摘要
In recent years, bismuth has emerged as an advantageous alloying element in solder, serving two key applications. First, bismuth is used in many low-temperature solders that support temperature-sensitive assemblies, and second, small additions of bismuth in high-reliability solders are proving valuable in reinforcing joint durability, optimizing wetting characteristics, and minimizing voiding.
Bismuth: Properties and Comparison to Other Solder Metals
Bismuth (Bi) is a brittle, crystalline, and relatively dense metal with a silver-pink hue. It stands out, because when combined with other metals like tin, it’s overall melting point lowers due to eutectic interactions. While its elemental melting point is 271°C, bismuth-based alloys liquify below 200°C.
Compared to other metals used in soldering, bismuth is also distinct in its lower toxicity. It provides a relatively safe alternative to lead, which has been gradually phased out in many applications due to environmental and health concerns.
Another unique feature of bismuth is its tendency to expand upon solidification, a property it shares with H2O (water/ice), but with few other metals.
Bismuth’s low electrical and thermal conductivity relative to tin and silver may present challenges in certain applications, particularly those in which heat dissipation or optimal conductivity are paramount. Table 1 shows how bismuth compares with many common solder alloy elements in terms of electrical and thermal conductivity as well as melting point and density.
Element | Electrical Conductivity (%IACS) | Thermal Conductivity (W/mK) | 熔点 °C | Density g/cm3 |
Antimony | 4 | 26 | 630 | 6.69 |
铋 | 1.5 | 8 | 271 | 9.75 |
Copper | 100 | 401 | 1084 | 8.94 |
铟 | 20 | 84 | 157 | 7.31 |
领导 | 9.1 | 36 | 328 | 11.34 |
Nickel | 25 | 94 | 1453 | 8.91 |
Silver | 109 | 428 | 961 | 10.49 |
锡 | 16 | 68 | 232 | 7.28 |
表 1. A comparison of physical properties of common solder elements. [1]
Bismuth’s Place in the Evolution of Lead-Free Solder Alloys
First-generation lead-free solder alloys avoided bismuth for good reason. When bismuth comes into contact with lead, it forms a low-melting eutectic phase that can become brittle, causing fractures or joint failure under stress. This issue is particularly significant in electronics that may still encounter lead contamination from legacy processes, as even trace amounts of lead can trigger the formation of these unstable compounds.
However, with the near complete elimination of Pb in PCB assembly, later generations of lead-free solders began to incorporate bismuth for its valuable properties.
Bismuth in Low-Temperature Solder Alloys
Tin-bismuth (SnBi) alloys are widely utilized in applications requiring processing temperatures lower than those needed for traditional lead-free solders like SAC305. With a melting point as low as 138°C, SnBi alloys reduce thermal exposure during soldering, making them ideal for delicate electronics, flexible substrates, and applications where prolonged heat exposure could lead to component or substrate damage.
In addition to protecting sensitive components, the use of bismuth in low-temperature solders offers economic and environmental benefits. Lower temperature soldering processes consume less energy, potentially reducing operating costs and lowering the environmental impact of manufacturing. Furthermore, the minimal thermal impact reduces the likelihood of warpage in PCBs and other substrates.
Associated Issues
Despite these advantages, bismuth-based low-temperature solders also present certain challenges. The brittleness of bismuth can limit the mechanical strength of solder joints, making them more susceptible to cracking under mechanical stress. The risk of joint fragility is a notable concern in applications that may experience rapid temperature fluctuations or mechanical stresses, as it could lead to premature joint failure.
Because the thermal and electrical conductivities of bismuth are lower than those of tin, copper, and silver, it may also not perform well in applications requiring efficient heat dissipation or high electrical performance.
Small-Percentage Bismuth Additions in High-Reliability Solder Alloys
Bismuth’s role in solder alloys is somewhat paradoxical: when it is a main constituent in low-temperature solders, it is known to contribute to brittleness, however these concerns do not apply when it is used as a minor additive in high-reliability solder formulations.
In small percentages, typically around 1–6%, bismuth actually enhances solder performance rather than detracting from it.[2] At these low concentrations, bismuth does not lead to the brittle intermetallic compounds associated with higher bismuth content; instead, it acts to refine the alloy’s microstructure, improving properties like strength, thermal stability, and even fatigue resistance.
Figure 1 shows a comparison in grain structure between SAC305 and two bismuth-containing alloys: REL61, a low-silver alloy designed as a SAC305 replacement, and REL22, a high reliability SAC based alloy. When first cast, all three alloys have similar grain structure. But after aging at 150°C for 24 hours, SAC305 demonstrates an unstable microstructure, while both bismuth-containing alloys remain undegraded.
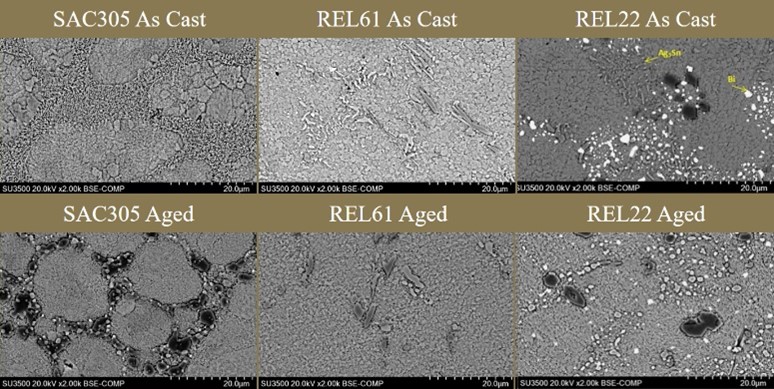
Bismuth’s low-melting-point benefit also comes into play when added in low concentrations by slightly lowering the overall melting temperature of the alloy, thus reducing thermal stress on components during soldering.
SAC-based alloys containing bismuth are now common in high-reliability applications, including automotive, aerospace, and industrial electronics, where the robustness of solder joints is paramount. In these applications, the specific benefits brought about by minor bismuth additions can lead to improved joint integrity and consistency, which are crucial for components exposed to prolonged operational stresses or demanding environmental conditions.
Influence on Solder Properties
Strength and Hardness
Small amounts of bismuth can improve the hardness of solder joints, contributing to increased resistance to mechanical deformation and thermal cycling. Bismuth forms intermetallic compounds with tin that contribute to a finer grain structure, enhancing the strength and hardness of the alloy. While SAC305 has an HV10 hardness of 14, bismuth-containing alloys REL61 and REL22 have hardnesses of 26 and 29, respectively.
Wettability and Barrel Fill
Bismuth enhances wettability, allowing molten solder to spread and bond more effectively on metal surfaces.[3] This improved fluidity promotes better barrel fill in through-hole components, as the molten alloy flows into narrow spaces more easily. Figure 2 shows how the wetting angles of two bismuth-containing alloys compare to SAC305 and SN100C. Smaller contact angles indicate better wetting.
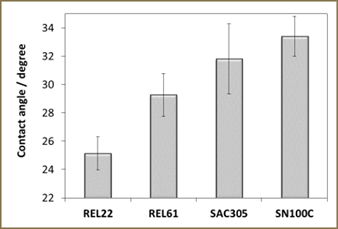
Smoothness of Joints
In a SAC alloy, additional bismuth contributes to smoother solder joints with matte finish. This characteristic improves automatic optical inspection (AOI) yields, as smoother and more consistent joints are easier to inspect and less likely to trigger false defect detections as with SAC305. Figure 3 shows images taken by a high end AOI machine, illustrating the clear difference between SAC305 and bismuth-containing REL61.
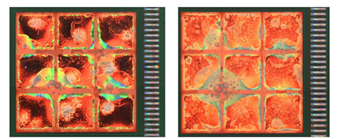
Reduction of Voiding
Adding bismuth to solder has also been shown to reduce void formation. Reduced voiding translates to improved structural integrity and electrical reliability, reducing the likelihood of weak spots that could fail under thermal or mechanical stress.[4]
Tin Whisker Mitigation
Tin whiskers are growths of tin from an alloy that may occur under different conditions such as joint strain or bending. These whiskers are problematic in electronics because they can lead to shorts. It has been observed that bismuth-containing alloys seem to mitigate the growth of these whiskers. It is not well understood why this is, but Figure 4. Shows the stark difference between tin whisker growth in SAC305 compared to bismuth-containing REL61.
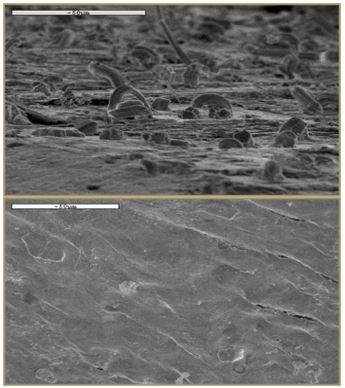
结论
Bismuth plays a multifaceted role in modern solder technology, offering benefits that address both low-temperature processing needs and high-reliability requirements. Its distinct physical and chemical properties make it uniquely suited for applications requiring reduced thermal exposure and enhanced joint reliability.
While bismuth’s reputation as a brittle metal may raise concerns, particularly in low-temperature soldering applications, when used in small amounts within high-reliability solder alloys, these drawbacks are largely eliminated, allowing bismuth’s beneficial properties to come to the forefront. At trace levels, bismuth enhances the alloy’s microstructure, contributing to improved strength, stability, and a slightly lower melting point—all while potentially improving joint reliability.
References
[1] The Engineering Toolbox. (n.d.). The Engineering Toolbox. Retrieved November 19, 2024, from https://www.engineeringtoolbox.com/
[2] H. Elhosiny Ali, A.M. El-Taher, H. Algarni, Influence of bismuth addition on the physical and mechanical properties of low silver/lead-free Sn-Ag-Cu solder, Materials Today Communications, Volume 39, 2024,109113, ISSN 2352-4928, https://doi.org/10.1016/j.mtcomm.2024.109113.
[3] M.I.I. Ramli, M.A.A. Mohd Salleh, H. Yasuda, J. Chaiprapa, K. Nogita, The effect of Bi on the microstructure, electrical, wettability and mechanical properties of Sn-0.7Cu-0.05Ni alloys for high strength soldering, Materials & Design, Volume 186, 2020, 108281, ISSN 0264-1275, https://doi.org/10.1016/j.matdes.2019.108281.
[4] Preeth Sivakumar, Kathy O’Donnell, Junghyun Cho, Effects of bismuth and nickel on the microstructure evolution of Sn-Ag-Cu (SAC)-based solders, Materials Today Communications, Volume 26, 2021, 101787, ISSN 2352-4928, https://doi.org/10.1016/j.mtcomm.2020.101787.