RESUMEN
A medida que la industria electrónica se esfuerza continuamente por innovar y mejorar la eficacia de los procesos de ensamblaje y reprocesado, el estudio de las aleaciones de soldadura a baja temperatura (LT) ha atraído una gran atención. Este artículo ofrece un análisis exhaustivo de las soldaduras a baja temperatura, centrándose especialmente en su aplicación en los procesos de reparación y en las implicaciones más amplias para la fabricación de productos electrónicos. Nos adentramos en diversas facetas de la soldadura a baja temperatura, examinando tanto los beneficios potenciales como los retos asociados a su uso.
El estudio revisa trabajos anteriores sobre la soldadura LT en el retrabajo, ofreciendo un resumen detallado y sugiriendo un enfoque prudente debido al aumento de los costes y las complejidades asociadas con el alambre de soldadura que contiene bismuto, junto con la falta de diferencias sustanciales en la resistencia y fiabilidad de la unión en comparación con los métodos tradicionales. Además, el artículo aborda consideraciones más generales sobre la soldadura LT, como las ventajas e inconvenientes, las ventajas y desventajas en cuanto a rendimiento y las áreas que requieren un estudio más profundo.
Esta investigación sobre la soldadura LT se enriquece con nuevos datos sobre la limpieza de residuos de óxido de bismuto y los efectos de la temperatura de la punta y el tiempo de contacto en la formación de IMC durante el retrabajo. Al proporcionar una visión completa de la investigación existente y los nuevos hallazgos, este artículo pretende ofrecer información valiosa a los fabricantes, ingenieros e investigadores, contribuyendo a la toma de decisiones informadas con respecto a la adopción e integración de la soldadura LT en el retrabajo y ensamblaje de componentes electrónicos.
INTRODUCCIÓN
En una era en la que la innovación y la eficiencia se han convertido en aspectos primordiales, la industria de fabricación electrónica busca constantemente vías para mejorar los procesos, reducir los costes y aumentar la fiabilidad de los productos. Entre las diversas soluciones exploradas, la soldadura a baja temperatura (BT) ha surgido como una alternativa prometedora a los métodos de soldadura tradicionales, especialmente con la proliferación de componentes electrónicos intrincados y miniaturizados.
Históricamente, el uso de la soldadura LT ha estado motivado por sus características únicas, como un punto de fusión reducido y el potencial de ahorro de energía y material.[1]
Sin embargo, como ocurre con cualquier cambio significativo en la metodología, la implantación de la soldadura LT ha planteado una serie de retos. Estos retos, desde la fiabilidad hasta la gestión de residuos, pasando por los problemas de reprocesamiento, exigen una exploración y una comprensión más profundas.
Este artículo profundiza en los entresijos de la soldadura LT, concretamente en el ámbito de la reelaboración y el ensamblaje de componentes electrónicos. A través de un examen riguroso y una combinación de datos experimentales y conocimientos de la industria, pretendemos arrojar luz sobre el verdadero potencial, los beneficios y las consideraciones del empleo de la soldadura LT en la fabricación electrónica contemporánea.
ANTECEDENTES
La información sobre las principales características y problemas asociados a la soldadura a baja temperatura suele ser dispar, y tanto los estudios en curso como los ya existentes se ven entorpecidos por diferencias en las metodologías, el enredo con los esfuerzos de marketing y la falta de conclusiones metaanalíticas lo suficientemente sólidas como para ofrecer a los fabricantes perspectivas directas y procesables. Este documento pretende iniciar el proceso de reunir la información existente en una imagen cohesiva, identificando tanto los beneficios como los retos asociados a la soldadura a baja temperatura en diferentes dimensiones, a la vez que delimita claramente las cuestiones pendientes y las áreas de estudio, así como las conclusiones estandarizadas de los trabajos existentes.
Aleaciones de baja temperatura
Las soldaduras LT se caracterizan por sus composiciones metálicas únicas, en las que intervienen principalmente el estaño (Sn) y el bismuto (Bi). Históricamente, la presencia de plomo (Pb) en las soldaduras era habitual, pero con el cambio hacia procesos sin plomo, el bismuto se ha convertido en un componente más viable.[2] El protagonismo del estaño y el bismuto en estas aleaciones marca un cambio significativo en la tecnología de las soldaduras. El bismuto, que antes se pasaba por alto debido a su incompatibilidad con los procesos basados en Pb, es ahora parte integrante de las soldaduras LT, sobre todo porque la mayoría de los procesos de soldadura han pasado a ser sin Pb. Esta transición ha impulsado el desarrollo de nuevas generaciones de soldaduras LT. Aunque está surgiendo una creciente variedad de composiciones de soldaduras LT, este artículo se centrará principalmente en el estaño-bismuto eutéctico y el estaño-bismuto con una pequeña adición de plata (Ag), ya que estas composiciones representan una parte significativa de las aplicaciones actuales de soldaduras LT.
Principales ventajas e inconvenientes de la soldadura LT
Las principales ventajas de la soldadura LT residen en sus temperaturas de fusión más bajas en comparación con las soldaduras tradicionales. Esta característica conlleva varias ventajas. La primera es un menor consumo de energía. El punto de fusión más bajo permite ahorrar energía durante el proceso de soldadura, ya que se necesita menos calor. De hecho, algunos estudios han demostrado un ahorro potencial de energía de hasta 20-40% utilizando perfiles de reflujo de baja temperatura frente a los de la SAC305 tradicional.[3]
Otra ventaja es la reducción del alabeo de los componentes. Las temperaturas más bajas reducen el riesgo de deformación de componentes sensibles durante la soldadura, mejorando así la integridad del producto.
Sin embargo, estas ventajas se ven contrarrestadas por ciertos inconvenientes. En particular, el bismuto, aunque ventajoso para reducir el punto de fusión, introduce fragilidad en las uniones soldadas. Esto puede afectar a la fiabilidad y durabilidad de las conexiones soldadas, especialmente en entornos en los que la tensión mecánica es un problema.
Otro inconveniente está relacionado con la sensibilidad a la temperatura. Aunque las temperaturas más bajas son beneficiosas para ahorrar energía y reducir el alabeo, también requieren un control y una calibración cuidadosos durante el proceso de soldadura para garantizar la integridad de la unión.
También se plantean cuestiones relacionadas con la creación de uniones híbridas (a menudo SAC+LT) en diversos escenarios y cuáles son las características y modos de fallo de dichas uniones.[4] Esto es algo que ya hemos investigado en el caso de la soldadura a baja temperatura. Los cambios en el proceso son otra área de exploración, como el ajuste de las velocidades de rampa y el uso de hornos de reflujo con zonas de refrigeración. [5][6]
Soldadura a baja temperatura
Una cuestión que se plantean muchos fabricantes a la hora de implantar procesos de soldadura a baja temperatura es si pueden o deben utilizar también soldadura a baja temperatura en cualquier retrabajo realizado en componentes que hayan sido soldados con soldadura LT. Esta pregunta tiene dos vertientes: en primer lugar, si la soldadura LT en el proceso requiere soldadura LT en el retrabajo para mantener la integridad de la unión y, en segundo lugar, si el uso de soldadura LT en el retrabajo aporta beneficios adicionales y ahorro de costes, de forma similar a como lo hace la soldadura LT utilizada en la soldadura por reflujo y por ola.
El objetivo del debate es proporcionar una comprensión global del papel de la soldadura LT en el reprocesamiento, destacando las consideraciones clave para los fabricantes que contemplen su adopción en sus protocolos de reparación y mantenimiento.
Resumen de estudios anteriores
El estudio original exploraba la viabilidad de las aleaciones LT en escenarios de retrabajo.[7] Se observó que el hilo sólido de baja temperatura de fusión y el fundente externo, así como la soldadura de hilo SAC305 con núcleo de fundente, podían emplearse con éxito para reelaborar aleaciones LT. La soldadura LT presentaba características de procesado distintas a las de la soldadura SAC, pero éstas no impedían la formación de uniones soldadas de calidad.
Fundamentalmente, las uniones soldadas creadas con soldadura LT cumplieron los criterios IPC Clase 1, 2, 3, lo que sugiere que la soldadura LT es una opción viable para una serie de clases de productos. Sin embargo, los resultados de las pruebas de cizallamiento fueron variables, lo que refleja los retos inherentes a los procesos de reelaboración. Las uniones soldadas con SAC demostraron una mayor ductilidad en comparación con sus homólogas con bismuto, lo que concuerda con las propiedades conocidas de los materiales de estas aleaciones. Cuando se utilizó soldadura con hilo tubular SAC305, el proceso se asemejó a los métodos tradicionales de retrabajo SAC/SAC, con un énfasis en la utilización de diámetros de hilo más finos para componentes más pequeños.
El estudio puso de relieve la importancia de la destreza del operario, subrayando la necesidad de una formación adecuada a la hora de aplicar el retrabajo a baja temperatura. Esto es especialmente relevante dada la naturaleza variable de los resultados del retrabajo, incluso bajo la dirección de un operario muy experimentado.
Cuestiones sin resolver del estudio inicial
Varias cuestiones quedaron sin resolver, lo que justifica una mayor investigación. Una de las cuestiones clave sin resolver es la capacidad de limpieza de los residuos de óxido de bismuto tras el reflujo y la reelaboración. Este aspecto es crucial para garantizar la fiabilidad y el rendimiento a largo plazo de las uniones soldadas.
El estudio original también indicaba que las variables en las técnicas de soldadura manual, en particular la temperatura de la punta y el tiempo de contacto, influyen significativamente en la formación de compuestos intermetálicos (IMC). Comprender estas variables es esencial para optimizar los procesos de reelaboración y garantizar la integridad de las uniones soldadas.
Estas cuestiones sin resolver se investigaron como se describe en las dos secciones siguientes.
Limpiabilidad del residuo de óxido de bismuto
Una de las principales preocupaciones en torno al uso de la soldadura LT es la posibilidad de que queden residuos de óxido de bismuto tras los procesos de reflujo y repaso. La presencia de este residuo puede afectar a la calidad y fiabilidad de la unión soldada, aunque se considera principalmente cosmético. Se llevó a cabo un estudio en colaboración con MicroCare para determinar si este residuo se podía limpiar y qué producto químico de limpieza funcionaba mejor.
Objetivo del experimento
El objetivo del estudio era evaluar la eficacia de diversos productos químicos de limpieza para eliminar los residuos de las juntas de soldadura creadas con soldaduras de baja temperatura (LT). Este estudio se centró especialmente en evaluar la capacidad de los distintos agentes de limpieza para eliminar los residuos de óxido de bismuto resultantes de los procesos de soldadura a baja temperatura.
Materiales utilizados
En este estudio se emplearon diversos materiales de soldadura. La selección incluyó pasta AIM M8 SAC305, pasta NC273LT Sn42/Bi57/Ag1, hilo de núcleo fundente SAC305 y Sn42/Bi57/Ag1 sólido en combinación con fundente NC280 (para componentes PTH) o NC217 (para componentes SMT).
Para evaluar el proceso de limpieza, se consideraron tres productos químicos de limpieza distintos. Dos de ellos eran limpiadores fluorados, denominados limpiadores X e Y, mientras que el tercero era un limpiador no fluorado denominado limpiador Z.
Montaje experimental y procedimiento
Para la fase de montaje y ensayo, se crearon cupones de prueba (PCB016) para cada limpiador examinado. El proceso de ensamblaje implicó varios pasos. Los cupones A y B se sometieron a reflujo con soldadura LT y se repasaron con hilo LT y fundente externo. El cupón C se sometió a reflujo con soldadura LT y se repasó con alambre SAC305 con fundente. El cupón D se sometió tanto a reflujo como a repaso con SAC305. Por último, el cupón E se sometió a reflujo con soldadura LT y no se retrabajó. El paso inicial de esta fase consistió en tomar fotografías del "antes" de todos los componentes.
El procedimiento de limpieza de sobremesa posterior consistió en la aplicación de disolvente de limpieza mediante una herramienta dispensadora. El proceso comprendía un ciclo de fregado en húmedo y secado, consistente en un fregado en húmedo de 20 segundos, un fregado de 20 segundos y un periodo de secado de 30-60 segundos. A continuación, se analizó meticulosamente la limpieza de los cupones al microscopio y se tomaron fotografías del "después".
Resultados
Tras una minuciosa experimentación, el limpiador X resultó ser el más eficaz para las muestras consideradas. La eficacia de la limpieza se evaluó además examinando cupones de prueba específicos. Los cupones de prueba B, C y E mostraron los resultados de limpieza más satisfactorios con el limpiador X, lo que significaba una eliminación satisfactoria de los residuos con LT+LT, LT+SAC y LT sin repaso, respectivamente (véase la figura 1). Sin embargo, el cupón de prueba A (LT+LT) mostró ligeros residuos en ciertas zonas, lo que contrasta con su gemelo, el cupón de prueba B. El cupón de prueba D (SAC+SAC) mostró varias zonas de residuos notables tras la limpieza, como se ilustra en las figuras 2 y 3.
Figura 1. Componentes del cupón de ensayo C antes (izquierda) y después (derecha) de la limpieza con Cleaner X
Figura 2. Cupón de prueba A antes (izquierda) y después (derecha) de la limpieza con Cleaner X
Figura 3. Cupón de prueba D antes (izquierda) y después (derecha) de la limpieza con Cleaner X
Conclusión
El estudio concluyó que, aunque el proceso de limpieza con Cleaner X fue eficaz para la mayoría de los cupones de prueba, hubo una notable variabilidad en la eliminación de residuos en las distintas muestras. El estudio subraya la importancia de seleccionar el producto químico de limpieza adecuado y seguir rigurosamente el procedimiento de limpieza para garantizar una eliminación eficaz de los residuos.
Consideraciones sobre el crecimiento de IMC y variables en las técnicas de soldadura manual
El crecimiento del compuesto intermetálico (IMC) es un factor crucial a la hora de evaluar la fiabilidad de la unión soldada. El estudio inicial había mostrado resultados comparables entre varias combinaciones de soldadura en términos de ensayo de cizallamiento y espesor del IMC. Sin embargo, la velocidad de crecimiento del IMC y la importancia del tiempo de permanencia en esta formación siguen siendo objeto de intenso escrutinio. Desentrañar la dinámica del crecimiento de IMC en el contexto de la soldadura LT puede aportar más claridad sobre la viabilidad a largo plazo de la soldadura.
Efectos de la variación de la soldadura manual en IMC y otras características
Este estudio se inició para abordar la segunda pregunta de seguimiento del documento inicial Low Temperature Rework.[7] Metcal, empresa especializada en la fabricación de equipos de soldadura manual, se investigó el impacto de la temperatura de la punta y el tiempo de contacto en la formación de compuestos intermetálicos (IMC) y otras características al utilizar soldadura a baja temperatura (LTS).
Materiales utilizados
En el estudio se utilizó la aleación Sn42/Bi57/Ag1 tanto para reflujo como para retrabajo, y junto con el hilo se empleó el fundente NC280 de AIM. Los componentes soldados fueron cinco componentes con agujeros pasantes chapados (PTH), que incluían tres resistencias y dos condensadores, en un único modelo de placa de circuito impreso. La soldadura manual se realizó con un soldador CVC-6CH0025S con punta de cincel de 2,5 mm.
Montaje experimental y procedimiento
En este experimento se variaron las condiciones de soldadura, con dos temperaturas de punta diferentes, a saber, 285°C y 343°C, con los correspondientes ajustes en los tiempos de contacto. Concretamente, para 285°C, los tiempos de contacto se fijaron en 3s, 4s (línea de base), 5s y 6s. Mientras tanto, a 343°C, los tiempos de contacto fueron de 2s (línea de base), 3s, 4s y 5s.
Los parámetros de evaluación se centraron en un análisis exhaustivo de diversos aspectos, como las juntas de soldadura, las características de los residuos, las propiedades de humectación, la corrosión, la forma de la junta de soldadura, la confirmación del relleno del barril, el grosor IMC y la presencia de huecos.
Resultados
En el examen de las juntas de soldadura, se observó que algunas juntas presentaban un ángulo de contacto superior a 90° a 285°C, especialmente notable a un tiempo de contacto de 3 segundos. Por el contrario, a 343 °C, algunas juntas presentaban un exceso de soldadura en la parte superior, como se muestra en la figura 4.
Figura 4. Ángulo de contacto de la patilla del condensador después de la reelaboración a 285°C, tiempo de contacto de 3 segundos
En cuanto a los residuos, el color se oscureció en correlación con el tiempo de contacto para ambas temperaturas de punta, como se ilustra en la Figura 5.
Figura 5. Residuo inferior de componentes reelaborados a 343°C
Las propiedades de humectación de la soldadura fueron notables, presentando un aspecto brillante y suave y proporcionando una buena cobertura del área de la almohadilla en la mayoría de las uniones.
No se detectaron casos de corrosión en los PCB analizados.
La forma de las uniones soldadas se vio influida por las condiciones de temperatura. Los componentes sometidos a 343°C formaron mejores uniones soldadas en los distintos tiempos de contacto en comparación con los sometidos a 285°C. Todos los barriles, excepto la resistencia con 3 y 4 segundos de tiempo de contacto a 285°C, se llenaron a 100%.
La investigación sobre el espesor de la IMC reveló que a 343°C, la IMC PCB/Soldadura era mayor en comparación con la IMC Pin/Soldadura. El grosor de la IMC era mayor en los componentes con 3 y 4 segundos de tiempo de contacto que en los de 2 y 5 segundos. A 285°C, el IMC de Pin/Solder fue mayor que el IMC de PCB/Solder, especialmente para resistencias con tiempos de contacto de 6 y 5 segundos. Los condensadores a 285°C no mostraron IMC Pin/Solder medible, lo que sugiere que era inferior a 1µm. Consulte la Figura 6, la Tabla 1 y la Tabla 2 para obtener información detallada.
Figura 6. Espesores de IMC tras la reelaboración de la patilla de la resistencia a 343°C, tiempo de contacto de 4 segundos
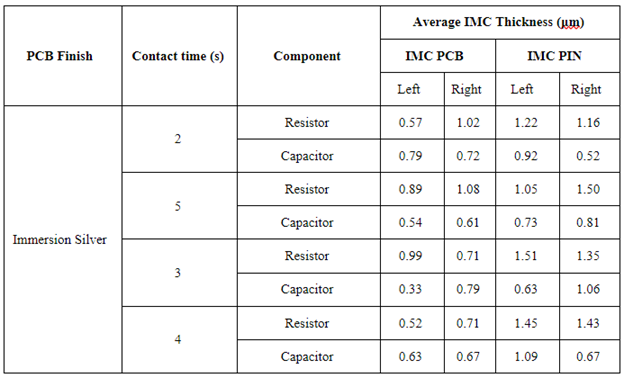
Cuadro 1. Espesor medio IMC 343°C
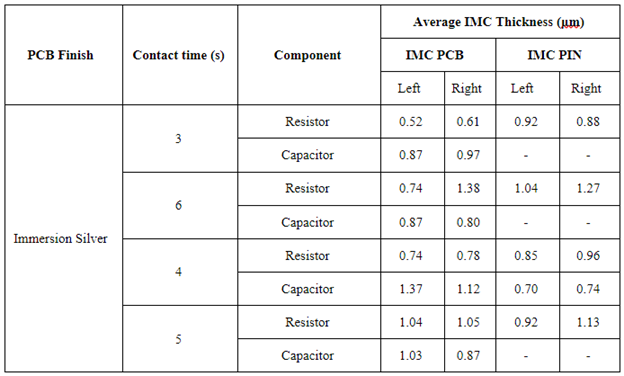
Tabla 2. Espesor medio IMC 285°C
Por último, la presencia de huecos fue una observación común, con más de 80% de los pernos mostrando huecos para ambas temperaturas y a través de diferentes tiempos de contacto.
Conclusiones
Los resultados indicaron que las diferentes temperaturas y los distintos tiempos de contacto influyen en la calidad de la unión soldada y en la formación de IMC. En cuanto a la pregunta de si el uso de soldadura LT en el retrabajo podría prolongar la vida útil de la punta o ahorrar energía, la respuesta parece ser negativa. En general, la temperatura más alta, 343°C, dio los mejores resultados, siendo 3-4 segundos el tiempo de contacto ideal.
Otras consideraciones para el crecimiento de la CIM
Los distintos enfoques de retrabajo, como LT+LT, LT+SAC y SAC+SAC, pueden influir en la formación de IMC de forma única. A medida que los fabricantes se plantean la adopción de la soldadura LT para el retrabajo, es imperativo comprender estas sutiles diferencias y sus posibles implicaciones. Muchos estudios recientes han analizado el crecimiento de IMC y la migración de bismuto en BGA, comparando los efectos de LT+LT, LT+SAC y SAC+SAC.[8] Sin embargo, los resultados de un estudio a otro no muestran una tendencia definida. También hay pruebas de que la rampa de temperatura, los índices de enfriamiento y los tiempos de permanencia pueden afectar significativamente a la integridad de la unión cuando se trata de soldaduras a baja temperatura, tanto si forman parte de una unión híbrida como si no, como se ha mencionado anteriormente. Esto parece indicar la posibilidad de una mayor variación en los resultados de la soldadura manual, dependiendo de los ajustes del equipo, así como de la experiencia del operario.
Argumentos a favor de la soldadura a baja temperatura en el retrabajo
A la hora de examinar los beneficios potenciales del uso de soldaduras de baja temperatura (LT) en los procesos de retrabajo, hay que tener en cuenta varios factores clave. Nuestros estudios e investigaciones han proporcionado información sobre cada uno de estos aspectos, dando forma a nuestra comprensión de la practicidad y eficacia de la soldadura LT en escenarios de retrabajo.
Ahorro en material de soldadura
Contrariamente a las expectativas de rentabilidad, el hilo de soldadura LT es significativamente más caro que el SAC305. Esto se debe a que un componente clave de la soldadura LT, el bismuto, no es muy dúctil, lo que hace que la fabricación del hilo de soldadura LT sea intrínsecamente más difícil. Este mayor coste socava una de las ventajas potenciales del uso de la soldadura LT en los procesos de reprocesado, convirtiéndola en una opción menos atractiva desde el punto de vista financiero.
Facilidad de uso
La facilidad de uso es otro aspecto en el que la soldadura LT no ofrece necesariamente ventajas. La necesidad de utilizar hilo sin núcleo y fundente externo complica el proceso de reparación. Además, exige un mayor nivel de experiencia y precisión por parte del operario. Estos factores contribuyen a que el proceso de reparación sea más complicado y complejo.
Ahorro de energía
Aunque la soldadura LT funde a temperaturas más bajas, lo que sugiere un ahorro potencial de energía, nuestros resultados indican que la integridad de la unión y la formación de IMC mejoran cuando se utiliza una temperatura de punta más caliente y un tiempo de contacto moderado. Esto indicaría que no se puede ahorrar energía en el retrabajo sin comprometer la integridad del trabajo.
Vida útil
Aunque existe la posibilidad teórica de que se prolongue la vida útil de las puntas debido a las temperaturas de funcionamiento más bajas, nuestra investigación sugiere de nuevo que esto no se confirmaría debido a la mejora de los resultados al soldar a una temperatura más alta.
Integridad de la articulación
Nuestro estudio inicial comparó el rendimiento de las configuraciones SAC+SAC, LT+SAC y LT+LT en términos de ensayos de cizallamiento y espesor IMC. Los resultados indicaron que el rendimiento de todas estas combinaciones era comparable. Sin embargo, siguen existiendo dudas sobre la tasa de crecimiento de la IMC y el tiempo de permanencia, que requieren una mayor investigación para comprender plenamente las implicaciones sobre la integridad de la junta.
Requisitos de temperatura del componente/sustrato
Una consideración importante en el uso de la soldadura LT es su impacto en el componente y el sustrato. Si la adopción de la soldadura LT en los procesos de reflujo conduce al uso de sustratos y componentes más baratos, éstos pueden tener sensibilidades de temperatura específicas en el reflujo que deben gestionarse cuidadosamente. Este aspecto del uso de la soldadura LT requiere un conocimiento matizado de los materiales implicados y sus respectivas tolerancias de temperatura.
Limpieza de residuos
Las soldaduras que contienen bismuto pueden dejar residuos de óxido de bismuto, tanto tras el reflujo como tras la reelaboración. De hecho, se observó gran parte de este residuo en los componentes reelaborados en el estudio de la variable del soldador. Sin embargo, se determinó que existe una solución y un proceso de limpieza que prácticamente eliminan este residuo.
Conclusión
Basándonos en las conclusiones acumuladas de nuestras investigaciones y estudios, la utilización de soldaduras de baja temperatura en los procesos de reprocesado no está firmemente respaldada. Aunque existen ventajas teóricas, la realidad práctica y los resultados de nuestras investigaciones sugieren que las ventajas son mínimas o se ven anuladas por otros problemas. Los fabricantes deben sopesar estos factores cuidadosamente a la hora de considerar la adopción de la soldadura LT para fines de retrabajo.
Casos de uso principales de la soldadura a baja temperatura
Por último, nos gustaría reevaluar el alcance más amplio de las aplicaciones de soldadura a baja temperatura (BT), teniendo en cuenta tanto sus limitaciones inherentes como las áreas en las que resulta prometedora.
Recordemos que las soldaduras LT son menos fiables en situaciones de estrés mecánico, como caídas, en las que la fragilidad puede ser un obstáculo importante. Sin embargo, pueden ser adecuadas para la electrónica de consumo, donde la durabilidad es menos crítica y mantener bajos los costes de fabricación es esencial para mantener la rentabilidad.
Entornos de aplicación controlados
En los casos en los que no se espera que el dispositivo sufra tensiones mecánicas significativas, como en entornos estacionarios o controlados, la fragilidad de la soldadura de estaño-bismuto puede no ser una preocupación importante.
Combinación con otras aleaciones
A veces, la soldadura de estaño-bismuto puede combinarse con otras aleaciones para mitigar su fragilidad. Por ejemplo, la adición de plata (Ag) puede mejorar su resistencia mecánica, haciéndola más adecuada para aplicaciones que requieren cierto nivel de resistencia a los golpes.
Componentes redundantes o no críticos
En algunos diseños, especialmente en automoción y aeroespacial, la soldadura de estaño-bismuto puede utilizarse para componentes redundantes o que no son críticos para la función principal del sistema, reduciendo así el riesgo asociado al fallo de la unión soldada.
Electrónica flexible
En la electrónica flexible, el interés suele centrarse en la flexibilidad más que en la resistencia a los choques mecánicos. En este caso, la baja temperatura de la soldadura de estaño-bismuto es beneficiosa para los materiales sensibles a la temperatura utilizados en estos dispositivos. Los propios dispositivos pueden estar diseñados para sufrir impactos o golpes mínimos.
Uso en componentes protegidos
Tanto en las aplicaciones de automoción como en las aeroespaciales, los componentes soldados con estaño-bismuto pueden alojarse en zonas protegidas mecánicamente, donde se minimiza la probabilidad de sufrir golpes por caídas.
Aplicación selectiva
La soldadura de estaño-bismuto podría utilizarse selectivamente junto con otros tipos de soldadura en un mismo ensamblaje, empleándose sólo en áreas específicas en las que su bajo punto de fusión resulte beneficioso y su fragilidad no sea un inconveniente significativo.
Técnicas avanzadas de envasado
Algunas técnicas modernas de embalaje electrónico pueden mitigar los efectos de la fragilidad de la soldadura, como el uso de materiales de relleno o el empleo de diseños específicos de placas de circuito impreso que reducen la tensión en las juntas de soldadura.
Piezas móviles
En automoción y aeroespacial, podría utilizarse para piezas sin movimiento o en aplicaciones en las que las juntas de soldadura no estén sometidas a tensiones mecánicas frecuentes o severas.
La electrónica de consumo en el punto de mira
El segmento de la electrónica de consumo resulta especialmente interesante a la hora de considerar la adopción de la soldadura LT. Se trata de productos diseñados a menudo pensando en un ciclo de vida corto, desde accesorios para móviles hasta auriculares económicos. Hay que tener en cuenta que, aunque los dispositivos desechables que utilizan soldadura LT pueden anular los beneficios medioambientales positivos del uso de la soldadura LT al contribuir a un exceso de residuos, en mercados específicos en los que los dispositivos electrónicos deben ser desechables (como determinadas aplicaciones médicas o de seguridad), la soldadura LT puede ayudar a mantener la rentabilidad.
Orientaciones futuras y recomendaciones
La exploración de la soldadura a baja temperatura (BT), su aplicación en el reprocesado y sus implicaciones más amplias para la industria electrónica han aportado, sin duda, una gran riqueza de conocimientos. Sin embargo, como ocurre con cualquier esfuerzo científico, el viaje ha desvelado tantas preguntas como respuestas. Sobre la base de los conocimientos reunidos hasta ahora, surgen varias direcciones y recomendaciones para el futuro.
Desarrollo y normalización de aleaciones
En un estudio de iNEMI, los encuestados manifestaron su deseo de que hubiera una aleación estándar en LT antes de querer invertir en hacer el cambio.[9] Como ya se ha dicho, aunque el estaño bismuto eutéctico es el modelo "básico" con el que se comparan o modifican aleaciones LT más sofisticadas para resolver los problemas existentes, todavía se está experimentando mucho con la adición de dopantes y otros elementos.
La mejora de la fiabilidad de las soldaduras de estaño-bismuto (Sn-Bi) a baja temperatura suele implicar la adición de otros elementos a la aleación. El objetivo de estas adiciones es mejorar determinadas propiedades, como la resistencia mecánica, el rendimiento en ciclos térmicos y la reducción de la fragilidad. Algunos de los elementos más eficaces para este fin son:
- Plata (Ag): Añadir plata a las aleaciones Sn-Bi es uno de los métodos más comunes para mejorar su resistencia mecánica y a la fatiga térmica. La plata puede aumentar la robustez general de la unión soldada, haciéndola menos propensa a fallos bajo tensión mecánica o ciclos térmicos.
- Cobre (Cu): El cobre es otro elemento que se suele añadir a las soldaduras Sn-Bi. Puede mejorar las características de humectación de la soldadura y sus propiedades mecánicas. El cobre también ayuda a reducir la tasa de crecimiento de IMC (compuestos intermetálicos), lo que puede ser beneficioso para la fiabilidad a largo plazo.
- Níquel (Ni): El níquel se utiliza para mejorar las propiedades mecánicas de la soldadura y estabilizar la capa intermetálica, reduciendo el crecimiento de fases frágiles. Esto puede ser especialmente beneficioso en aplicaciones en las que las uniones soldadas están sometidas a tensiones mecánicas.
- Antimonio (Sb): El antimonio puede añadirse a las soldaduras Sn-Bi para mejorar sus propiedades térmicas y mecánicas. Contribuye a refinar la microestructura de la soldadura, lo que mejora su rendimiento en ciclos térmicos y bajo tensión.
- Indio (In): El indio puede aumentar la ductilidad de la soldadura, haciéndola menos quebradiza. Esto puede ser especialmente útil en aplicaciones en las que la flexibilidad y la resistencia a la fatiga térmica son importantes.
Cada uno de estos elementos contribuye de forma diferente al rendimiento global de la soldadura. La elección del elemento o elementos a añadir depende de los requisitos específicos de la aplicación, como el entorno operativo, los tipos de tensiones a los que se enfrentarán las juntas de soldadura y el equilibrio deseado entre coste y rendimiento. Las proporciones de estos aditivos deben controlarse cuidadosamente, ya que una cantidad excesiva puede provocar otros problemas, como un aumento de la fragilidad o una reducción de la capacidad de humectación.
Determinar el interés comercial de la soldadura a baja temperatura hoy y en el futuro
Determinar el interés comercial de las soldaduras de baja temperatura (BT) implica evaluar factores inmediatos y a largo plazo en la fabricación de productos electrónicos. Las consideraciones clave incluyen la comparación de costes entre las soldaduras a baja temperatura y las tradicionales, teniendo en cuenta el ahorro potencial a largo plazo derivado de la reducción del consumo de energía y la posibilidad de utilizar componentes más baratos. La compatibilidad de la soldadura LT con las líneas de fabricación existentes, junto con la necesidad de modificar los equipos, constituye una parte fundamental de esta evaluación.
Es esencial tener en cuenta los requisitos específicos del producto, en particular para los componentes sensibles a la temperatura, y la fiabilidad y el rendimiento de la soldadura LT en diversas condiciones. Además, las ventajas medioambientales y el cumplimiento de la normativa, en línea con las tendencias mundiales de sostenibilidad, desempeñan un papel importante en esta evaluación.
También son importantes las perspectivas de futuro, como la tendencia a la miniaturización de los dispositivos electrónicos y los cambios del mercado hacia procesos de fabricación más respetuosos con el medio ambiente. Por tanto, la rentabilidad de la soldadura LT depende de un equilibrio entre las necesidades operativas inmediatas, los beneficios a largo plazo y la adaptación a la evolución de las tendencias industriales y las demandas de los consumidores.
La importancia de la colaboración industrial
El camino a seguir exige un esfuerzo concertado de investigación en colaboración, combinando los conocimientos del mundo académico, la fabricación y la tecnología de soldadura para explorar áreas como el consumo de energía, las interacciones de los materiales y otras. El establecimiento de plataformas abiertas para el intercambio de conocimientos, junto con el fortalecimiento de los lazos entre la industria y el mundo académico, será crucial para abordar los problemas sin resolver y fomentar la innovación. Este enfoque colaborativo promete liberar todo el potencial de la soldadura LT en la fabricación de productos electrónicos, convirtiendo los retos en peldaños para el avance y la eficiencia en este campo en evolución.
CONCLUSIÓN
Nuestro examen exhaustivo de la soldadura a baja temperatura (BT) en el ensamblaje y reprocesado de componentes electrónicos ha puesto de relieve su complejo papel en la fabricación moderna. El análisis comparativo de diversas estrategias de retrabajo reveló diferencias matizadas en términos de calidad de la unión, crecimiento de IMC y tiempo de proceso, arrojando luz sobre las mejores prácticas adaptadas a objetivos de fabricación específicos. En resumen, se formaron mejores uniones retrabajadas utilizando temperaturas de punta de hierro más altas y tiempos de contacto moderados. Además, pudimos confirmar que los residuos de óxido de bismuto resultantes de la reelaboración o el reflujo de soldaduras con contenido de bismuto a baja temperatura se podían limpiar en caso de que plantearan un problema.
En última instancia, llegamos a la conclusión de que, si bien la soldadura LT presenta muchas ventajas en la soldadura por reflujo, no hay muchas razones para utilizar la soldadura LT en la reelaboración debido a la complejidad, el coste y la relativa falta de ventajas con respecto a la reelaboración con SAC. Además, hasta que nuevos descubrimientos produzcan aleaciones LT más fiables, observamos inconvenientes asociados a la fragilidad y a los fallos por impacto de caída que deben sopesarse con el ahorro de energía y costes de la soldadura LT, lo que apunta a que la electrónica consumible es quizá el mejor caso de uso actual.
De cara al futuro, el desarrollo y la adopción generalizada de la soldadura LT dependerán de que se aborden los retos mediante la innovación colaborativa, la investigación continua y la adaptación a los nuevos requisitos de la industria. El viaje a través de las complejidades de la soldadura LT sugiere un camino de aprendizaje y adaptación continuos, en el que la colaboración de la industria puede aprovechar su potencial para satisfacer las crecientes demandas de la fabricación electrónica.
REFERENCIAS
[1] Tang, K. K., Aspandiar, R. F., Mokler, S., Chen, O., & Jiang, A. (2015). SMT Soldering with Low Temperature Solder Paste (Soldadura SMT con pasta de soldadura a baja temperatura). Intel Corporation.
[2] Mei, Zequn & Hua, Fay & Glazer, J. & Chung, C. Key. (1997). Soldadura a baja temperatura. Circuit World. 10. 463 - 476. 10.1109/IEMT.1997.626966.
[3] Intel. (2017). Introducción a la soldadura a baja temperatura (LTS). Intel Corporation. Copyright 2017.
[4] Coyle, R., Anselm, M., Hadian, F., Kempaiah, S., Raj, A., Popowich, R., Clark, L., Fullerton, J., & Johnson, C. (2021, 1 de noviembre). The Effect of Peak Reflow Temperature on Thermal Cycling Performance and Failure Mode of Hybrid Low Temperature Solder Joints. SMTA International 2021, 1 de noviembre de 2021
[5] Dušek, K. & Bušek, David & Veselý, Petr & Pražanová, Anna & Plaček, Martin & Re, Julia. (2022). Understanding the Effect of Reflow Profile on the Metallurgical Properties of Tin-Bismuth Solders. Metals. 12. 121. 10.3390/met12010121.
[6] Sloan, M., Flanagan, K., Sandy-Smith, B., Allen, M. B. (2018). Perfiles de reflujo para aleaciones de soldadura de próxima generación. Indium Corporation. Clinton, NY, Estados Unidos.
[7] O'Neill, T., Fijalkowski, J., Tafoya, C., Xu, Y., Hrcek, S., Lambert, L., Willis, B., Hamasha, S. (Año). Cómo abordar los problemas del retrabajo a baja temperatura. AIM Solder. Montreal, Quebec, Canadá.
[8] Fu, Haley & Aspandiar, Raiyomand & Chen, Jimmy & Cheng, Shunfeng & Chen, Qin & Coyle, Richard & Feng, Sophia & Hardin, Bill & Krmpotich, Mark & Mokler, Scott & Radhakrishnan, Jagadeesh & Ribas, Morgana & Sandy-Smith, Brook & Tang, Kok & Wu, Greg & Zhang, Anny & Zhen, Wilson. (2018). Proyecto iNEMI sobre desarrollo de procesos de pastas de soldadura a baja temperatura basadas en BISN - Parte II: Caracterización de uniones de soldadura BGA de aleación mixta. 1-17. 10.23919/PanPacific.2018.8318989.
[9] iNEMI. (2019). Informe resumido de la encuesta iNEMI: Low Temperature Solder (LTS) Readiness for Volume Board Assembly. Publicado en mayo de 2019.
AUTORIZADO POR
Timothy O'Neill, Gayle Towell
AIM Solder
Cranston, Rhode Island, Estados Unidos
Elizabeth Norwood
MicroCare
New Britain, Connecticut, EE.UU.
Hoa Nguyen
Metcal
Cypress, California, EE.UU.
*PRESENTADO EN IPC APEX 2024
AGRADECIMIENTOS
Los autores desean agradecer a Yanci Gómez, técnico de I+D de AIM Solder, y a Itzayana López, química de I+D de AIM Solder, su ayuda en el análisis transversal.