por Timothy O'Neill y Logan Jelinske
Resumen
A pesar de las predicciones sobre la desaparición de los componentes con orificios pasantes, siguen siendo habituales en toda la industria. Sin embargo, su uso está disminuyendo y es posible que los ensamblajes sólo incorporen uno o dos componentes con orificios pasantes. Una técnica alternativa para soldar componentes con orificios pasantes, que elimina la necesidad de un proceso de soldadura independiente, es el método Pin-in-Paste (PiP) o de reflujo intrusivo. PiP utiliza la impresión de pasta de soldadura y los procesos de reflujo SMT para soldar dispositivos con orificios pasantes. La técnica PiP puede ser más rentable al eliminar la necesidad de un proceso de soldadura por ola o selectiva y los costes asociados. En este artículo se detalla el proceso PiP, incluyendo consideraciones sobre el diseño de la PCB y el esténcil, así como la selección de la pasta de soldadura y las directrices de reflujo.
Fondo
A medida que los dispositivos electrónicos son cada vez más pequeños y potentes, los componentes con orificios pasantes se utilizan con menos frecuencia, debido a las limitaciones de espacio de los dispositivos modernos. Sin embargo, los dispositivos con orificios pasantes ofrecen ventajas de rendimiento frente a los SMT, ya que disponen de interconexiones robustas con cables conformes que aumentan la fiabilidad mecánica y eléctrica. La soldadura PiP puede proporcionar un proceso y un rendimiento del producto equivalentes a la soldadura por ola, selectiva y manual durante el montaje SMT, reduciendo así los costes. El funcionamiento de una máquina de soldadura por ola o selectiva puede ser costoso y el paso adicional del proceso puede eliminarse. PiP también puede eliminar la necesidad de equipos infrautilizados y aumentar el espacio en la planta de producción.
Consideraciones sobre PiP
Las consideraciones para la implementación de PiP utilizando componentes de orificio pasante son:
- Se verifica que los componentes son capaces de soportar las temperaturas del proceso SMT y se establece el método de inserción. Una vez impresa la pasta de soldadura, los componentes pueden colocarse manualmente o mediante inserción automatizada.
- El componente debe tener una holgura adecuada para evitar que la soldadura entre en contacto con la parte inferior del componente, un defecto según IPC-610G 7.3.5.
- La relación plomo/agujero debe ser lo más ajustada posible. Una relación plomo/agujero demasiado grande provocará un aumento del volumen de pasta, anulaciones y la posibilidad de que la soldadura fluya fuera del agujero pasante durante el reflujo. Una relación plomo/agujero demasiado estrecha provocará un llenado insuficiente del barril y problemas de inserción.
- La longitud del cable debe ser lo más corta posible. Un exceso de longitud desplazará la pasta en la inserción y puede alejar la soldadura del cilindro, aumentando la necesidad de volumen de soldadura.
Los requisitos de volumen de pasta para conseguir un llenado adecuado del barril deben equilibrarse con los requisitos SMT para evitar puentes/cortos, etc. La pasta de soldadura en máscara/sobreimpresión es una técnica aceptada para aumentar el volumen de pasta, pero está limitada por el espaciado de los componentes y otras características de la placa. Además, la diversificación de las opciones de aleación puede afectar o reducir la fuerza de humectación y el retroceso necesarios para que la sobreimpresión sea eficaz.
Las plantillas escalonadas pueden implementarse para conseguir un relleno adecuado del barril sin afectar negativamente a otras juntas de soldadura. Los avances en las técnicas de microsoldadura de esténciles de soldadura han eliminado muchas de las incoherencias asociadas a las tecnologías anteriores. El chorro de pasta de soldadura es un desarrollo reciente que proporciona un medio sin contacto de aumentar el volumen local de pasta. Las preformas de soldadura también pueden utilizarse para aumentar el volumen de soldadura.
Se pueden realizar pequeños ajustes en el proceso para aumentar el llenado del tambor experimentando con los ajustes de la impresora, incluida la impresión sin contacto, manipulando la velocidad de la racleta, la presión, el ángulo de ataque y el número de golpes.
Cálculo del volumen de soldadura
El volumen requerido de la unión soldada, Vsse calcula por la diferencia entre el volumen del agujero pasante y el volumen del pasador. La fórmula es:
Volumen de la unión soldada = Volumen del orificio pasante - Volumen de la patilla + (2 x Volumen del filete de soldadura)
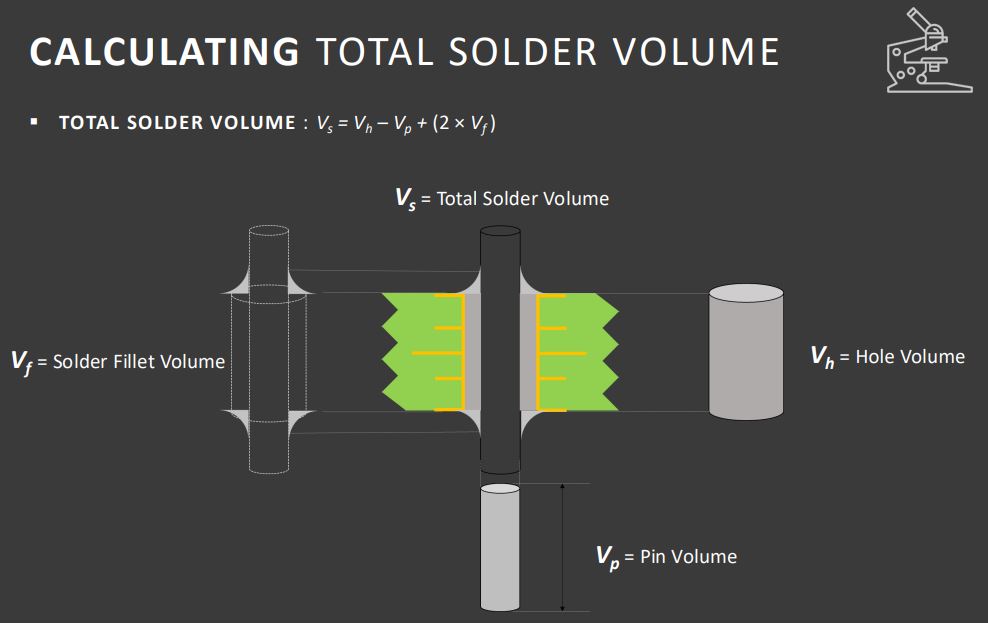
Esta fórmula tendrá en cuenta la cantidad de soldadura necesaria para garantizar un llenado adecuado del barril de orificios pasantes. Para el volumen del agujero pasante, Vh:
Vh = πRo2H
Dónde Ro es el radio del agujero pasante y H es la altura del agujero pasante o el grosor de la placa de circuito impreso. El volumen del filete de soldadura, Vfpuede calcularse mediante la siguiente fórmula, derivada del Teorema del Centroide de Pappus:
Vf = 2πA(0.2234R2 + Rt)
Donde radio de filete, Res igual a la diferencia entre el radio de la pastilla y el radio del pasador (R = Rp-Rt). Área del filete, Aes igual a 0,215R2. Para calcular el volumen del alfiler, Vp:
Vp = πRt2H
Una vez Vh, Vfy de Vp la fórmula del volumen de la unión soldada se reduce a lo siguiente:
Vs = Vh - Vp + (2 x Vf)
Puesto que, la pasta de soldadura es aproximadamente 50% soldadura por volumen, un factor de reducción, Fpara determinar la cantidad de pasta de soldadura necesaria. El factor de reducción suele oscilar entre 0,45 y 0,55, dependiendo de la formulación de la pasta de soldadura. La fórmula para calcular el volumen de pasta de soldadura, Vsp...es:
Vsp = Vs/F
Aperturas del esténcil
Una vez determinado el volumen de pasta de soldadura, el siguiente paso es diseñar el esténcil utilizado para el proceso. Para un diseño general de apertura circular, utilice:
Vsp = πr2t
Dónde r es el radio de la abertura y t es el grosor de la pantalla. Para una abertura rectangular general, utilice:
Vsp = lwt
Dónde l es la longitud, w es la anchura, y t es el grosor de la pantalla. Utilice la aritmética para ajustar el radio de las aberturas circulares o la longitud y la anchura de las aberturas rectangulares para satisfacer el volumen necesario de pasta de soldadura requerida, Vsp. Dependiendo de la aplicación requerida, pueden ser beneficiosas diferentes formas de apertura. Como puede verse en la figura 2, pueden utilizarse diversas formas y tamaños de apertura para aumentar el rendimiento durante el proceso.
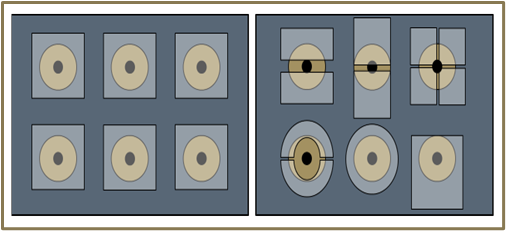
Consideraciones sobre PCB
El objetivo principal de un proceso PiP es crear una unión soldada de calidad. Existen varias consideraciones relativas a las placas de circuito impreso que pueden facilitar su aplicación.
La almohadilla que rodea el cañón debe ser lo más pequeña posible, manteniendo las propiedades mecánicas adecuadas. En general, es el doble del diámetro del cilindro revestido. Esto tiene la ventaja de reducir la pasta necesaria para cumplir la norma IPC-610G 4.3.2.1.
Otra consideración a tener en cuenta en la PCB es la relación cable/agujero. Como ya se ha mencionado, debe ser lo más pequeña posible, pero debe tener en cuenta las tolerancias del conector y la placa de circuito impreso para permitir variaciones en la precisión de la colocación, al tiempo que requiere fuerzas de inserción mínimas.
Para cumplir el requisito de volumen de soldadura de un proceso PiP, es necesario imprimir pasta de soldadura en la máscara de soldadura de la PCB, como se ve en la Figura 3. La sobreimpresión en la máscara de soldadura puede estar limitada por el espacio y la ubicación en la PCB. La sobreimpresión en la máscara de soldadura puede estar limitada por el espacio y la ubicación en la PCB. La máscara de soldadura y el acabado de la superficie del pad pueden influir significativamente en el resultado. Una máscara de soldadura con una alta energía superficial mantendrá la soldadura fundida plana, mientras que una soldadura refluida sobre una máscara con una baja energía superficial tenderá a formar cordones y puede interferir con el componente mientras está en estado líquido debido a un alto ángulo de humectación. La máscara de soldadura también debe aplicarse al cobre expuesto para garantizar que la soldadura fundida fluya hacia el barril, y todas las vías que no sean de prueba deben cubrirse. Además, los acabados superficiales fácilmente soldables, como HASL y ENIG, favorecerán la humectación y mejorarán los resultados.
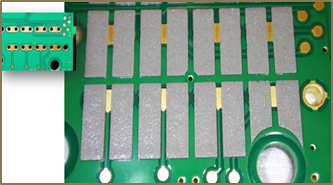
Selección de pasta de soldadura
Una variable clave en la soldadura PiP es la pasta de soldadura utilizada. Hay una serie de propiedades de la pasta que pueden tener una gran influencia en el éxito de la soldadura PiP. Algunas de las más significativas son el asentamiento en caliente, la humectación, el tipo de aleación y las características de los residuos. El asentamiento en caliente de la pasta de soldadura se comprueba según IPC TM-650 2.4.35 Sec. 5.2.2. Este ensayo cuantifica la capacidad de un depósito de pasta de soldadura para resistir la deformación a 150°C durante 10-15 minutos. Se trata de una propiedad importante, ya que la pasta que puede resistir el desprendimiento tiene menos probabilidades de caerse y salirse del barril antes de convertirse en líquida. Una pasta de soldadura con mejores propiedades de humectación mejorará la capacidad del proceso y puede superar algunos de los problemas mencionados. La química del fundente y la aleación pueden afectar al rendimiento de humectación. Por ejemplo, a medida que se investigan las aleaciones de baja temperatura, debe evaluarse el impacto de las propiedades humectantes en el rendimiento de la PiP.
Consideraciones sobre el reflujo
El perfil de reflujo de la pasta de soldadura puede manipularse para influir en el resultado de la calidad de la unión soldada de todo el conjunto de la placa de circuito impreso, no sólo del componente PiP. A la hora de ajustar el perfil para obtener el mejor resultado posible, hay que tener en cuenta una serie de factores. Los factores restrictivos más comunes a la hora de desarrollar un perfil de reflujo son las recomendaciones de pasta de soldar, las limitaciones de temperatura de los componentes, las características de la masa térmica del conjunto y la capacidad y limitaciones del horno. El perfil utilizado debe ajustarse a estas limitaciones y, al mismo tiempo, satisfacer los objetivos de calidad de la aplicación.
Evaluación de la calidad
La calidad de las uniones soldadas PiP debe cumplir los criterios IPC-610 para las Clases 1, 2 y 3. Los rayos X no destructivos y los cortes transversales destructivos pueden proporcionar pruebas definitivas sobre el éxito del proceso.
Procesos posteriores
La incorporación de un proceso PiP puede tener implicaciones inesperadas para una serie de procesos posteriores al reflujo. Dado que la pasta de soldadura es 50% fundente en volumen, añadir pasta adicional a la PCB para lograr el llenado del barril puede aumentar significativamente la cantidad de residuos de fundente post-soldadura. Tenga en cuenta que el fundente líquido utilizado en la soldadura por ola y selectiva deja muy pocos residuos. El aumento de residuos de pasta de soldadura puede causar una serie de problemas:
- Estética - Sencillamente, el aumento de residuos de fundente no es atractivo a la vista.
- ICT - El aumento de residuos de fundente puede interferir con las sondas de prueba que entran en contacto con la zona de prueba, lo que provoca "falsas llamadas". Puede ser necesario un mayor mantenimiento de los dispositivos de prueba, así como la sustitución y limpieza de las sondas.
- Horno de reflujo - El aumento de pasta conduce a un aumento de los volátiles de fundente que se generan durante el proceso de reflujo. Esto resulta en la acumulación de residuos de fundente en el horno, causando una mayor limpieza del sistema de gestión de fundente y goteo de fundente en el horno de reflujo. Además, la pasta desplazada del barril durante el proceso de inserción puede caerse de la punta del pasador y acumularse en el fondo del horno de reflujo.
- Los residuos de fundente y/o pasta de soldadura pueden fluir hasta el extremo del conector, lo que puede infringir las normas de calidad o interferir con las limitaciones de holgura y tolerancia.
Conclusión
Los componentes con orificios pasantes siguen siendo habituales y es poco probable que desaparezcan en un futuro próximo. Los ensambladores modernos adoptan constantemente nuevos procesos y optimizan los existentes. Se ha demostrado que PiP puede ayudar a reducir los costes operativos, simplificar el proceso de producción, reducir la huella de la línea de montaje y ahorrar energía. A medida que se incorporan nuevas aleaciones, dispositivos más pequeños y nuevas tecnologías, la PiP sigue siendo una técnica útil para la industria del ensamblaje de placas de circuito impreso.