Por Timothy O'Neill
En el montaje de placas de circuito impreso (PCB), la integridad de la máscara de soldadura es primordial. Esta capa protectora, diseñada para proteger las superficies de cobre y evitar puentes de soldadura entre los componentes, desempeña un papel crucial para garantizar la fiabilidad y funcionalidad de los dispositivos electrónicos.
Sin embargo, las máscaras de soldadura pueden presentar varios problemas, como agrietamiento, delaminación, descascarillado y presencia de residuos cerosos o aceitosos. Estos defectos pueden dar lugar a complicaciones como la formación de microesferas de soldadura, la formación de puentes y los rastros de caracol de soldadura, especialmente visibles tras procesos de soldadura por ola.
Estos problemas no sólo comprometen la calidad y la fiabilidad a largo plazo de la placa de circuito impreso, sino que también pueden dar lugar a importantes repeticiones de la producción y a un aumento de los costes.
Causas comunes de problemas con la máscara de soldadura
Los problemas con las máscaras de soldadura pueden deberse a varios factores, desde el proceso de fabricación hasta los materiales utilizados. Estas son algunas de las causas más comunes:
- Preparación inadecuada de la superficie: Para que una máscara de soldadura se adhiera correctamente, la superficie de la placa de circuito impreso debe estar limpia y libre de contaminantes. Cualquier residuo u oxidación/humedad puede afectar significativamente a la adherencia de la máscara.
- Curado incorrecto: Las máscaras de soldadura requieren un curado adecuado para lograr una adhesión y durabilidad óptimas. Las máscaras de soldadura insuficientemente curadas son susceptibles a cualquier líquido y pueden dañarse fácilmente durante el proceso de soldadura debido a la absorción de fundente y a una volatilización inadecuada. Un endurecedor insuficiente en la composición de la máscara de soldadura también puede hacer que nunca se endurezca completamente después del curado.
- Porosidad de la máscara de soldadura: En ocasiones, las máscaras de soldadura pueden presentar porosidad en función del tipo de máscara de soldadura utilizada, el proceso de aplicación y el proceso de curado. A través de estos pequeños orificios pueden filtrarse productos químicos como fundentes y productos de limpieza, así como humedad. Esto puede provocar problemas de fiabilidad, así como corrosión u otros daños con el paso del tiempo.
- Factores medioambientales: La máscara de soldadura puede absorber sustancias químicas durante la fabricación de los PCB, que pueden llegar a ser altamente higroscópicas o corrosivas. Cuando se exponen a condiciones de campo, estas sustancias absorbidas pueden hacer que el PCB experimente fallos debido a los efectos combinados de la humedad, el calor y el estrés eléctrico.
Casi todos los casos de deslaminación de la máscara de soldadura están relacionados con la propia placa de circuito impreso y no con el fundente o el equipo utilizado en el proceso de montaje. Si la máscara de soldadura muestra daños visibles o si hay residuos aceitosos o cerosos presentes, esto podría indicar problemas con la adhesión o el curado inadecuado de la máscara, o potencialmente una combinación de ambos factores.
Otros signos de un problema son los rastros de caracoles de soldadura, microesferas de soldadura o puentes tras el proceso de soldadura. Es crucial identificar y resolver estos problemas para evitar que se vean comprometidas las prestaciones y la integridad de las placas de circuito impreso.
A continuación se indican algunas pruebas sencillas que el ingeniero puede realizar en el taller para ayudar a determinar la causa principal.
Comprobación de la adherencia: La prueba de la cinta adhesiva
Esta prueba consiste en aplicar un trozo de cinta adhesiva transparente de al menos 5 cm de longitud. Presione la cinta sobre la placa y tire de ella rápidamente hacia arriba formando un ángulo de aproximadamente 90 grados con la superficie de la PCB (Figura 1). Si la cinta despega la máscara, se trata de un problema de adherencia. El método de prueba oficial del IPC (2-4-28) utiliza cinta adhesiva 3M Marca 600 de ½ pulgada (también conocida como "Scotch"), pero si no es lo que hay en su dispensador, utilice lo que haya.
Si la máscara se levanta, observe el estado del cobre que hay debajo. Si el cobre está brillante, es probable que no se haya preparado adecuadamente para la aplicación de la máscara de soldadura. Un acabado mate indica una limpieza y desbaste adecuados de las superficies antes de la aplicación de la máscara.
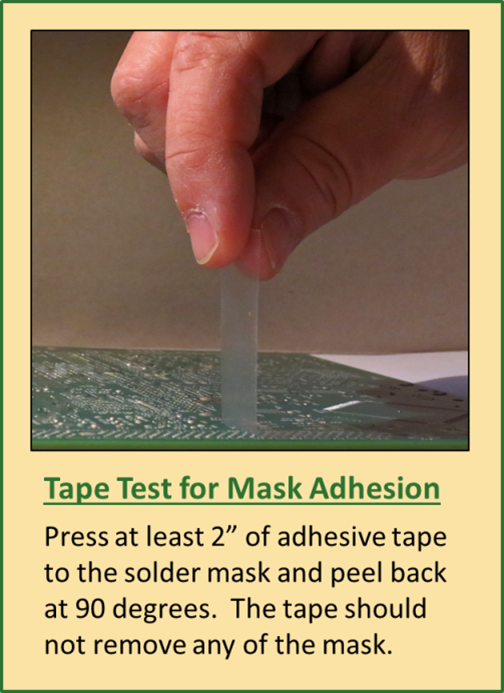
Comprobaciones de curado y dureza
Puede realizar las tres pruebas siguientes para comprobar el curado y la dureza de la máscara.
La prueba del lápiz: Busca un lápiz de madera y sácale punta. Sosténgalo en un ángulo de 45° y presione con firmeza alejándolo de usted (figura 2). Si la máscara de soldadura se levanta o desportilla, no está suficientemente dura. Esto puede ser el resultado de un curado inadecuado o de un endurecedor insuficiente añadido a la máscara antes del curado.
El lápiz que utilizaste era probablemente un #2H (todos estamos familiarizados con ellos por los exámenes estandarizados). Los lápices se clasifican según una escala de dureza, y cualquier grafito de dureza inferior a #6H no debería perforar la máscara de soldadura. Si quieres un #6H, o un kit completo de lápices de dureza variable, se venden en tiendas de material de arte.
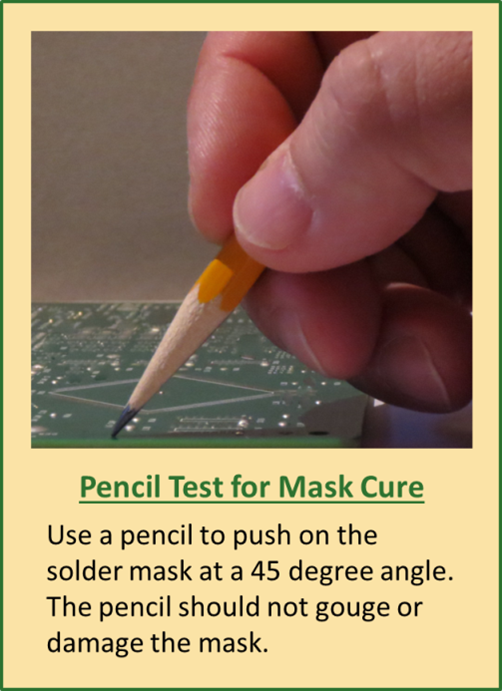
La prueba del horneado: Realice esta prueba colocando la placa de circuito impreso en un horno precalentado a 175°C y deje que la temperatura de la placa alcance los 155°C. Una vez a esta temperatura, mantenga la placa a 155°C durante exactamente 60 minutos. Asegúrese de que el horno tiene una ventilación adecuada para eliminar los humos y plastificantes nocivos, evitando que se vuelvan a depositar en los acabados soldables, lo que podría dar lugar a problemas de humectación o mojado deficiente.
Si después de este tratamiento se resuelven problemas como el agrietamiento, la delaminación y la presencia de residuos aceitosos o cerosos, indica que la máscara de soldadura estaba poco curada, y el horneado adicional ha ayudado a completar el proceso de curado.
Sin embargo, si los problemas persisten, esto puede sugerir que la formulación de la máscara de soldadura era incorrecta, debido potencialmente a una cantidad insuficiente de endurecedor añadido durante la preparación.
Toallitas de comprobación de máscaras de soldadura: BLT Circuit Services ofrece toallitas fáciles de usar para comprobar la máscara de soldadura. Estas toallitas están diseñadas para realizar una prueba cualitativa rápida con el fin de identificar máscaras de soldadura insuficientemente curadas en placas de circuito impreso. Para utilizarlas, extraiga una toallita del envase, asegurándose de que el envase está bien cerrado. Frote la toallita sobre la placa de circuito impreso con una presión moderada durante unos 10-15 segundos en varias zonas.
Si la máscara de soldadura no está suficientemente curada, el color de la resistencia se transferirá a la bayeta, lo que indica problemas de adhesión o curado de la máscara (Figura 3). Si se produce una transferencia de este tipo, es posible que la placa de circuito impreso tenga defectos y debe comunicarse al proveedor para que los corrija.
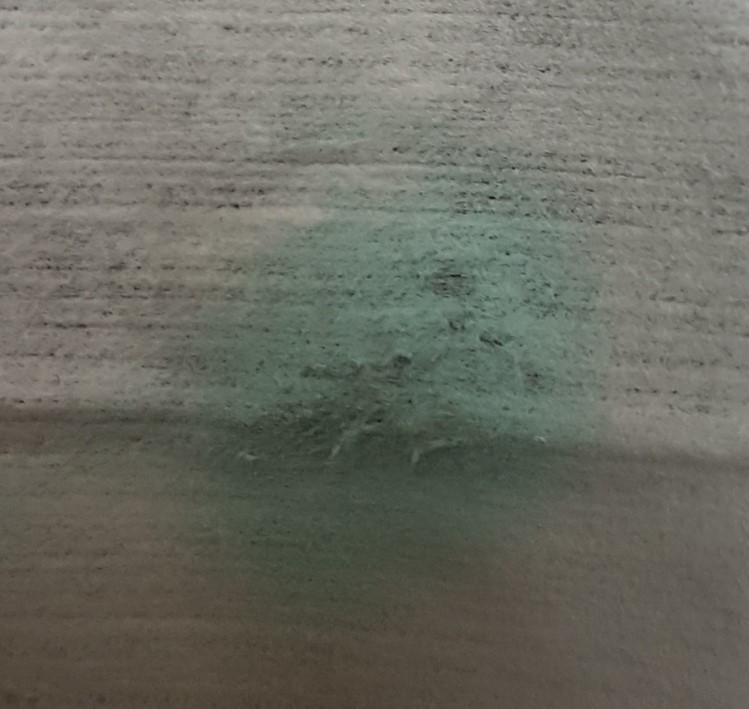
Caso práctico: Cómo la química de los fundentes puede agravar los problemas de las máscaras de soldadura
Aunque los problemas de la máscara de soldadura suelen derivarse de problemas de aplicación que pueden identificarse mediante las comprobaciones descritas anteriormente, la interacción entre la máscara y la química del fundente también puede causar problemas en raras ocasiones. Aquí describimos una situación en la que el problema estaba relacionado, al menos parcialmente, con el fundente.
El problema
En este caso, un fundente líquido parecía estar interactuando con la máscara de soldadura, haciéndola aparecer brumosa y agrietada, incluso levantándola del sustrato. El problema parecía producirse con mayor frecuencia y gravedad alrededor de las trazas. Una revisión del proceso de soldadura por ola no indicó pasos, parámetros o tiempos de exposición inusuales que pudieran causar daños en la máscara de soldadura, y el fabricante de PCB insistió en que se trataba de un problema de fundente.
Resolución de problemas y pruebas de la máscara de soldadura
Pedimos al usuario que realizara algunas de las pruebas sencillas de máscara de soldadura mientras investigábamos el número de lote del fundente para ver si había algún cambio de producción u otras preocupaciones de los clientes relacionadas con él. No encontramos cambios ni preocupaciones en los registros, pero este fundente en particular era un material muy especializado, de lotes pequeños. Nos planteamos la hipótesis de que tal vez se hubieran producido algunas variaciones durante su vida útil, por lo que probamos una muestra devuelta por el usuario, pero tampoco encontramos ningún problema.
Mientras tanto, la máscara no superó la prueba de la cinta y la prueba de limpieza de la máscara de soldadura. Después, al investigar más a fondo la química de la máscara y el fundente, descubrimos que la máscara era un producto más nuevo, sin halógenos.
Identificar la causa
La composición única de la máscara y la falta de un curado suficiente provocaron que siguiera siendo muy porosa. Como resultado, el fundente fue absorbido en la subsuperficie de la resistencia a la soldadura, donde no pudo volatilizarse adecuadamente como se esperaba durante la fase de precalentamiento.
Una vez que la placa se encontraba con la ola de soldadura, el fundente absorbido hervía entre la resistencia y las capas de cobre, socavando la adherencia entre la resistencia de soldadura y las pistas de cobre base. Esta información, junto con los fallos de la prueba de la máscara de soldadura, ayudó al ensamblador a demostrar el problema a su fabricante de placas de circuito impreso y a encontrar una solución.
Reflexiones finales
No es inusual que el proveedor de productos químicos para soldadura dirija el análisis de la causa raíz de los problemas de soldadura. De hecho, tiene mucho sentido. El personal de asistencia técnica de soldadura ve tantos procesos y problemas diferentes y variados, que son solucionadores de problemas naturales y un gran recurso para los ingenieros de procesos. La evaluación adecuada del rendimiento de los materiales se basa a menudo en pruebas derivadas de los conocimientos de causa y efecto que sólo se adquieren con la experiencia.
Un proveedor de calidad no debe intentar pasar la responsabilidad de los problemas del proceso a los demás, sino comprometerse a llevar al cliente a la solución más rápida y eficaz, independientemente del fallo. La estrategia de "pasar la pelota" puede ser contraproducente y poner en peligro el negocio; sin embargo, por alguna razón inexplicable, sigue siendo habitual. Hasta que se erradique, siga llamando a los soldadores; gran parte de nuestra valiosa experiencia la adquirimos a través de los retos de nuestros clientes.