von Timothy O'Neill und Logan Jelinske
Abstrakt
Trotz der Vorhersagen über den Niedergang von Durchgangslochkomponenten sind sie in der gesamten Industrie nach wie vor üblich. Ihre Verwendung ist jedoch rückläufig, und die Baugruppen enthalten möglicherweise nur noch ein oder zwei durchkontaktierte Bauteile. Eine alternative Technik zum Löten von Bauteilen mit Durchgangslöchern, die einen separaten Lötprozess überflüssig macht, ist das Pin-in-Paste- (PiP) oder Intrusive-Reflow-Verfahren. PiP nutzt den Lotpastendruck und das SMT-Reflow-Verfahren zum Löten von Bauteilen mit Durchgangslöchern. Das PiP-Verfahren kann kosteneffizienter sein, da die Notwendigkeit eines Wellen- oder Selektivlötprozesses und die damit verbundenen Kosten entfallen. In diesem Beitrag wird das PiP-Verfahren detailliert beschrieben, einschließlich Überlegungen zum Leiterplatten- und Schablonendesign sowie zur Auswahl der Lötpaste und zu Reflow-Richtlinien.
Hintergrund
Da elektronische Geräte immer kleiner und leistungsfähiger werden, werden Bauteile mit Durchgangslöchern immer seltener eingesetzt, da der Platzmangel moderner Geräte die treibende Kraft ist. Dennoch bieten durchkontaktierte Bauteile Leistungsvorteile gegenüber SMT, da sie robuste Verbindungen mit nachgiebigen Leitungen aufweisen, die die mechanische und elektrische Zuverlässigkeit erhöhen. Das PiP-Löten kann bei der SMT-Bestückung eine gleichwertige Prozess- und Produktleistung wie das Wellen-, Selektiv- und Handlöten bieten und so die Kosten senken. Der Betrieb einer Wellen- oder Selektivlötmaschine kann kostspielig sein und der zusätzliche Prozessschritt kann entfallen. PiP kann auch den Bedarf an nicht ausgelasteten Geräten eliminieren und den Platz in der Produktion vergrößern.
PiP-Überlegungen
Für die PiP-Implementierung mit durchkontaktierten Bauteilen sind folgende Punkte zu beachten:
- Es wird geprüft, ob die Bauteile den Temperaturen des SMT-Prozesses standhalten, und die Bestückungsmethode festgelegt. Nachdem die Lötpaste gedruckt wurde, können die Bauteile entweder manuell oder automatisch eingesetzt werden.
- Das Bauteil muss einen ausreichenden Abstand haben, um zu verhindern, dass das Lötzinn mit der Unterseite des Bauteils in Berührung kommt, was einen Fehler gemäß IPC-610G 7.3.5 darstellt.
- Das Verhältnis von Blei zu Loch muss so eng wie möglich sein. Ein großes Blei-Loch-Verhältnis führt zu einer Erhöhung des Pastenvolumens, zu Lunkerbildung und zur Gefahr, dass das Lot während des Reflows aus dem Durchgangsloch fließt. Ein zu enges Blei-Loch-Verhältnis führt zu einer unzureichenden Füllung der Hülse und zu Problemen beim Einsetzen.
- Die Leitungslänge sollte so kurz wie möglich gehalten werden. Überschüssige Leitungslänge verdrängt die Paste beim Einsetzen und kann das Lot von der Hülse wegziehen, was den Bedarf an Lotvolumen erhöht.
Die Anforderungen an das Pastenvolumen zur Erzielung einer angemessenen Fassfüllung müssen mit den SMT-Anforderungen zur Vermeidung von Überbrückungen/Shorts usw. in Einklang gebracht werden. Das Aufbringen von Lotpaste auf die Maske/den Überdruck ist eine anerkannte Technik zur Erhöhung des Pastenvolumens, die jedoch durch die Abstände zwischen den Bauteilen und andere Merkmale der Leiterplatte begrenzt ist. Darüber hinaus kann sich die Diversifizierung der Legierungsoptionen auf die Benetzungskraft und den Rückzug auswirken/verringern, die erforderlich sind, damit das Überdrucken effektiv ist.
Stufenschablonen können eingesetzt werden, um eine angemessene Zylinderfüllung zu erreichen, ohne andere Lötstellen zu beeinträchtigen. Fortschritte bei den Mikroschweißtechniken für Lötschablonen haben viele der mit früheren Technologien verbundenen Unstimmigkeiten beseitigt. Eine neuere Entwicklung ist das Aufspritzen von Lötpaste, das ein berührungsloses Mittel zur Erhöhung des lokalen Pastenvolumens darstellt. Auch Lötvorformen können zur Erhöhung des Lotvolumens eingesetzt werden.
Geringfügige Prozessanpassungen können vorgenommen werden, um die Zylinderfüllung zu erhöhen, indem mit den Druckereinstellungen experimentiert wird, z. B. durch berührungsloses Drucken, Manipulation von Rakelgeschwindigkeit, Druck, Anstellwinkel und Hubzahl.
Berechnung des Lötstellenvolumens
Das erforderliche Lötstellenvolumen, Vserrechnet sich aus der Differenz zwischen dem Volumen des Durchgangslochs und dem Volumen des Stifts. Die Formel lautet:
Volumen der Lötstelle = Volumen der Durchgangsbohrung - Volumen des Stifts + (2 x Volumen der Lötfahne)
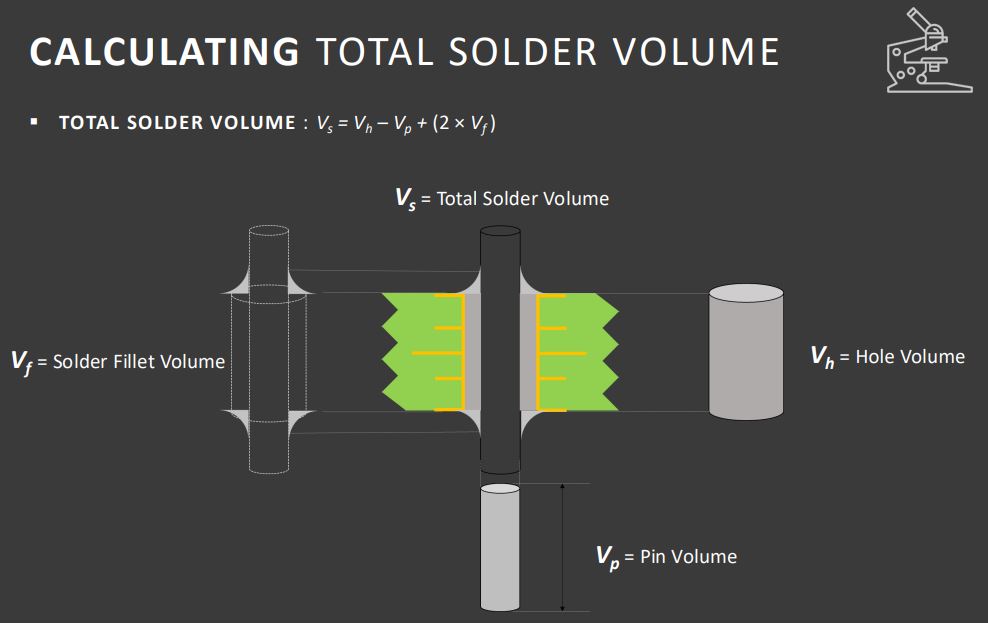
Diese Formel berücksichtigt die Lotmenge, die benötigt wird, um eine ordnungsgemäße Füllung des Durchgangslochs zu gewährleisten. Für das Volumen des Durchgangslochs, Vh:
Vh = πRo2H
Wo Ro ist der Radius des Durchgangslochs und H ist die Höhe des Durchgangslochs oder die Dicke der Leiterplatte. Das Volumen der Lötfahne, Vfkann mit der folgenden Formel berechnet werden, die aus dem Pappus'schen Schwerpunktsatz abgeleitet ist:
Vf = 2πA(0,2234R2 + Rt)
Wo Verrundungsradius, Rist gleich der Differenz zwischen dem Radius des Pads und dem Radius des Stifts (R = Rp-Rt). Filetbereich, Aist gleich 0,215R2. Berechnung des Volumens der Nadel, Vp:
Vp = πRt2H
Sobald Vh, Vfund Vp berechnet werden, reduziert sich die Formel für das Lötstellenvolumen auf die folgende:
Vs = Vh - Vp + (2 x Vf)
Da Lötpaste etwa 50% Lötmittel nach Volumen ist, ergibt sich ein Reduktionsfaktor, Fwird benötigt, um die benötigte Menge an Lotpaste zu bestimmen. Der Reduktionsfaktor liegt im Allgemeinen zwischen 0,45 und 0,55, je nach Zusammensetzung der Lotpaste. Die Formel zur Berechnung des Volumens der Lötpaste, Vspist:
Vsp = Vs/F
Schablonenöffnungen
Sobald das Volumen der Lötpaste bestimmt ist, besteht der nächste Schritt darin, die für den Prozess verwendete Schablone zu entwerfen. Für ein allgemeines kreisförmiges Öffnungsdesign, verwenden Sie:
Vsp = πr2t
Wo r ist der Radius der Blende und t ist die Dicke der Schablone. Für eine allgemeine rechteckige Apertur verwenden Sie:
Vsp = lwt
Wo l ist die Länge, w ist die Breite, und t ist die Dicke der Schablone. Passen Sie den Radius für kreisförmige Öffnungen oder die Länge und Breite für rechteckige Öffnungen rechnerisch an, um das erforderliche Volumen an Lotpaste zu erreichen, Vsp. Je nach der gewünschten Anwendung können unterschiedliche Öffnungsformen von Vorteil sein. Wie in Abbildung 2 zu sehen ist, können verschiedene Formen und Größen von Öffnungen verwendet werden, um die Leistung während des Prozesses zu erhöhen.
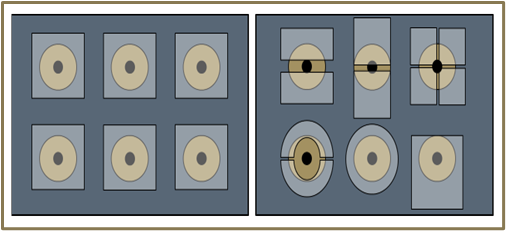
PCB-Überlegungen
Das Hauptziel eines PiP-Prozesses ist die Herstellung einer hochwertigen Lötstelle. Es gibt eine Reihe von Überlegungen zur Leiterplatte, die die Umsetzung erleichtern können.
Die Unterlage, die den Lauf umgibt, sollte so klein wie möglich sein und gleichzeitig ausreichende mechanische Eigenschaften aufweisen. In der Regel ist dies das Zweifache des Durchmessers der beschichteten Hülse. Dies hat den Vorteil, dass die erforderliche Paste zur Erfüllung der Norm IPC-610G 4.3.2.1. reduziert wird.
Eine weitere Überlegung zur Leiterplatte ist das Verhältnis von Anschlussleitung zu Bohrung. Wie bereits erwähnt, sollte dieses Verhältnis so klein wie möglich gehalten werden, aber es sollte die Toleranzen des Steckverbinders und der Leiterplatte berücksichtigen, um eine Variation der Platzierungsgenauigkeit zu ermöglichen und gleichzeitig minimale Einsteckkräfte zu erfordern.
Um das für einen PiP-Prozess erforderliche Lotvolumen zu erreichen, muss die Lotpaste auf die Lötmaske der Leiterplatte gedruckt werden (siehe Abbildung 3). Das Überdrucken der Lötmaske kann durch den Platz und die Lage auf der Leiterplatte begrenzt sein. Die Lötstoppmaske und die Oberflächenbeschaffenheit des Pads können einen erheblichen Einfluss auf das Ergebnis haben. Eine Lötstoppmaske mit hoher Oberflächenenergie hält das geschmolzene Lot flach, während Lot, das auf einer Maske mit niedriger Oberflächenenergie aufgeschmolzen wird, aufgrund des hohen Benetzungswinkels zum Abperlen neigt und das Bauteil während des Liquidus stören kann. Die Lötstoppmaske sollte auch auf freiliegendes Kupfer aufgebracht werden, um sicherzustellen, dass das geschmolzene Lot in den Zylinder fließt, und alle Durchkontaktierungen, die nicht zum Testen dienen, sollten verschlossen werden. Außerdem begünstigen leicht lötbare Oberflächenbeschichtungen wie HASL und ENIG die Benetzung und verbessern die Ergebnisse.
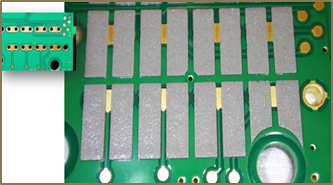
Auswahl der Lötpaste
Eine Schlüsselvariable beim PiP-Löten ist die verwendete Lotpaste. Es gibt eine Reihe von Pasteneigenschaften, die einen starken Einfluss auf den Erfolg des PiP-Lötens haben können. Einige der wichtigsten sind das Heißsinkverhalten, die Benetzungsleistung, der Legierungstyp und die Rückstandseigenschaften. Das Heißsetzverhalten von Lötpasten wird gemäß IPC TM-650 2.4.35 Sec. 5.2.2 getestet. Dieser Test quantifiziert die Fähigkeit eines Lotpastendepots, einer Verformung bei 150°C für 10-15 Minuten zu widerstehen. Dies ist eine wichtige Eigenschaft, da eine Paste, die dem Absacken widersteht, weniger wahrscheinlich aus dem Fass fällt, bevor sie flüssig wird. Lötpaste mit besseren Benetzungseigenschaften verbessert die Prozessfähigkeit und kann einige der oben genannten Probleme lösen. Flussmittelchemie und Legierung können die Benetzungsleistung beeinflussen. Wenn beispielsweise Niedrigtemperaturlegierungen untersucht werden, sollten die Auswirkungen der Benetzungseigenschaften auf die PiP-Leistung bewertet werden.
Überlegungen zum Reflow
Das Reflow-Profil der Lötpaste kann so verändert werden, dass es die Qualität der Lötstelle für die gesamte Leiterplattenbaugruppe beeinflusst, nicht nur für die PiP-Komponente. Es gibt eine Reihe von Überlegungen, wenn Profilanpassungen vorgenommen werden, um das bestmögliche Ergebnis zu erzielen. Zu den häufigsten einschränkenden Faktoren bei der Entwicklung eines Reflow-Profils gehören Empfehlungen für die Lötpaste, Temperaturbeschränkungen für die Bauteile, Eigenschaften der thermischen Masse der Baugruppe sowie Fähigkeiten und Einschränkungen des Ofens. Das verwendete Profil muss diesen Einschränkungen Rechnung tragen und gleichzeitig die Qualitätsziele der Anwendung erfüllen.
Bewertung der Qualität
Die Qualität der PiP-Lötstellen sollte die IPC-610-Kriterien für Klasse 1, 2 und 3 erfüllen. Eine zerstörungsfreie Röntgenprüfung und ein zerstörender Querschnitt können einen endgültigen Beweis dafür liefern, ob der Prozess erfolgreich ist.
Nachgelagerte Prozesse
Die Einführung eines PiP-Prozesses kann unerwartete Auswirkungen auf eine Reihe von Post-Reflow-Prozessen haben. Da Lötpaste nach Volumen 50% Flussmittel ist, kann das Hinzufügen von zusätzlicher Paste auf die Leiterplatte, um die Trommel zu füllen, die Menge der Flussmittelrückstände nach dem Löten erheblich erhöhen. Denken Sie daran, dass flüssige Flussmittel, die beim Wellen- und Selektivlöten verwendet werden, sehr wenig Rückstände hinterlassen. Erhöhte Lötpastenrückstände können eine Reihe von Problemen verursachen:
- Ästhetik - Einfach ausgedrückt: Erhöhte Flussmittelrückstände sind visuell nicht ansprechend.
- ICT - Erhöhte Flussmittelrückstände können den Kontakt der Prüfspitzen mit dem Prüfbereich beeinträchtigen, was zu "falschen Anrufen" führt. Eine verstärkte Wartung der Prüfvorrichtungen, ein Austausch der Prüfspitzen und eine Reinigung können erforderlich sein.
- Reflow-Ofen - Eine erhöhte Pastenmenge führt dazu, dass während des Reflow-Prozesses vermehrt flüchtige Flussmittel entstehen. Dies führt dazu, dass sich Flussmittelrückstände im Ofen ansammeln, was eine verstärkte Reinigung des Flussmittelmanagementsystems und ein Abtropfen des Flussmittels im Reflow-Ofen zur Folge hat. Außerdem kann Paste, die während des Bestückungsvorgangs aus dem Zylinder verdrängt wird, von der Spitze des Stifts abfallen und sich im Boden des Reflow-Ofens ansammeln.
- Flussmittelrückstände und/oder Lötpaste können auf das Ende des Steckverbinders fließen, wodurch Qualitätsstandards verletzt oder Spiel- und Toleranzgrenzen beeinträchtigt werden können.
Schlussfolgerung
Bauteile mit Durchgangslöchern sind nach wie vor weit verbreitet und es ist unwahrscheinlich, dass sie in absehbarer Zukunft abgeschafft werden. Moderne Montagebetriebe führen ständig neue Verfahren ein und optimieren bestehende Prozesse. Es ist erwiesen, dass PiP dazu beitragen kann, die Betriebskosten zu senken, den Produktionsprozess zu vereinfachen, den Platzbedarf der Montagelinie zu reduzieren und Energie zu sparen. Mit der Einführung neuer Legierungen, kleinerer Bauteile und neuer Technologien bleibt PiP eine nützliche Technik für die Leiterplattenbestückungsindustrie.