Les alliages de soudure ont évolué en même temps que les besoins de l'industrie, répondant à des exigences de performance spécifiques et établissant de nouvelles références. Cet article se lance dans une exploration chronologique de l'évolution des alliages, en mettant en évidence les développements cruciaux et la trajectoire future de l'innovation en matière d'alliages de soudure.
Historiquement, l'introduction de réglementations telles que la directive RoHS (Restriction of Hazardous Substances) a entraîné l'abandon des brasures à base de plomb. Il a donc fallu mettre au point des matériaux de soudure plus sûrs, mais tout aussi efficaces. La première génération de soudure sans plomb se présentait sous la forme de SAC305L'entreprise est connue pour ses applications robustes dans divers secteurs d'activité. Mais cela n'a pas été sans difficultés.
Première génération d'alliages sans plomb : L'avènement du SAC305
En juillet 2006, la réglementation RoHS a exigé que les alliages de soudure pour de nombreuses applications contiennent moins de 0,1% de plomb. Cela a marqué un changement important dans le développement des alliages puisque la norme, depuis des décennies, était l'alliage eutectique étain-plomb (Sn63Pb37).
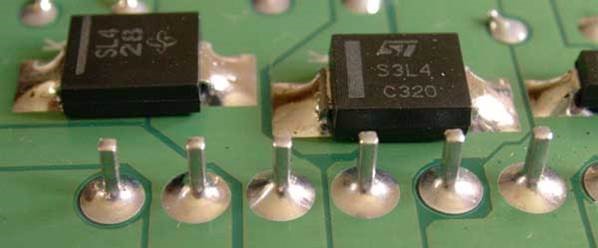
Le Sn63Pb37 est encore utilisé aujourd'hui dans certains secteurs exemptés. Ses avantages sont les suivants
- Un point de fusion bas, qui garantit une contrainte thermique minimale sur les composants lors de l'assemblage.
- Transition rapide de l'état liquide à l'état solide grâce à la nature eutectique, ce qui réduit la probabilité de défauts.
- Excellentes propriétés de mouillage qui assurent une bonne soudabilité sur diverses surfaces
Malheureusement, le risque sanitaire posé a été jugé trop important pour que l'on puisse continuer à l'utiliser dans la plupart des applications.
Jusqu'en juillet 2006, de nombreux nouveaux alliages ont été testés en tant qu'alternatives sans plomb. Le leader émergent à l'époque était le SAC305, un alliage à base d'étain contenant 3% d'argent et 0,5% de cuivre.
L'attrait initial de la SAC305 reposait sur sa compatibilité avec les processus de fabrication existants et les composants en plomb. Cependant, à mesure que son utilisation se répandait, l'industrie a commencé à reconnaître ses défauts inhérents. Des coûts élevés (en raison de la teneur en argent), des problèmes de dissolution du cuivre et des préoccupations concernant les propriétés mécaniques, telles que la résistance aux chocs et aux microfissures, ont été mis en évidence.
En outre, les problèmes de mouillage, la propension à la formation de chuchotements d'étain et le vieillissement imprévisible ont souligné la nécessité de poursuivre l'innovation.
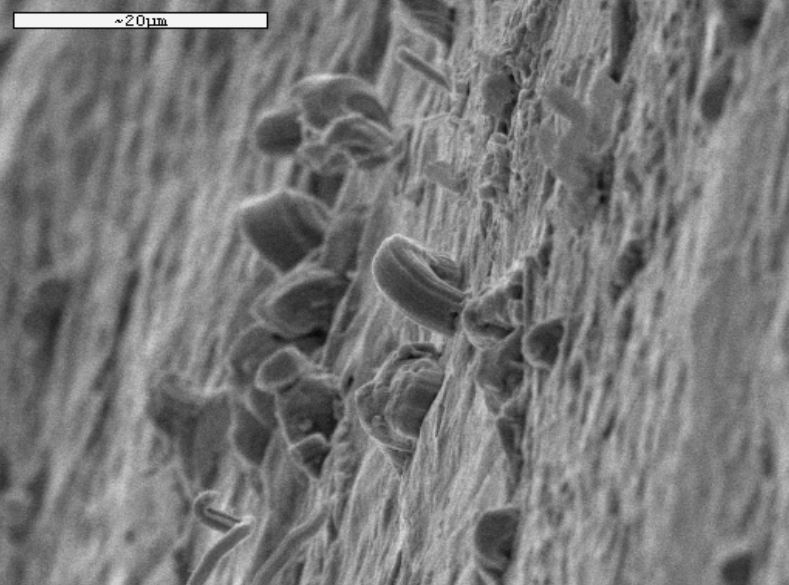
Évolution des alliages de deuxième génération : Variations des SAC
Alors que l'industrie cherchait des solutions aux limites du SAC305, des alliages sans plomb de deuxième génération sont apparus. Parmi ceux-ci, on trouve le SAC105, le SAC0307 et le SN100C.
SACX
La faible teneur en argent du SAC105 et du SAC0307 (respectivement 1% et 0,3% d'argent) en a fait des alternatives rentables au SAC305, dont la teneur en argent est plus élevée.Toutefois, leurs plages de fusion légèrement plus élevées posaient problème. Les fabricants de CMS considéraient déjà que la température de fusion du SAC305 était élevée (217-220 °C), surtout par rapport à celle du SnPb (183 °C).
De nombreux alliages SACX à faible teneur en argent présentent également une résistance mécanique réduite, ce qui les rend moins adaptés aux applications soumises à de fortes contraintes ou à des températures élevées.
SN100C®
Un autre candidat, toujours populaire aujourd'hui, était SN100C®. Développé par Nihon Superior, cet alliage à base d'étain contient 0,7% de cuivre, 0,05% de nickel et des traces de germanium. Connu pour sa grande fluidité, il offre d'excellentes caractéristiques de mouillage, réduisant les défauts et améliorant la résistance des joints.
Mais alors que le SN100C® constituait une solution durable et fiable pour diverses applications, son point de fusion légèrement plus élevé restait un inconvénient.
Si ces alliages de deuxième génération ont trouvé leur place dans de nombreuses applications de brasage à la vague où les problèmes liés aux températures plus élevées ne se posent pas, les applications SMT ont continué à préférer le SAC305, malgré ses défauts.
L'évolution des alliages de troisième génération : Alliages à haute fiabilité
L'avènement des alliages sans plomb de troisième génération a marqué un saut monumental dans la technologie du brasage et a permis une évolution, en particulier pour les industries où la fiabilité est primordiale, telles que l'automobile, l'aérospatiale et les applications militaires. Ces alliages de pointe, développés grâce à des techniques de microalliage, introduisent des éléments mineurs dans le métal de base, améliorant des propriétés spécifiques sans compromettre les caractéristiques fondamentales de l'alliage.
Les chercheurs de l'AIM ont découvert très tôt une combinaison prometteuse d'ajouts de micro-éléments, à savoir le bismuth et l'antimoine. Le bismuth réduit considérablement le point de fusion, minimisant ainsi les contraintes thermiques lors du brasage, et l'antimoine améliore la résistance mécanique.
Chez AIM, notre offre de haute fiabilité de troisième génération comprend des alliages appelés REL61TM et REL22TM. REL22TM contient de l'étain, du bismuth, de l'argent, du cuivre, de l'antimoine, du nickel et des traces de raffineurs de structure de grain élémentaire. Il s'est avéré extrêmement durable dans les environnements difficiles et offre des performances améliorées en matière de mouillage et de cycles thermiques. Il fond également à une température plus basse que le SAC305.
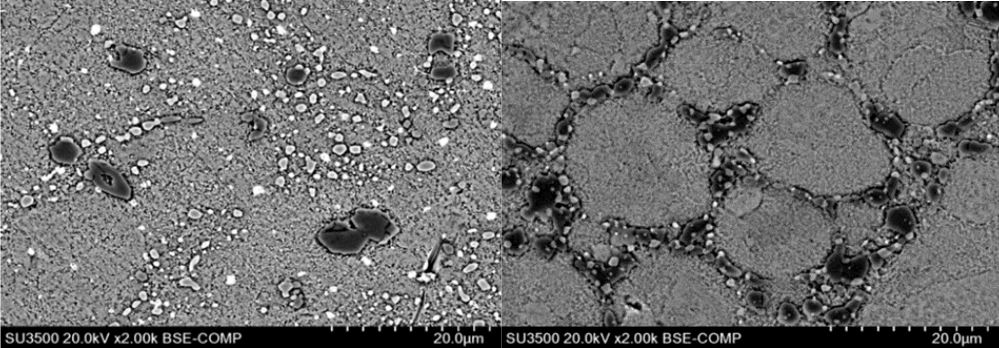
REL61TM est l'alliage le moins cher et le plus fiable d'AIM. Bien que ses performances n'égalent pas celles du REL22TMIl s'est avéré supérieur au SAC305 dans tous les domaines et son prix est également moins élevé.
Les compositions uniques de ces alliages les rendent idéaux pour les applications où l'endurance, la longévité et les performances maximales ne sont pas négociables. Le tableau ci-dessous présente quelques-unes des données de recherche d'AIM comparant les alliages REL22TM et REL61TM au SAC305.
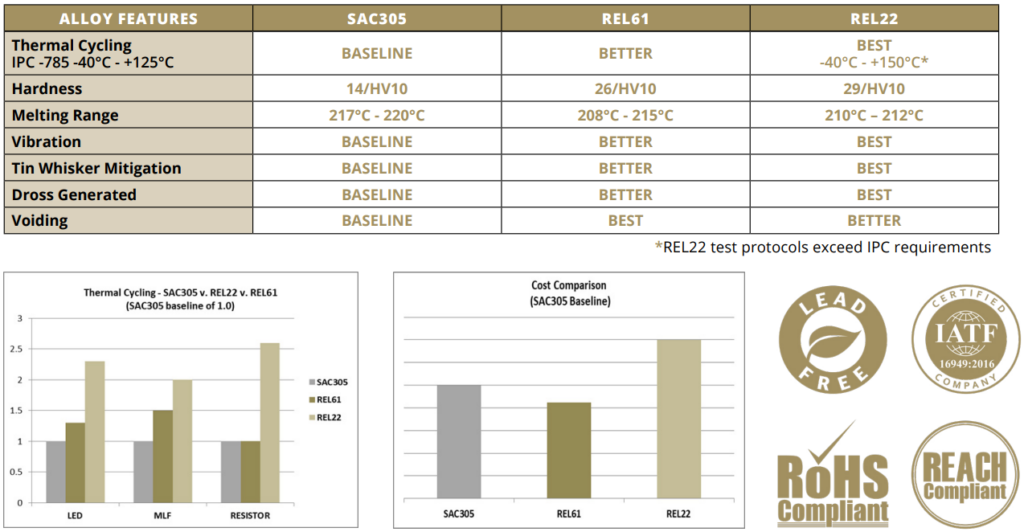
Perspectives d'avenir
Le passage du SAC305 aux alliages avancés sans plomb reflète la capacité d'adaptation et l'engagement de l'industrie électronique en faveur de l'innovation. À chaque génération, des premiers aux derniers alliages à haute fiabilité comme le REL22 d'AIMTM et REL61TMLes matériaux de soudure sont devenus plus sophistiqués, répondant aux exigences croissantes en matière de performance, de fiabilité et de respect de l'environnement.
Un autre domaine de recherche actif est alliages à basse température de fusion - ceux qui sont plus proches du point de fusion de l'étain-plomb. Toutefois, il semble qu'il y ait un compromis dans ce domaine en ce qui concerne la fiabilité. Le Saint-Graal reste une soudure à basse température vraiment très fiable.