AIM ANWENDUNGSBERATUNG
Optimiert und vom Ingenieur genehmigt
Empfehlungen für die Druckeinstellung von Lotpaste
Die Druckeinstellungen sind entscheidend für einen optimalen Lotpastenauftrag. Dieser Leitfaden bietet Einblicke in wichtige Parameter wie Abriss, Trennungsabstand, Trennung, Geschwindigkeit, Druckgeschwindigkeit und Rakeldruck. Das Verständnis und die Anpassung dieser Einstellungen können die Qualität und Zuverlässigkeit des Lotpastenauftrags verbessern.
Empfohlene Snap-Off-Einstellungen: 0,00 (bei Kontakt)
Was ist Snap-Off?
Der Snap-off-Abstand bezieht sich auf den Abstand zwischen dem Substrat (Leiterplatte) und dem Sieb oder der Schablone. Die Einstellung des Snap-Off-Abstands hilft, die Lotpaste von der Schablone zu lösen und die Menge der auf dem Substrat aufgebrachten Paste zu kontrollieren.
Die Rolle von Snap-Off in der Lötanwendung
Während des Drucks übt das Rakelmesser Druck auf die Schablone aus und versiegelt den zu bedruckenden Bereich. Beim Vorbeifahren des Rakels kehrt die Schablone in den voreingestellten Abstand zurück und trennt sich von der auf dem Substrat verbliebenen Lotpaste.
Das Abreißen ist in erster Linie ein Überbleibsel aus den Tagen des Siebdrucks, obwohl es die Pastenabgabe durch eine schlecht geschnittene Schablone verbessern kann und für bestimmte Geräte oder Anwendungen immer noch notwendig sein kann.
Überlegungen zum Snap-Off-Druck
Positive Snap-off-Abstände können sich negativ auf den gewünschten "Dichtungseffekt" auswirken und zu Pastenausbreitung und Brücken zwischen den Komponentenpads führen. Snap-off kann auch zu ungleichmäßigem Pastenauftrag und uneinheitlichen Druckergebnissen führen.
Die Einstellung des Snap-Off-Abstandes auf 0,00 (Kontaktdruck) bietet Vorteile wie vollständige Abdichtung, Vermeidung von Ausbluten und Brückenbildung, selbst bei Bauteilen mit kleinem Pitch. Der Kontaktdruck führt außerdem zu einem gleichmäßigeren Pastenauftrag und einer konstanten Pastenhöhe.
Einstellen der Snap-Off-Einstellungen
Führen Sie die folgenden Schritte aus, um einen 0,00-Abdruck (bei Kontakt) zu erstellen:
- Wählen Sie einen ebenen Untergrund.
- Legen Sie das Substrat unter die Schablone.
- Senken Sie die Schablone ab oder heben Sie die Platte auf die Druckhöhe an.
- Schalten Sie das Vakuum aus, das die Platte hält.
- Stellen Sie den Schablonenabzug so ein, dass ein deutlicher Abstand zwischen Schablone und Substratoberfläche entsteht.
- Verringern Sie langsam die Absprungdistanz, indem Sie die Schablone in Richtung des Substrats auslenken, bis sie die bedruckbare Fläche gerade berührt.
- Bei manuellen Druckern arretieren Sie die Schablonenhöhe und stellen die Messuhren auf 0,00 zurück. Bei automatisierten Druckern notieren Sie den neuen Rastabstand und wiederholen Sie die Schritte 2, 3 und 6, um die Einstellung zu überprüfen.
Anmerkungen
Bei einigen computergesteuerten Geräten ist eine zusätzliche Kalibrierung für die Absprungeinstellungen erforderlich. Überprüfen Sie immer Ihre Einstellungen. Denken Sie auch daran, die gesamte Platinenfläche auf Kontakt mit der Schablone zu prüfen, insbesondere die äußeren Kanten. Überprüfen Sie die Leiterplattenauflage und stellen Sie sicher, dass sich die Leiterplatte nicht verzieht, wenn der Kontakt zu früh erfolgt.
Empfohlener Trennungsabstand: 0,010″ bis 0,050″ (0,25 bis 1,25 mm), abhängig von der Plattendicke, dem Abknicken und der Einstellung des Niederhalters.
Was ist der Trennungsabstand?
Der Trennungsabstand bezieht sich auf den Abstand, um den sich der Z-Turm bzw. der Leiterplattenträger mit kontrollierter Geschwindigkeit absenkt, um die Schablone zu entfernen, bevor er in seine Ausgangsposition zurückkehrt. Es ist wichtig, die Schablone nach dem Druck sorgfältig von der Leiterplatte zu trennen, um eine saubere Trennung der Lotpaste von den Schablonenöffnungen zu gewährleisten. Die Trennstrecke wird in der Regel mit einer bestimmten Geschwindigkeit durchfahren, um diesen Prozess zu unterstützen.
Die Rolle des Trennungsabstands bei der Lotanwendung
Sobald der Druckzyklus abgeschlossen ist, senkt sich der Z-Turm, der das bedruckte Substrat hält, mit einer bestimmten Geschwindigkeit auf den eingestellten Trennungsabstand ab. Nach Erreichen dieses Abstands senkt sich der Z-Turm mit voller Geschwindigkeit in seine Ausgangsposition. Die durch die langsame Motordrehung verursachten Vibrationen in einigen Leiterplattenträgern tragen ebenfalls zur Freisetzung der Lotpaste bei.
Überlegungen zum Trennungsabstand
Die Einstellung eines Trennungsabstands fördert eine bessere Freisetzung der Lotpaste aus den Schablonenöffnungen. Er trägt auch zu gleichmäßigeren Lotpastenablagerungen bei und minimiert die Spitzenbildung. Obwohl die Verwendung eines Trennungsabstands die Gesamtdruckzykluszeit verlangsamt, ist die Auswirkung auf die Produktionszeit bei kleinen Trennungsabständen oder schnelleren Trennungsgeschwindigkeiten minimal, wird aber bei Annäherung an die Grenzwerte bedeutender.
Einstellen des Trennungsabstands
Beginnen Sie damit, den Trennungsabstand im Setup-Menü auf 0,005" (0,125 mm) mehr als die Schablonendicke einzustellen. Wenn die Schablonendicke zum Beispiel 0,006″ (0,15 mm) beträgt, stellen Sie den Anfangsabstand auf 0,011″ (0,28 mm). Führen Sie dann die folgenden Schritte aus:
- Senken Sie die Schablone ab oder heben Sie die Platte auf die Druckhöhe an.
- Vergewissern Sie sich, dass das Vakuum, das die Platte hält, ausgeschaltet ist.
- Stellen Sie den Abstand schrittweise ein und achten Sie dabei auf den richtigen Abstand zwischen Schablone und Substrat.
- Überprüfen Sie den Abstand, indem Sie drucken und den Lotpastenauftrag kontrollieren.
Anmerkungen: Eine Feinabstimmung des Trennungsabstands kann je nach Ausrüstung oder Anforderungen erforderlich sein. Testen und validieren Sie den angepassten Trennungsabstand, um optimale Ergebnisse sicherzustellen.
Berücksichtigen Sie die Auswirkungen auf die Gesamtproduktionszeit, wenn Sie den Trennungsabstand anpassen. Finden Sie ein Gleichgewicht zwischen optimaler Pastenabgabe und effizientem Druck.
Es ist wichtig, den Trennungsabstand zu überwachen und einzuhalten, um Probleme wie das Verschmieren von Lotpaste oder unzureichende Ablösung zu vermeiden. Überprüfen und reinigen Sie die Schablone und die Ausrüstung regelmäßig, um eine einwandfreie Funktion zu gewährleisten.
Empfohlene Trennungsgeschwindigkeit: 0,010″ bis 0,020″ pro Sekunde (0,254 mm bis 0,508 mm pro Sekunde), 1-2 oder 10-20% der Achsengeschwindigkeit für Fine-Pitch- und Micro-BGA-Komponenten. Für unkritisches Drucken kann eine Geschwindigkeit von 0,030″ bis 0,050″ pro Sekunde (0,762 mm bis 1,27 mm pro Sekunde), 3-5 oder 30-50% verwendet werden.
Was ist die Trennungsgeschwindigkeit?
Die Ablösegeschwindigkeit bezieht sich auf die gemessene Geschwindigkeit, mit der sich die Rakel von der Schablone löst. Wie der Trennungsabstand dient dieser Parameter dazu, die Trennung der Lotpaste von den Schablonenöffnungen zu unterstützen. Die Ablösegeschwindigkeit kann in Tausendstel Zoll, Millimetern oder als Prozentsatz der Achsengeschwindigkeit angegeben werden.
Die Rolle der Trenngeschwindigkeit bei der Lötanwendung
Sobald der Druckzyklus abgeschlossen ist, hilft die Steuerung der Ablösegeschwindigkeit des Rakels dabei, eine saubere Ablösung der Lotpaste von den Schablonenöffnungen zu erreichen. Eine gut kontrollierte Ablösegeschwindigkeit trägt zu einem konsistenten und gleichmäßigen Pastenauftrag bei, minimiert Defekte und gewährleistet eine bessere Qualität der Lötstellen. Durch sorgfältiges Einstellen der Ablösegeschwindigkeit können Sie den Druckprozess optimieren und bessere Ergebnisse erzielen.
Überlegungen zur Trennungsgeschwindigkeit
Die Einstellung einer angemessenen Trenngeschwindigkeit ist entscheidend für einen optimalen Lotpastenauftrag. Sie hilft, Probleme wie Eselsohren, Spitzenbildung, Dochtwirkung und unzureichende Pastenabdeckung zu vermeiden. Während langsamere Abscheidegeschwindigkeiten im Allgemeinen für eine bessere Kontrolle bevorzugt werden, ist es wichtig, ein Gleichgewicht zwischen zuverlässigem Pastenauftrag und effizientem Druck zu finden. Berücksichtigen Sie Faktoren wie Bauteiltypen, Leiterplattendesigns und Lotpasteneigenschaften, wenn Sie die geeignete Separationsgeschwindigkeit für Ihre Anwendung bestimmen.
Einstellen der Trennungsgeschwindigkeit
Gehen Sie folgendermaßen vor, um die Trenngeschwindigkeit effektiv einzustellen:
- Zugriff auf das Setup-Menü oder die Software-Einstellungen.
- Suchen Sie den Parameter für die Trenngeschwindigkeit.
- Legen Sie zunächst einen konservativen Wert fest, der auf dem empfohlenen Bereich für Ihre spezielle Anwendung basiert.
- Führen Sie einen Testdruck durch und prüfen Sie den Lotpastenauftrag auf Qualität und Konsistenz.
- Stellen Sie die Trenngeschwindigkeit schrittweise ein, wobei Sie die Leistung und die erzielten Ergebnisse berücksichtigen.
- Wiederholen Sie den Testdruck und die Inspektion, bis der gewünschte Lotpastenauftrag erreicht ist.
Anmerkungen: Eine Feinabstimmung der Abscheidegeschwindigkeit kann je nach Ausrüstung oder Anforderungen erforderlich sein. Testen und validieren Sie die angepasste Abscheidegeschwindigkeit, um optimale Ergebnisse zu erzielen.
Es ist wichtig, die Trenngeschwindigkeit zu überwachen und aufrechtzuerhalten, um Probleme wie das Verschmieren von Lotpaste oder unzureichende Ablösung zu vermeiden. Überprüfen und reinigen Sie die Schablone und die Ausrüstung regelmäßig, um eine einwandfreie Funktion zu gewährleisten.
Beim Drucken von Fine Pitch, d.h. LGA, QFN und Micro-BGA, stellen Sie die Trenngeschwindigkeit auf ein Minimum ein.
Empfohlene Druckgeschwindigkeitseinstellungen: Je nach Zusammensetzung und Viskosität der Lötpaste liegen die empfohlenen Druckgeschwindigkeiten zwischen 25 und 200 mm pro Sekunde (1 bis 8 Zoll pro Sekunde).
Was ist Druckgeschwindigkeit?
Die Druckgeschwindigkeit bezieht sich auf die Geschwindigkeit, mit der sich die Rakelanordnung während des Druckzyklus über die Schablone bewegt.
Die Rolle der Druckgeschwindigkeit bei der Lötanwendung
Die Druckgeschwindigkeit sollte in Verbindung mit anderen Parametern wie Rakeldruck, Pastenchemie, Schablonenöffnungsgröße usw. eingestellt werden. Die Anpassung der Druckgeschwindigkeit ist notwendig, um ein sauberes Abwischen der Schablonenoberfläche zu erreichen, insbesondere bei der Verwendung von hochviskoser Lotpaste bei höheren Geschwindigkeiten.
Überlegungen zur Druckgeschwindigkeit
Hochgeschwindigkeitsdruck bezieht sich in der Regel auf Geschwindigkeiten zwischen 4 und 8 Zoll pro Sekunde (100 bis 200 mm pro Sekunde). Das Erreichen einer guten Druckqualität bei hohen Geschwindigkeiten hängt von der Wahl der richtigen Lotpastenviskosität und -rheologie sowie von einem geeigneten Schablonendesign ab.
Während des Hochgeschwindigkeitsdrucks führen die Scherkräfte der Rakel zu einer vorübergehenden Viskositätsverringerung (Scherverdünnung) der Lotpasten. Höhere Geschwindigkeiten und erhöhter Rakeldruck verschlimmern die Scherverdünnung, was zu einem Kurzschluss zwischen den Pads führen kann, wenn die Paste nicht schnell wieder ihre normale Viskosität annimmt. Auch eine unzureichende Füllung der Schablonenöffnungen und eine unzureichende Padabdeckung können bei hohen Geschwindigkeiten auftreten.
Für den Hochgeschwindigkeitsdruck sind zusätzliche Druck- und Geschwindigkeitseinstellungen erforderlich, die sich auf Messwandler, Servomotoren, Rakelmesser und die Lebensdauer der Schablone auswirken können. Der Hauptvorteil des Hochgeschwindigkeitsdrucks ist die Verkürzung der Produktionszeit und die Erhöhung des Durchsatzes.
Einstellen der Druckgeschwindigkeit
Aufgrund der Vielzahl der beteiligten Variablen empfiehlt es sich, die wenden Sie sich an Ihren AIM Solder-Techniker für Hinweise zur Anpassung der Druckgeschwindigkeit.
Anmerkungen: Im Allgemeinen führt ein langsamerer Druck zu einer besseren Druckqualität, aber dies sollte mit den Produktionsanforderungen abgewogen werden. Passen Sie die Druckgeschwindigkeit an, um die Zykluszeit zu optimieren, ohne den Rest Ihrer Produktionslinie zu verlangsamen.
Ziehen Sie in Erwägung, die Druckeinstellungen auf eine bedarfsgesteuerte Zyklusrate einzustellen, um die Wartezeit zwischen den Zyklen zu minimieren. Diese Optimierung ermöglicht eine stabile Rheologie der Lotpaste und eine verbesserte Druckzykluszeit.
Wenn für Ihren Produktionsprozess hohe Druckgeschwindigkeiten erforderlich sind, stellen Sie sicher, dass Ihre Lötpaste für diese Geschwindigkeiten ausgelegt ist. Eine angemessene Unterstützung der Leiterplatte kann auch die Biegung während des Druckzyklus minimieren.
Empfohlener Rakeldruck: 0,45 bis 0,70 kg pro 25 mm (1 bis 1,5 lbs pro linearem Zoll) des Rakelmessers
Was ist Rakeldruck?
Der Rakeldruck bezieht sich auf den Druck, den das Rakelmesser während des Druckvorgangs auf die Schablonenoberfläche ausübt.
Die Rolle des Rakeldrucks beim Auftragen von Lötzinn
Während des Druckzyklus drückt die Rakel die Lotpaste über den bedruckbaren Bereich, füllt die Öffnungen und wischt die Schablonenoberfläche sauber. Ein gleichmäßig über die Klingenlänge verteilter Rakeldruck sorgt für eine konstante Pastenhöhe, eine gleichmäßige Abscheidungskontrolle und einen geringeren Verschleiß von Klinge und Schablone.
Überlegungen zum Rakeldruck
Das richtige Maß an Druck ist wichtig, um einen gleichmäßigen und zuverlässigen Lotpastenauftrag zu gewährleisten und gleichzeitig mögliche Probleme zu vermeiden. Übermäßiger Druck kann zu beschädigten Schablonen, Prägungen und zum Brechen des Gewebes zwischen den Fine-Pitch-Öffnungen führen. Diese Probleme können sich negativ auf den Druckprozess auswirken und zu einer schlechten Qualität der Lötstellen führen. Umgekehrt kann ein zu geringer Druck zu Ausrutschern führen, wenn die Schablone nicht ausreichend sauber gewischt wird. Es ist wichtig, ein Gleichgewicht zwischen ausreichendem Druck für die Schablonenfüllung und der Vermeidung von übermäßigem Druck zu finden, der Schäden verursachen kann.
Einstellen des Rakeldrucks
Gehen Sie wie folgt vor, um den richtigen Druck auf den Rollenquetscher zu ermitteln, vorausgesetzt, die Klingen sind korrekt installiert und eingestellt:
- Wählen Sie einen ebenen Untergrund.
- Legen Sie das Substrat unter die Schablone.
- Stellen Sie den Rakeldruck so ein, dass nach einem Druckzyklus überschüssiges Lot auf dem Öffnungsbereich der Schablonenoberfläche verbleibt.
- Tragen Sie Lotpaste auf die Schablone auf und führen Sie einen Druckzyklus durch.
- Beobachten Sie die Menge der auf der Schablonenoberfläche verbliebenen Lotpaste.
- Erhöhen Sie den Rakeldruck geringfügig und führen Sie einen weiteren Druckzyklus durch.
- Beobachten Sie erneut die Menge der auf der Schablonenoberfläche verbliebenen Lotpaste, die etwas geringer sein sollte als beim vorherigen Durchgang.
- Wiederholen Sie die Schritte 6 und 7, bis nur noch eine hauchdünne Schicht Lötpaste auf dem Öffnungsbereich der Schablonenoberfläche sichtbar ist.
Anmerkungen: Auch die Anpassung anderer Druckparameter, wie Druckgeschwindigkeit oder Schablonendesign, kann den erforderlichen Rakeldruck beeinflussen.
Regelmäßige Inspektion und Wartung der Rakelklingen gewährleisten optimale Leistung und gleichmäßigen Druckauftrag.
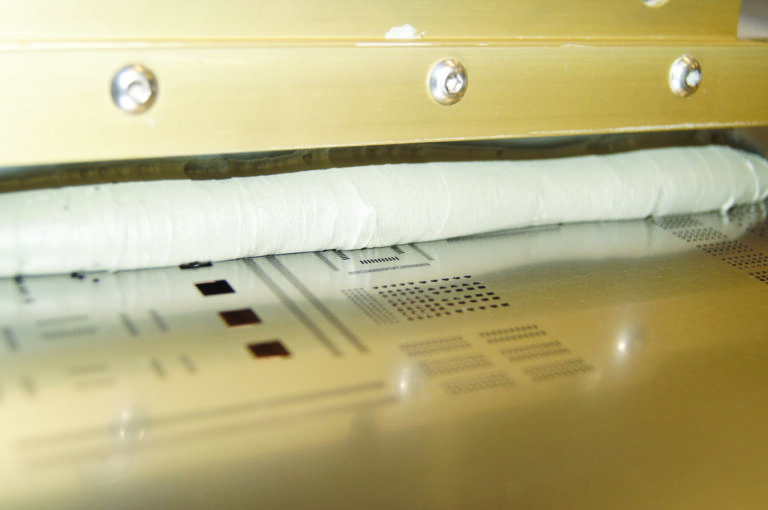