焊膏--装在罐子、盒装或注射器中的灰色粘稠物--被涂抹在电路板上,用于连接元件和建立电气连接。它有特定的 储存和处理说明.它需要冷藏。不能开太久,否则会变质。您必须仔细调整工艺设置,以优化其性能。
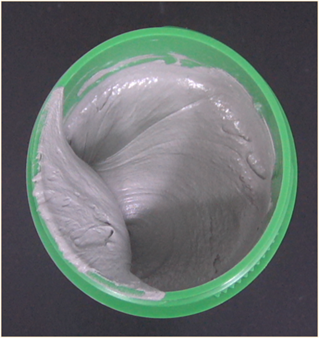
但为什么呢?这种灰色粘稠物是由什么制成的?它是如何制造出来的?
锡膏基础知识
焊膏由焊粉(合金金属的微小球体)和助焊剂介质(松香、树脂和其他用于促进清洁和防止氧化的化学物质)制成。
因此,要制作焊膏,必须首先创建一个 合金.然后,您必须将合金变成微小的球体。接着,您需要一种具有正确化学成分的助熔介质。最后,在严格控制的环境中将小球与助熔介质结合在一起。
每个制造商的具体操作方法都不尽相同,而且具体细节通常都是专有的、保密的。尽管如此,我们还是可以为您提供一个大致的过程。
合金化和雾化
雾化前工序包括对将送入雾化器的金属进行合金化、化验和铸造。一种雾化方法是将受控的熔融焊料流浇注到旋转圆盘上。
如下图所示,当液体撞击圆盘时,会偏转成液滴,这些液滴在凝固前会在表面张力作用下形成单个球体。雾化参数包括熔体温度、圆盘速度、腔室环境和其他变量,这些变量会影响颗粒的关键特性,如大小、形状和氧化物含量。
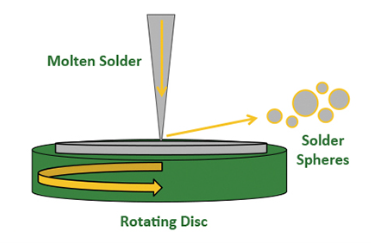
雾化操作通常经过优化,以生产特定尺寸的粉末,超出理想范围的球体被视为工艺的副产品。球形是理想的形状,但有时会形成狗骨头或尾巴等不规则形状,或者多个球体聚集在一起。这些不理想的几何形状会影响焊膏的流变性和印刷性能,需要在后续加工中去除。
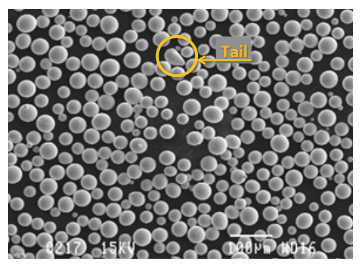
通过调节雾化环境中惰性气体的含量来控制氧化。
锡膏粉末尺寸/类型
焊膏根据其所含焊粉(小球)的尺寸范围进行分类。粉末尺寸范围从 1 型到 10 型,其中 3-6 型是目前电子制造中最常用的。4 型是目前最常用的尺寸,其粒度范围为 20-38 µm。它能够印刷 0201 和 microBGA。
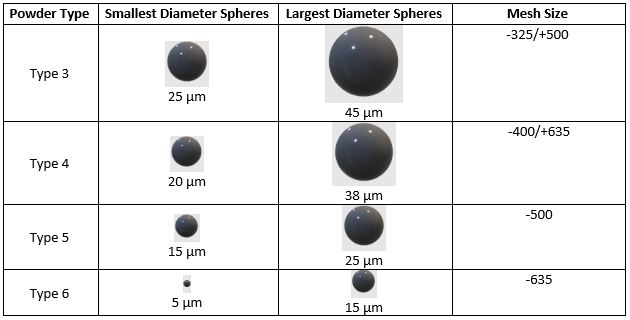
这到底有多小?作为参考,一根头发的粗细约为 100 微米,一个白细胞的直径约为 10-20 微米。因此,这些微粒确实非常小!
5 型粉末的颗粒为 15-25 µm,适合 QFN 和 01005 器件等更精细的应用。 6 型及更小 涉足尖端技术所需的超微型化领域。
粉末粒度的分类和分布
雾化后,粉末将按尺寸进行精制和分类。方法包括空气分级和筛分。
空气分级工艺根据质量将焊粉分成不同的等级。粉末被吹过一股气流,目标大小的颗粒被集中起来。较小的颗粒被流动的气体带走,较重的颗粒则落入收集区。
这种工艺可以快速筛分粉末,使最理想尺寸的颗粒高度集中。空气分级使随后的筛分操作更加高效和有效。
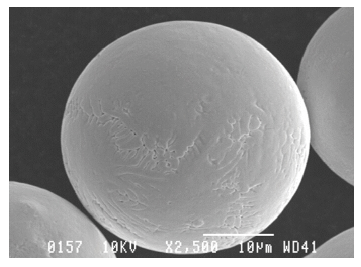
筛分使用大型振动筛对分类粉末进行分拣,振动筛的筛网逐渐变细。筛网与 JEDEC 和 J-STD-005 指定的定义粉末 "类型 "的网目尺寸相关。上一节中的表格显示了筛网网目尺寸和所得颗粒尺寸的分类。
归类为 3 类或 T3 的球体可通过 325 目筛网,但不能通过 500 目筛网,因此称为 -325/+500。这相当于粒径为 25 至 45 微米;80% 的颗粒必须符合这一粒径要求。同样,4 型浆料可通过 400 目筛网,但不能通过 635 目筛网,这相当于粒径为 20 至 38 微米。
T3 和 T4 等级之间存在尺寸重叠;因此,T4 焊膏通常在精细特征印刷方面略胜一筹,而不会带来回流焊问题。
然而,颗粒尺寸在 5 至 10 微米至 25 微米时会迅速减小,虽然焊膏的精细特征印刷能力显著提高,但表面氧化物的影响也会开始显现;保质期可能会受到影响,回流焊凝聚问题的可能性也会增加。
焊膏助焊剂
助焊剂是一种化学剂,通过清洁金属表面、提高焊料流动性和防止回流过程中的氧化作用来促进焊接。
焊膏中使用的助焊剂是各种化学品的组合,包括活化剂、流变修饰剂、溶剂和增塑剂。助焊剂的具体成分取决于预期应用和所需特性,如活化温度、粘度和清洁要求。
最后一步将粉末与助焊剂结合
制作焊膏的最后一步是将焊料合金粉和助焊剂按特定比例混合,以确保焊膏均匀一致。按体积计算,助焊剂与合金的典型比例约为 50/50,按重量计算则为 10/90,但这一比例可根据应用的具体要求而变化。
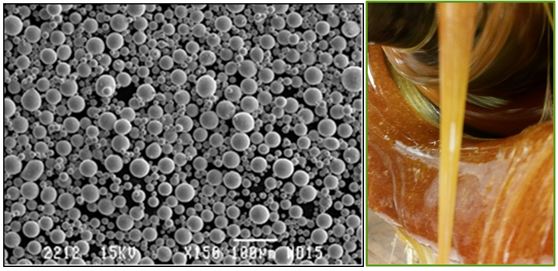
焊膏生产商使用专有的混合工艺,其中包括经过仔细校准的混合器,以确保稳定的温度和一致的混合。该工艺的每个部分都经过仔细测量和监控,并保持每批产品的一致性,以确保生产出的锡膏均匀一致,符合所有要求的规格。
混合后,根据电路板的应用方式,浆糊会被装进瓶子、盒或注射器中。
最终产品还要经过严格的测试,以确保符合所有相关标准。其中包括粘度、坍落度、焊料成球性、润湿性和保质期等测试。
我们经常提到氧化。这是怎么回事?
氧化是物质与空气中的氧气之间发生的一种自然的化学过程。氧化现象随处可见--苹果切片放置后会变成棕色,旧车生锈也是氧化作用的结果。当焊料合金中的金属与空气接触时也会发生氧化。
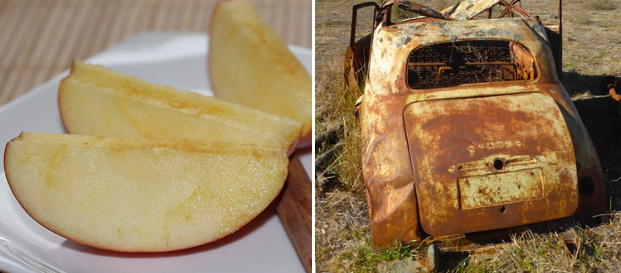
焊料合金与空气接触越多,其氧化倾向就越大。湿气、温度升高和加热也会加速氧化。当焊料合金与氧气发生反应时,就会在其表面形成氧化层。与纯合金相比,氧化层的导电性和机械稳定性都较差,这意味着很难形成良好的电气连接。
因此,制作和使用焊膏的主要目标之一就是尽可能减少氧化。事实上,助焊剂介质的主要作用之一就是去除氧化物和防止氧化。它通过化学作用以及在金属和空气之间形成屏障来实现这一目的。
金属容易与氧气发生反应,这就是焊膏需要小心处理和储存的原因。这也是为什么焊膏的生产过程必须严格控制的原因。通常情况下,粉末是在氧气被氮气取代的环境中形成的,而氮气不会与金属发生反应。
氧化倾向是一些制造商在回流焊过程中使用氮气环境的原因。这也是为什么更细的焊膏更脆弱的原因--当粉末尺寸变小时,表面积与金属质量的比例就更大。由于氧化发生在表面,更多的表面积意味着更多的氧化机会。
最后的话
就是这样!灰色粘液是通过制造微小的金属合金球,并将其与一种化学浆料结合而成,这种浆料经过优化,可以减轻氧化作用,促进牢固的电气连接。氧化既是制作过程的敌人,也是最终产品的敌人--这也是储存和处理说明的原因所在。