por Kevin Pigeon
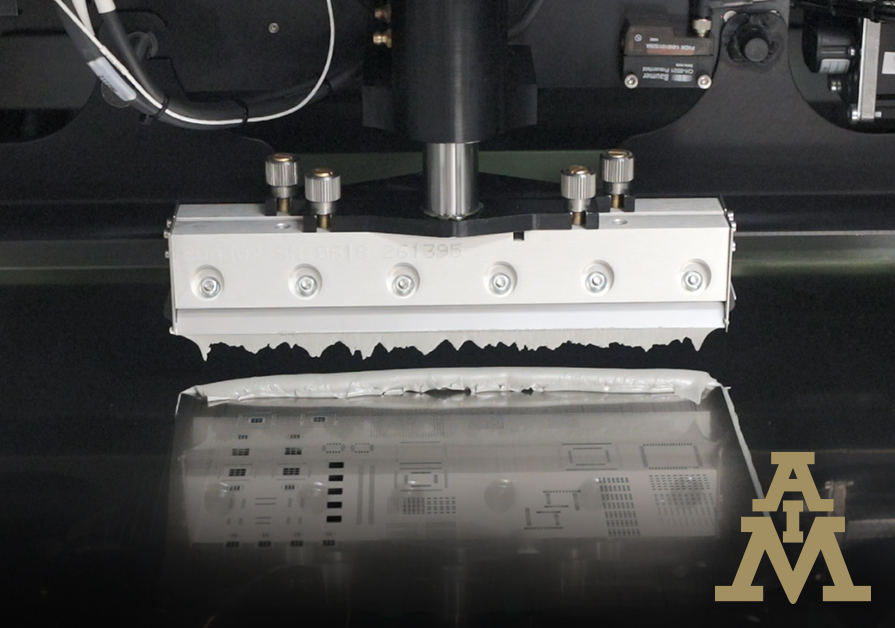
Comprender y controlar la ventana del proceso de montaje no consiste sólo en gestionar la pasta de soldadura. Se trata de dominar todas las variables del proceso a lo largo de todo el proceso de montaje SMT para obtener resultados óptimos.
Definición de la ventana Proceso de montaje
La ventana del proceso de montaje define el rango de parámetros dentro del cual soldadura en pasta cumpla los estándares óptimos de rendimiento. Salirse de este margen puede dar lugar a defectos, repeticiones e incoherencias que afectan a la eficacia y el rendimiento del proceso de fabricación de productos electrónicos.
Estos parámetros pueden incluir rangos aceptables para cosas como las siguientes:
- Tiempo total del perfil de reflujo desde el ambiente hasta el pico
- Temperatura máxima del horno de reflujo
- Tiempo por encima del liquidus
- Ritmo de cambio de temperatura
- Presión de la escobilla de goma
- Velocidad de la escobilla de goma
- Grosor del esténcil, diseño, tamaño de apertura y revestimientos
- Precisión en la colocación de los componentes
- Volumen de soldadura
- Acabado de componentes y placas de circuito impreso
- Y más
Tenga en cuenta que el índice de ventana de proceso (PWI), una medida estadística determinada por el fundente y la aleación de la pasta de soldadura, no es suficiente por sí solo para definir la ventana de proceso de ensamblaje. También deben tenerse en cuenta todos los factores anteriores.
Factores que afectan a la ventana del proceso de montaje
Los parámetros que definen la ventana del proceso de montaje no están aislados. Más bien, interactúan de forma compleja, cada uno influyendo y siendo influido por los demás. Comprender y gestionar esta interacción no consiste sólo en mantener el equilibrio, sino en orquestar la armonía en todo el proceso de soldadura.
Componentes de PCB y material de sustrato
Las temperaturas de reflujo deben ser lo suficientemente altas como para activar el fundente y formar una unión soldada fiable, pero no tanto como para dañar los delicados componentes o los sustratos de las placas de circuito impreso. En el perfil térmico también influyen varios factores, como el tipo de horno, la velocidad del transportador y la masa térmica del conjunto.
Diseño y disposición de placas de circuito impreso
El diseño de la placa de circuito impreso, incluida la disposición de las almohadillas, los planos de tierra, las trazas y las fijaciones necesarias, determina cómo se distribuye el calor. Los materiales con diferentes propiedades térmicas se comportan de forma diferente bajo el mismo perfil térmico. Puede ser necesario ajustar el perfil de reflujo y modificar el esténcil para conseguir el equilibrio adecuado.
Diseño de plantillas
El esténcil determina la forma y el volumen de los depósitos de soldadura. La proximidad y la profundidad de las aberturas pueden afectar a la probabilidad de que se produzcan puentes u otros defectos. El hecho de que el esténcil esté o no recubierto también puede afectar a la probabilidad de que la pasta se adhiera al esténcil en lugar de desprenderse limpiamente tras la impresión. Estos factores, junto con las características de la pasta de soldadura, determinarán la gama aceptable de ajustes de impresión.
Composición de la pasta de soldadura
La pasta de soldadura es una mezcla meticulosamente diseñada compuesta por polvo de soldadura y un fundente especializado. El tamaño, la forma y la composición de la aleación metálica del polvo de soldadura determinan su comportamiento de fusión, mientras que la composición química del fundente determina su nivel de actividad y su rendimiento térmico. En la siguiente sección profundizaremos en este tema.
Composición de la pasta de soldadura y su impacto en detalle
La aleación de la soldadura determina la resistencia mecánica y las propiedades eléctricas de la unión soldada resultante. Los tamaños de polvo más pequeños suelen mejorar la capacidad de impresión, lo que permite aplicaciones de paso más fino, pero también pueden aumentar el riesgo de oxidación, formación de puentes y anulación.
El medio fundente se encarga de eliminar los óxidos de las superficies metálicas, proteger la zona de soldadura de una mayor oxidación y mejorar el proceso de humectación. La composición del medio fundente influye en el nivel de actividad, la viscosidad, las características de asentamiento y las propiedades de los residuos de un determinado tipo de pasta de soldadura. Los fabricantes deben tener en cuenta:
- Fiabilidad: La composición de la aleación del polvo de soldadura, combinada con la acción protectora del fundente, contribuye a la fiabilidad a largo plazo de las conexiones soldadas.
- Imprimibilidad: En esta propiedad influyen las características físicas del polvo de soldadura y la reología del medio fundente. Imprimibilidad óptima garantiza volúmenes de deposición constantes (medidos mediante inspección de pasta de soldadura (SPI)), lo que resulta crucial para minimizar los defectos en aplicaciones de paso fino.
- Rendimiento de reflujo: El fundente debe activarse a la temperatura adecuada, favoreciendo una excelente humectación y extensión de la aleación de soldadura. La pasta también debe presentar una buena coalescencia, lo que da lugar a juntas de soldadura bien formadas y sin excesivas oquedades.
- Características de los residuos: Después del reflujo, el residuo que deja el medio fundente puede afectar al rendimiento y a la estética de la placa de circuito impreso. Los fundentes no corrosivos y sin limpieza dejan residuos mínimos y benignos, mientras que los fundentes solubles en agua y a base de colofonia requieren un paso de limpieza.
- Cumplimiento de la normativa medioambiental: Las pastas de soldadura deben cumplir la normativa medioambiental. La mayoría de las aplicaciones exigen aleaciones sin plomo, y algunas especifican ahora que los fundentes no contengan halógenos.
- Operativa: Tenga en cuenta la vida útil, los requisitos de almacenamiento, la ventana de humedad y la pegajosidad. Todos estos factores determinarán la facilidad de uso del producto para su aplicación.
Pero esto no es más que una pequeña fracción del panorama total. Puede haber docenas de consideraciones adicionales, incluidos criterios específicos del cliente, que requieren un equilibrio justo.
El gráfico de radar de la Figura 1 da una idea de cómo se pueden comparar dos tipos de flujo diferentes en función de estos factores, lo que permite priorizar unas características sobre otras para una aplicación concreta.
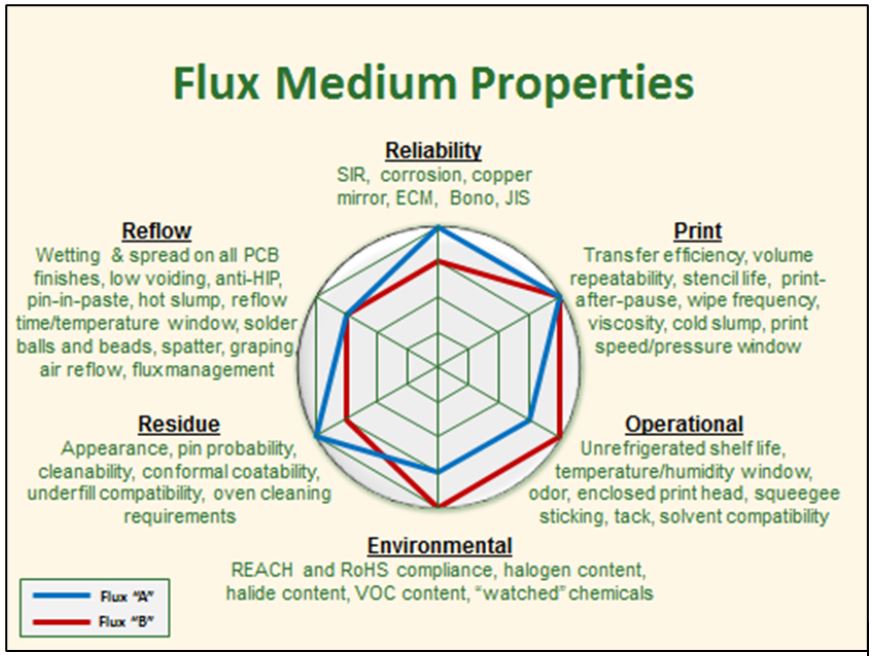
Figura 1 Gráfico de radar de las propiedades del medio de flujo
Cumplir los plazos del proceso de montaje
La elección del sustrato, los componentes, la pasta de soldadura, el esténcil y otros factores determinan la amplitud o estrechez de una ventana de proceso de montaje concreta. Aunque a menudo es una buena idea tomar decisiones que mantengan esa ventana lo más amplia posible para tener en cuenta las variaciones, esto también debe equilibrarse con las limitaciones de la aplicación. A continuación se indican los pasos a seguir para lograr este equilibrio crucial:
- Desarrollar una comprensión global de los requisitos: Esto incluye la naturaleza de los componentes, los tipos de materiales de PCB implicados y las condiciones ambientales en las que funcionará el conjunto.
- Considere las opciones de aleación de soldadura: El punto de fusión de la soldadura debe coincidir con los límites de los componentes y el sustrato. Esto incluye tener en cuenta el calentamiento adicional que puede ser necesario para las regiones de alta masa térmica.
- Considere las opciones de medio fundente: Un fundente bien equilibrado puede influir significativamente en el comportamiento de humectación y en la integridad de las juntas de soldadura. Tenga en cuenta el nivel de actividad, las características de los residuos y la fiabilidad electroquímica del fundente.
- Seleccione la pasta de soldadura adecuada: Después de considerar la aleación y el medio fundente por separado, es importante profundizar un poco más y asegurarse de que la pasta de soldadura resultante es conocida por su consistencia y fiabilidad. Las variaciones en la composición de la pasta pueden dar lugar a una amplia gama de problemas de montaje, por lo que es crucial elegir productos de fabricantes de renombre conocidos por mantener altos estándares.
- Evaluar el rendimiento de la pasta de soldadura: Dado que la interacción final de la pasta con el proceso puede dar lugar a resultados imprevistos, es importante evaluar el rendimiento de la pasta en su entorno de producción. Mida el volumen de los depósitos de pasta de soldadura, evalúe el porcentaje de anulación y busque otros defectos después del reflujo. También debe examinar cualquier residuo dejado por el fundente para asegurarse de que cumple las especificaciones y puede limpiarse si es necesario.
- Ajústelo según sea necesario: Por último, ajuste los parámetros del proceso hasta obtener los resultados deseados.
Reflexiones finales
Dominar la ventana del proceso de ensamblaje ayuda a optimizar las aplicaciones de pasta de soldadura. Al comprender la interacción entre las propiedades de la pasta y el entorno de montaje en general, los profesionales pueden mejorar la flexibilidad, reducir los defectos y mantener un alto nivel de eficiencia y fiabilidad.
Publicado originalmente en Asamblea de Circuitos, 27 de junio de 2024.