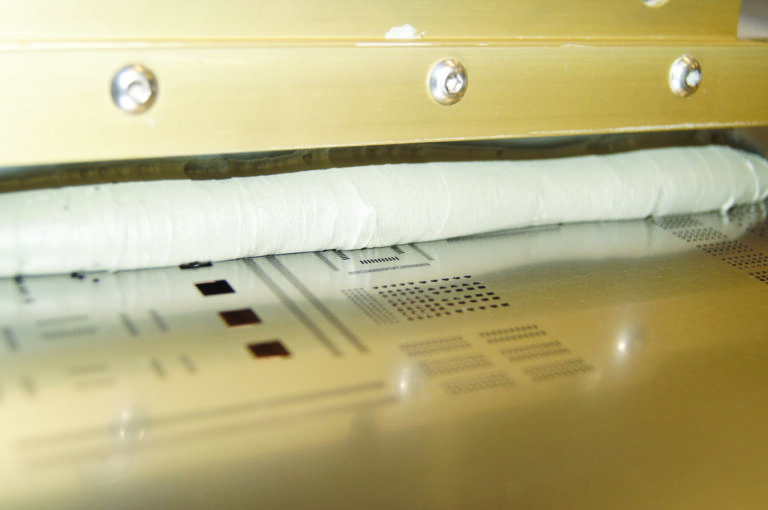