La pasta de soldar, esa sustancia gris que se presenta en tarros, cartuchos o jeringuillas, se aplica a las placas de circuitos para unir componentes y crear conexiones eléctricas. Se suministra con instrucciones de almacenamiento y manipulación. Requiere refrigeración. No se puede dejar abierto demasiado tiempo, o se estropea. Hay que ajustar cuidadosamente los parámetros del proceso para optimizar su rendimiento.
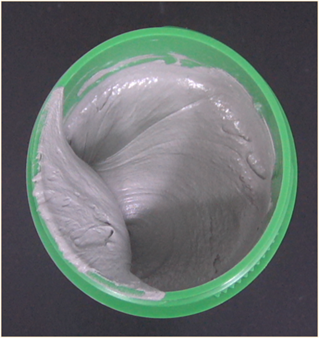
Pero, ¿por qué? ¿De qué está hecha esta sustancia gris? ¿Cómo se fabrica?
Fundamentos de la pasta de soldadura
La pasta de soldar está hecha de polvo de soldadura -pequeñas esferas de metal aleado- combinado con un medio fundente -colofonias, resinas y otros productos químicos diseñados para favorecer la limpieza y evitar la oxidación-.
Por lo tanto, para hacer pasta de soldadura, primero debe crear un aleación. Luego hay que convertir esa aleación en pequeñas esferas. A continuación, se necesita un fundente con la composición química adecuada. Por último, hay que combinar las pequeñas esferas con el medio fundente en un entorno cuidadosamente controlado.
El método exacto varía de un fabricante a otro, y los detalles exactos suelen estar protegidos por derechos de propiedad intelectual. Dicho esto, podemos darle una idea general del proceso.
Aleación y atomización
Los procesos previos a la atomización incluyen la aleación, el ensayado y la fundición del metal que se introducirá en el atomizador. Un método de atomización consiste en verter un chorro controlado de soldadura fundida sobre un disco giratorio.
A medida que el líquido golpea el disco, se desvía en gotitas que se forman por tensión superficial en esferas individuales antes de congelarse, como se muestra en el diagrama siguiente. Los parámetros de atomización incluyen la temperatura de fusión, la velocidad del disco, el entorno de la cámara y otras variables que influyen en las características clave de las partículas, como el tamaño, la forma y el nivel de óxido.
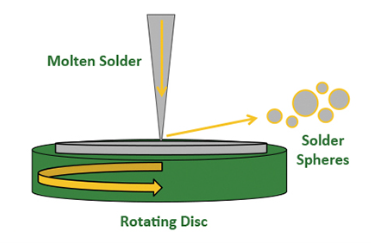
Las operaciones de atomización suelen optimizarse para producir un tamaño de polvo determinado, y las esferas fuera del rango deseado se consideran subproductos del proceso. Las formas esféricas son ideales, pero a veces se forman formas irregulares como huesos de perro o colas, o se agrupan varias esferas. Estas geometrías no deseadas pueden afectar a la reología de la pasta de soldadura y al rendimiento de la impresión, y se eliminan en el procesamiento posterior.
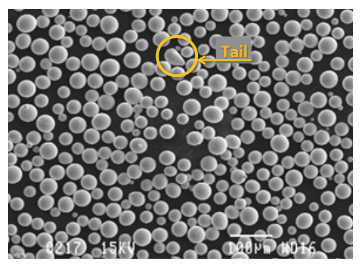
La oxidación se controla manipulando los niveles de gases inertes en el entorno de atomización.
Pasta de Soldadura en Polvo Tamaños/Tipos
Las pastas de soldadura se clasifican en función del tamaño del polvo de soldadura (pequeñas esferas) que contienen. Los tamaños de polvo van del Tipo 1 al Tipo 10, siendo los Tipos 3-6 los más utilizados actualmente en la fabricación de productos electrónicos. El Tipo 4 es el tamaño más popular en la actualidad, con un rango de tamaño de partícula de 20-38 µm. Es capaz de imprimir 0201s y microBGAs.
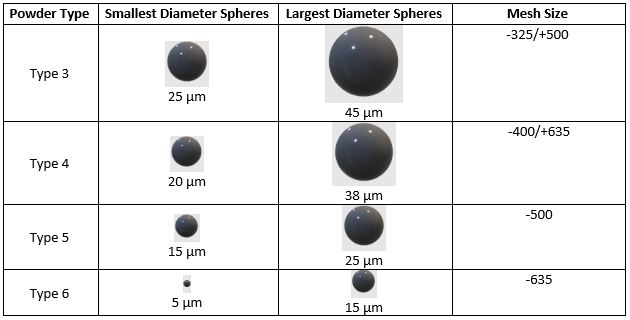
¿Qué tamaño tiene? Como referencia, el grosor de un cabello humano es de unas 100 µm y el diámetro de un glóbulo blanco es de unas 10-20 µm. Así que estas partículas son muy pequeñas.
El polvo de tipo 5, con partículas de 15-25 µm, es adecuado para aplicaciones más finas como QFN y dispositivos 01005. Tipos 6 y menores aventurarse en la ultraminiaturización, necesaria para las tecnologías de vanguardia.
Clasificación y distribución del tamaño del polvo
Tras la atomización, el polvo se refina y se clasifica por tamaños. Los métodos para hacerlo incluyen la clasificación por aire y el tamizado.
El proceso de clasificación por aire separa el polvo de soldadura en distintas clases en función de su masa. El polvo se sopla a través de una corriente de gas en la que se concentran las partículas del tamaño deseado. Las partículas más pequeñas son arrastradas por el flujo de gas y las más pesadas caen en una zona de recogida.
Este proceso permite aventar rápidamente el polvo hasta donde se concentran las partículas de tamaño más deseable. La clasificación por aire hace que la posterior operación de tamizado sea mucho más eficiente y eficaz.
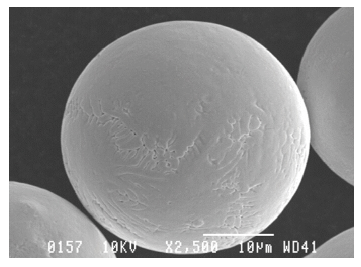
El cribado clasifica el polvo mediante grandes tamices vibratorios con cribas cada vez más finas. Los tamices se correlacionan con el tamaño de malla que define el "tipo" de polvo designado por JEDEC y J-STD-005. La tabla de la sección anterior muestra las clasificaciones, tanto en términos de tamaño de malla de los tamices como de tamaño de las partículas resultantes.
Las esferas clasificadas como Tipo 3, o T3, caerán a través de un tamiz de 325 mallas pero no a través de uno de 500 mallas, de ahí el término -325/+500. Esto equivale a tamaños de partícula de 25 a 45µm. Esto equivale a tamaños de partícula de 25 a 45µm; 80% de las partículas deben cumplir este requisito de tamaño. Del mismo modo, la pasta de tipo 4 pasará por un tamiz de 400 mallas, pero no por uno de 635, lo que equivale a un tamaño de partícula de 20 a 38 µm.
Existe un solapamiento de tamaño entre las clases T3 y T4; por lo tanto, la pasta de soldadura T4 puede ofrecer normalmente una ligera ventaja en la impresión de características finas sin introducir problemas de reflujo.
Sin embargo, el tamaño de las partículas disminuye rápidamente en el Tipo 5 a 10 µm a 25 µm, y aunque la capacidad de impresión de características finas de la pasta de soldadura mejora drásticamente, los efectos de los óxidos superficiales pueden empezar a influir; la vida útil puede verse afectada, y aumentan las posibilidades de problemas de coalescencia por reflujo.
Fundente para pasta de soldadura
El fundente es un agente químico que facilita la soldadura limpiando las superficies metálicas, mejorando el flujo de la soldadura y evitando la oxidación durante el proceso de reflujo.
El fundente utilizado en la pasta de soldadura es una combinación de varios productos químicos, como activadores, modificadores reológicos, disolventes y plastificantes. La composición específica del fundente depende de la aplicación prevista y de las propiedades requeridas, como la temperatura de activación, la viscosidad y los requisitos de limpieza.
El paso final: Combinar el polvo con el fundente
El último paso en la fabricación de pasta de soldadura consiste en combinar polvo de aleación de soldadura y fundente en proporciones específicas para garantizar que la pasta sea uniforme y homogénea. La proporción típica es de aproximadamente 50/50 de fundente y aleación en volumen o 10/90 en peso, pero puede variar en función de los requisitos específicos de la aplicación.
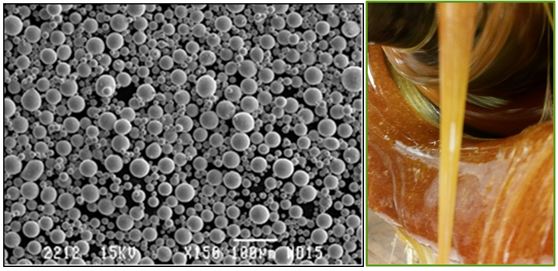
Los fabricantes de pasta de soldadura utilizan procesos de mezcla patentados con mezcladores cuidadosamente calibrados para garantizar temperaturas estables y una mezcla homogénea. Cada parte del proceso se mide, supervisa y mantiene cuidadosamente de un lote a otro, garantizando que la pasta producida sea uniforme y cumpla todas las especificaciones requeridas.
Una vez mezclada, la pasta se envasa en tarros, cartuchos o jeringuillas, en función de cómo se vaya a aplicar a las placas de circuitos.
A continuación, el producto final se somete a rigurosas pruebas para garantizar que cumple todas las normas pertinentes. Esto incluye pruebas de viscosidad, asentamiento, formación de bolas de soldadura, humectación y vida útil, entre otras.
Hemos mencionado mucho la oxidación. ¿De qué se trata?
La oxidación es un proceso químico natural que se produce entre las sustancias y el oxígeno del aire. La oxidación está presente en todas partes: es lo que hace que las manzanas en rodajas se vuelvan marrones cuando se dejan reposar, o lo que hace que se forme óxido en un coche viejo. También ocurre cuando el metal de una aleación de soldadura entra en contacto con el aire.
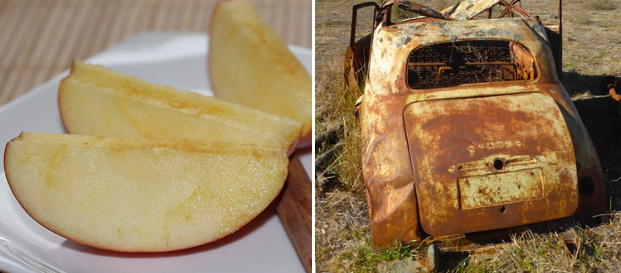
Cuanto más contacto tenga una aleación de soldadura con el aire, más propensa será a la oxidación. La oxidación también puede acelerarse por la humedad, las temperaturas más cálidas y el calentamiento. Cuando las aleaciones de soldadura reaccionan con el oxígeno, forman una capa de óxido en su superficie. Esta capa de óxido es menos conductora y menos estable mecánicamente que la aleación pura, lo que dificulta la formación de buenas conexiones eléctricas.
Por ello, uno de los principales objetivos a la hora de crear y utilizar pasta de soldadura es minimizar la oxidación en la medida de lo posible. De hecho, una de las principales funciones del fundente es eliminar los óxidos y evitar la oxidación. Lo hace mediante interacciones químicas y creando una barrera entre el metal y el aire.
Esta propensión de los metales a reaccionar con el oxígeno es la razón por la que la pasta de soldadura requiere una manipulación y un almacenamiento cuidadosos. También es la razón por la que el proceso de fabricación de la pasta debe controlarse cuidadosamente. A menudo, la formación de polvo se produce en un entorno en el que el oxígeno se ha sustituido por nitrógeno, un gas que no reacciona con el metal.
La propensión a la oxidación es la razón por la que algunos fabricantes utilizan atmósferas de nitrógeno durante el reflujo. Y también es la razón por la que las pastas de soldadura más finas son más delicadas: cuando el tamaño del polvo es menor, hay una mayor relación entre superficie y masa metálica. Dado que la oxidación se produce en la superficie, más superficie significa más posibilidades de oxidación.
Palabras finales
Ahí lo tienes. La sustancia viscosa gris se fabrica creando diminutas esferas de aleación metálica y combinándolas con una pasta química optimizada para mitigar la oxidación y promover fuertes conexiones eléctricas. La oxidación es el enemigo tanto del proceso como del producto final, y es la razón de las instrucciones de almacenamiento y manipulación.