La pâte à braser - la substance grise qui se présente sous forme de pot, de cartouche ou de seringue - est appliquée sur les circuits imprimés pour fixer les composants et créer des connexions électriques. Elle est livrée avec des instructions de stockage et de manipulation. Il doit être réfrigéré. Vous ne pouvez pas le laisser ouvert trop longtemps, sinon il se détériore. Vous devez soigneusement régler les paramètres de votre processus afin d'optimiser ses performances.
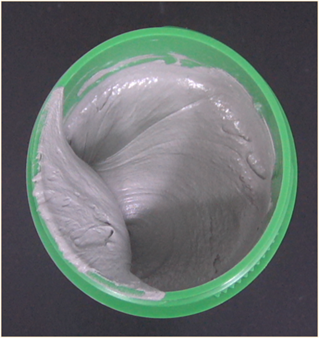
Mais pourquoi ? De quoi est faite cette substance grise ? Comment est-elle fabriquée ?
Notions de base sur la pâte à braser
La pâte à braser est composée de poudre de soudure - de minuscules sphères de métal allié - combinée à un flux - des colophanes, des résines et d'autres produits chimiques conçus pour favoriser le nettoyage et prévenir l'oxydation.
Ainsi, pour fabriquer de la pâte à souder, vous devez d'abord créer un alliage. Il faut ensuite transformer cet alliage en minuscules sphères. Ensuite, vous avez besoin d'un fondant ayant la bonne composition chimique. Enfin, vous combinez les minuscules sphères avec le fondant dans un environnement soigneusement contrôlé.
La méthode exacte utilisée varie d'un fabricant à l'autre, et les détails exacts sont souvent exclusifs et étroitement protégés. Cela dit, nous pouvons tout de même vous donner un aperçu général du processus.
Alliage et atomisation
Les processus de pré-atomisation comprennent l'alliage, le dosage et la coulée du métal qui sera introduit dans l'atomiseur. Une méthode d'atomisation consiste à verser un flux contrôlé de soudure en fusion sur un disque rotatif.
Lorsque le liquide frappe le disque, il est dévié en gouttelettes qui, sous l'effet de la tension superficielle, se transforment en sphères individuelles avant de geler, comme le montre le diagramme ci-dessous. Les paramètres d'atomisation comprennent la température de la matière fondue, la vitesse du disque, l'environnement de la chambre et d'autres variables qui influencent les caractéristiques clés des particules telles que la taille, la forme et le niveau d'oxyde.
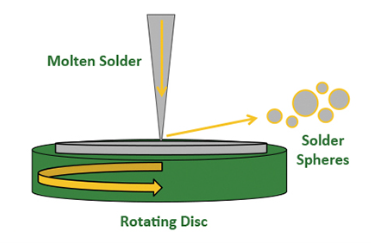
Les opérations d'atomisation sont souvent optimisées pour produire une taille de poudre particulière, les sphères en dehors de la gamme souhaitée étant considérées comme des sous-produits du processus. Les formes sphériques sont idéales, mais il arrive que des formes irrégulières telles que des os de chien ou des queues soient formées, ou que plusieurs sphères s'agglutinent. Ces géométries indésirables peuvent affecter la rhéologie de la pâte à braser et les performances d'impression, et sont éliminées lors du traitement ultérieur.
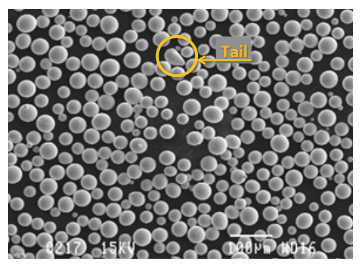
L'oxydation est contrôlée en manipulant les niveaux de gaz inertes dans l'environnement d'atomisation.
Poudre de pâte à braser Tailles/types
Les pâtes à braser sont classées en fonction de la taille de la poudre de soudure (minuscules sphères) qu'elles contiennent. Les tailles de poudre vont du type 1 au type 10, les types 3 à 6 étant les plus couramment utilisés dans la fabrication électronique. Le type 4 est la taille la plus populaire à l'heure actuelle, avec une gamme de tailles de particules de 20 à 38 µm. Il permet d'imprimer des 0201 et des microBGA.
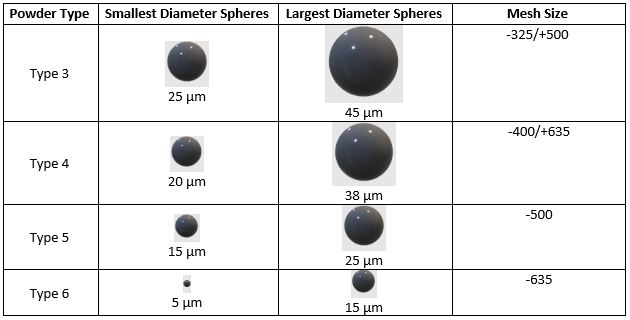
Quelle est cette taille ? À titre de référence, l'épaisseur d'un cheveu humain est d'environ 100 µm et le diamètre d'un globule blanc est d'environ 10 à 20 µm. Ces particules sont donc vraiment très petites !
La poudre de type 5, avec des particules de 15 à 25 µm, est adaptée aux applications plus fines comme les QFN et les dispositifs 01005. Types 6 et inférieurs s'aventurer dans l'ultra-miniaturisation, nécessaire aux technologies de pointe.
Classification et distribution de la taille des poudres
Après l'atomisation, la poudre est raffinée et triée par taille. Les méthodes utilisées à cet effet sont la classification par air et le tamisage.
Le processus de classification par air sépare la poudre de soudure en différentes classes en fonction de la masse. La poudre est soufflée à travers un flux de gaz où les particules de la taille cible sont concentrées. Les particules les plus petites sont entraînées par le flux de gaz et les particules les plus lourdes tombent dans une zone de collecte.
Ce processus permet un vannage rapide de la poudre jusqu'à l'endroit où les particules de la taille la plus souhaitable sont fortement concentrées. La classification par air rend l'opération de tamisage ultérieure beaucoup plus efficace.
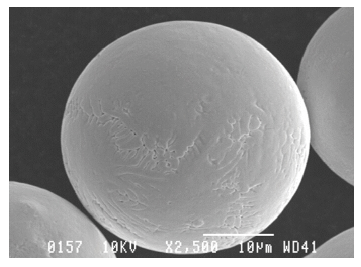
Le tamisage permet de trier la poudre classée à l'aide de grands tamis vibrants dotés de mailles de plus en plus fines. Les tamis correspondent à la taille des mailles qui définit le "type" de poudre tel que désigné par le JEDEC et le J-STD-005. Le tableau de la section précédente présente les classifications, à la fois en termes de taille des mailles des tamis et de taille des particules obtenues.
Les sphères de type 3, ou T3, passent à travers un tamis de 325 mesh mais pas à travers un tamis de 500 mesh, d'où le terme -325/+500. Cela correspond à des particules de 25 à 45 µm ; 80% des particules doivent répondre à cette exigence de taille. De même, la pâte de type 4 passera à travers un tamis de 400 mailles mais pas à travers un tamis de 635 mailles, ce qui équivaut à des particules de 20 à 38 µm.
Il y a un chevauchement de taille entre les classes T3 et T4 ; par conséquent, la pâte à braser T4 peut généralement offrir un léger avantage dans l'impression de caractéristiques fines sans poser de problèmes de refusion.
La taille des particules diminue rapidement entre 5 et 10µm et 25µm, cependant, et bien que la capacité de la pâte à souder à imprimer des caractéristiques fines soit considérablement améliorée, les effets des oxydes de surface peuvent commencer à se faire sentir ; la durée de conservation peut être affectée, et le potentiel de problèmes de coalescence lors de la refusion est accru.
Pâte à braser Flux
Le flux est un agent chimique qui facilite le brasage en nettoyant les surfaces métalliques, en améliorant l'écoulement de la brasure et en empêchant l'oxydation pendant le processus de refusion.
Le flux utilisé dans la pâte à braser est une combinaison de divers produits chimiques, notamment des activateurs, des modificateurs de rhéologie, des solvants et des plastifiants. La composition spécifique du flux dépend de l'application prévue et des propriétés requises, telles que la température d'activation, la viscosité et les exigences en matière de nettoyage.
L'étape finale : Combiner la poudre et le flux
L'étape finale de la fabrication de la pâte à souder consiste à combiner la poudre d'alliage de soudure et le flux dans des proportions spécifiques afin de garantir l'uniformité et l'homogénéité de la pâte. Le rapport typique est d'environ 50/50 entre le flux et l'alliage en volume ou 10/90 en poids, mais il peut varier en fonction des exigences spécifiques de l'application.
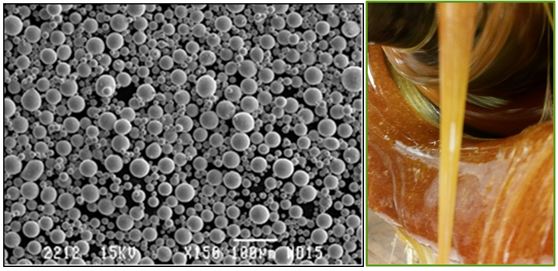
Les fabricants de pâte à braser utilisent des procédés de mélange exclusifs impliquant des mélangeurs soigneusement calibrés pour garantir des températures stables et un mélange homogène. Chaque étape du processus est soigneusement mesurée, contrôlée et maintenue cohérente d'un lot à l'autre, ce qui garantit que la pâte produite est uniforme et répond à toutes les spécifications requises.
Après avoir été mélangée, la pâte est conditionnée dans des pots, des cartouches ou des seringues, en fonction de la manière dont elle sera appliquée sur les circuits imprimés.
Le produit final est ensuite soumis à des tests rigoureux pour s'assurer qu'il répond à toutes les normes en vigueur. Ces tests portent notamment sur la viscosité, l'affaissement, la bille de soudure, le mouillage et la durée de conservation.
Nous avons beaucoup parlé de l'oxydation. De quoi s'agit-il ?
L'oxydation est un processus chimique naturel qui se produit entre les substances et l'oxygène de l'air. L'oxydation est omniprésente : c'est elle qui fait brunir les pommes en tranches lorsqu'elles sont laissées au repos, ou qui provoque la formation de rouille sur une vieille voiture. Elle se produit également lorsque le métal d'un alliage de soudure entre en contact avec l'air.
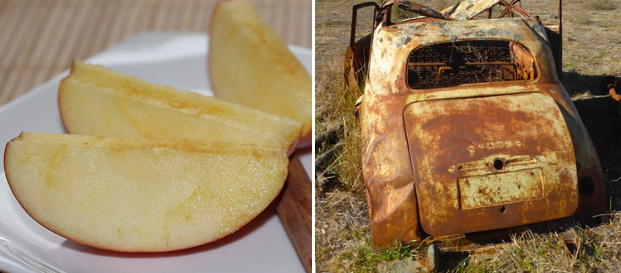
Plus un alliage de soudure est en contact avec l'air, plus il a tendance à s'oxyder. L'oxydation peut également être accélérée par l'humidité, les températures élevées et le chauffage. Lorsque les alliages de soudure réagissent à l'oxygène, ils forment une couche d'oxyde à leur surface. Cette couche d'oxyde est moins conductrice et moins stable mécaniquement que l'alliage pur, ce qui rend difficile la formation de bonnes connexions électriques.
C'est pourquoi l'un des principaux objectifs de la création et de l'utilisation de la pâte à braser est de minimiser l'oxydation autant que possible. En fait, l'un des rôles clés du flux est d'éliminer les oxydes et de prévenir l'oxydation. Il le fait par le biais d'interactions chimiques et en créant une barrière entre le métal et l'air.
Cette propension des métaux à réagir avec l'oxygène explique pourquoi la pâte à souder doit être manipulée et stockée avec précaution. C'est également la raison pour laquelle le processus de fabrication de la pâte doit être soigneusement contrôlé. Souvent, la formation de poudre se produit dans un environnement où l'oxygène a été remplacé par de l'azote, un gaz qui ne réagit pas avec le métal.
La propension à l'oxydation est la raison pour laquelle certains fabricants utilisent des atmosphères d'azote pendant la refusion. C'est également la raison pour laquelle les pâtes à braser plus fines sont plus délicates : lorsque la taille de la poudre est plus petite, le rapport entre la surface et la masse de métal est plus important. Comme l'oxydation se produit à la surface, une plus grande surface signifie plus de risques d'oxydation.
Dernières paroles
Et voilà ! La substance grise est obtenue en créant de minuscules sphères d'alliage métallique et en les combinant avec une pâte chimique optimisée pour atténuer l'oxydation et favoriser des connexions électriques solides. L'oxydation est l'ennemi du processus et du produit final. C'est la raison pour laquelle les instructions de stockage et de manipulation ont été données.