Attending IPC APEX EXPO 2025 reminded me why this show remains such an important event for the electronics manufacturing industry. It’s where cutting-edge technology meets practical engineering, where big-picture innovation converges with real-world application—and this year delivered on all fronts.
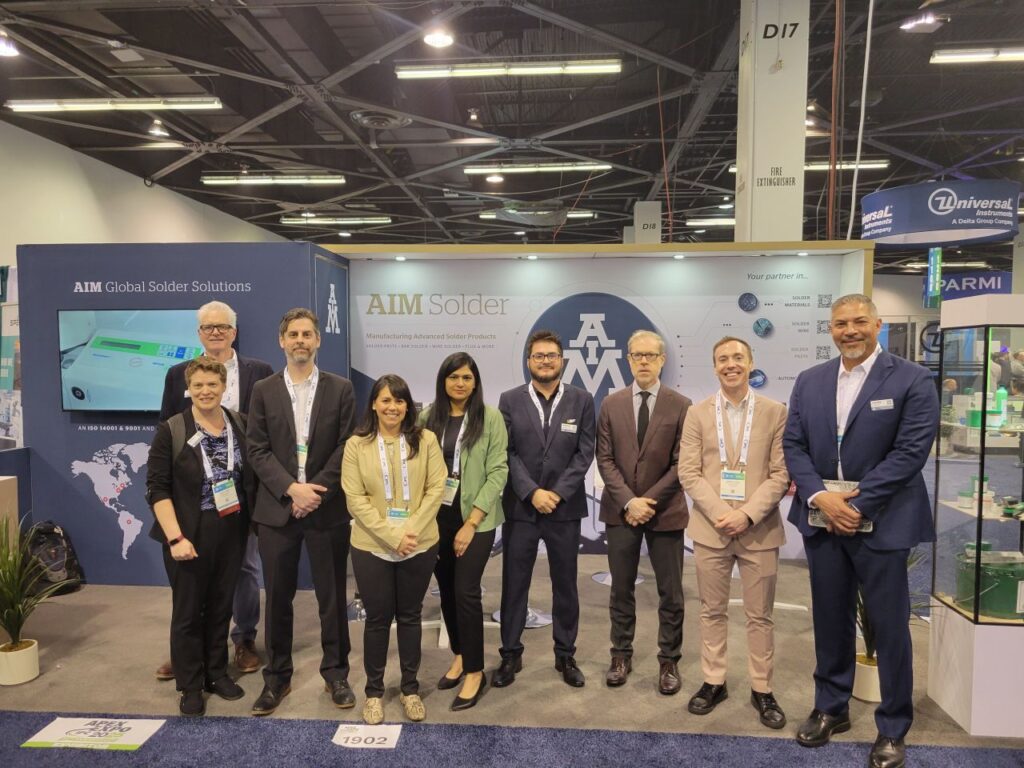
The Keynote: AI, Automation, and the Future of Manufacturing
The week kicked off with a high-energy keynote from Kevin Surace, a renowned futurist and AI visionary. His talk, “AI, Automation, and the Digital Transformation,” set the tone for the event by exploring how generative AI and automation are poised to reshape nearly every facet of our industry. From real-world manufacturing use cases to future-forward projections, Surace walked us through what’s already possible—and what’s just over the horizon.
What stood out to me most was the sheer potential of AI not just in production lines but in our day-to-day operations—technical documentation, process optimization, content development, and more. Imagine feeding in a library of soldering data, white papers, and application notes and asking AI to build a formatted, branded slide deck or a process guide tailored to a specific use case. That kind of efficiency could be transformative.
Sustainability in Action: From Soluboard® to Reclaim Programs
I had the chance to connect with Stephen Driver and Jack Herring from Jiva Materials, the creators of Soluboard®, the world’s first fully recyclable PCB with a biodegradable substrate. Their innovation is targeting OEMs and industries focused on reducing electronic waste, particularly in consumer and disposable electronics.
Because Soluboard can’t withstand peak reflow temperatures of standard solders, it’s a perfect match for low temperature solder—and they’ve been successfully using AIM’s low temperature solutions with their board. We’re now discussing the potential for collaborative studies, including SIR testing, to support this game-changing technology with additional technical validation. It’s an exciting opportunity not only to promote sustainable electronics but also to highlight low temperature soldering as a practical and future-ready solution.
AIM Solder’s Metals Reclaim Manager, Brendon Chrus, was also interviewed on-camera by IPC’s Seth Jacobsen as part of their sustainability initiative coverage. Brendon spoke about AIM’s cradle-to-grave reclaim program as well as some of our broader environmental commitments. We’ll share a link to the video interview once it’s available, and I highly recommend giving it a watch.
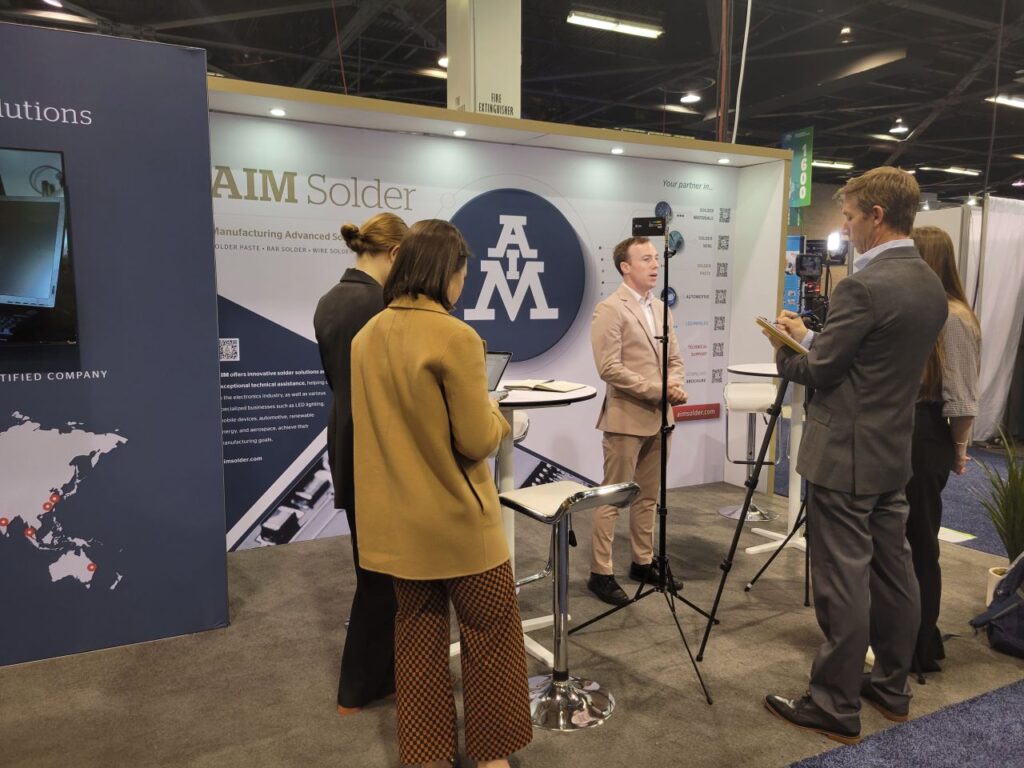
Engineering Conversations that Stick
One of the best parts of APEX is always the people—and sometimes, those quick conversations over coffee or during lunch offer some of the most thought-provoking insights.
At one table, I had the chance to meet Palash Pranav Vyas, a component reliability engineer and recent PhD graduate. His thesis research focused on high-temperature drop shock testing, simulating what happens to electronic devices when dropped while powered on—essentially at their peak operating temperature. The results? Devices are more vulnerable to failure when dropped hot. I think it was great how he thought to add real-world context to reliability testing, especially for consumer electronics and automotive applications. You can check out his published paper here: IEEE Article on High Temp Drop Shock Testing.
Sharing Our Research: Low Temperature in Wave Soldering
This year, I also had the opportunity to present some of our latest research at the technical conference. My session, “Exploring the Feasibility and Challenges of a Low Temperature Alloy in Wave Soldering Applications,” drew a full room and some great discussion.
We partnered with our colleagues at ITW EAE to explore whether low temperature alloys—which are already widely used in reflow—could perform reliably in wave soldering scenarios. We hope to present some follow-up research at the upcoming SMTAI 2025 in which we evaluate cross sections of our wave soldered samples.
A Glimpse into Industry Trends
Beyond the sessions and meetings, APEX 2025 offered a valuable pulse check on where the industry is headed. Several themes stood out during my time on the show floor and in various technical sessions:
- Design and assembly challenges for BTCs (Bottom Termination Components) continue to dominate conversations, especially in relation to voiding and cleaning.
- New SIR (Surface Insulation Resistance) test methods were discussed that aim to provide more accurate insight into contamination risk under modern process conditions.
- There was strong buzz around the power electronics market, which appears to be gaining momentum thanks to growth in EVs, renewables, and industrial automation.
- And as always, the many IPC standards committee meetings reminded me just how collaborative and foundational this work is for the entire industry. It was great to see so many familiar faces continuing to push the standards forward.
Talking Shop on The D-Code Podcast
Before wrapping up my time at APEX, I sat down with the hosts of The D-Code Podcast for a quick episode on solder powders. It was a fun, casual conversation where we touched on key powder characteristics, particle size, and their role in paste performance. Their team recorded dozens of short interviews with industry professionals throughout the week. Be sure to check out their series at The D-Code Podcast.
Final Thoughts
IPC APEX EXPO 2025 offered exactly what I had hoped for—innovation, collaboration, and a renewed sense of purpose as we tackle the challenges and opportunities ahead in electronics manufacturing. Whether it was presenting new research, connecting with sustainability leaders, or learning from peers across the globe, I left the show energized and with a giant to-do list.
There’s no doubt our industry is evolving quickly. At AIM, we’re excited to be part of that progress—partnering with companies like Jiva, sharing knowledge through podcasts and papers, and continuing to innovate in both materials and practices.
Looking forward to what comes next—and already thinking about APEX 2026!
Gayle Towell
AIM Solder Content Specialist