by Kevin Pigeon
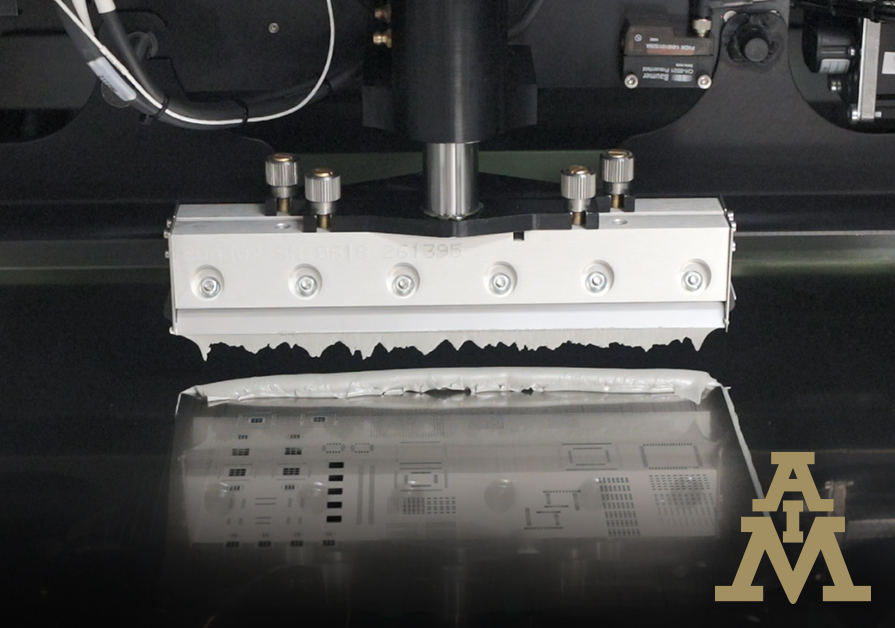
Understanding and controlling the assembly process window is not just about managing the solder paste. It’s about mastering all process variables across the entire SMT assembly process for optimal outcomes.
Defining the Assembly Process Window
The assembly process window defines the range of parameters within which solder paste will meet optimal performance standards. Straying outside this window can lead to defects, rework, and inconsistencies, affecting the efficiency and output of the electronics manufacturing process.
These parameters may include acceptable ranges for things like the following:
- Total reflow profile time from ambient to peak
- Peak reflow oven temperature
- Time above liquidus
- Rate of temperature change
- Squeegee pressure
- Squeegee speed
- Stencil thickness, design, aperture size, and coatings
- Precision of component placement
- Solder volume
- Component and PCB finish
- And more
Note that the Process Window Index (PWI), a statistical measure determined by the solder paste flux and alloy, is not alone sufficient for defining the assembly process window. All the factors above must be considered as well.
Factors Affecting the Assembly Process Window
The parameters which define the assembly process window are not isolated. Rather, they interact in complex ways, each influencing and being influenced by the others. Understanding and managing this interplay is not just about maintaining balance; it is about orchestrating harmony in the entire soldering process.
PCB Components and Substrate Material
Reflow temperatures must be high enough to activate the flux and form a reliable solder joint, but not so much as to damage the delicate components or PCB substrates. The thermal profile is also influenced by various factors, including the oven type, conveyor speed, and the thermal mass of the assembly.
PCB Design and Layout
The PCB design, including the layout of pads, ground planes, traces, and any fixtures required, determines how heat is distributed. Materials with different thermal properties behave differently under the same thermal profile. Adjustments in reflow profile as well as stencil modifications may be needed to strike the right balance.
Stencil Design
The stencil determines the shape and volume of solder deposits. Closeness and depth of apertures can affect how likely bridging or other defects may occur. Whether the stencil is coated or not can also affect how likely the paste is to adhere to the stencil as opposed to releasing cleanly after printing. These factors, together with the solder paste characteristics will determine the acceptable range of print settings.
Solder Paste Composition
Solder paste is a meticulously engineered mixture composed of solder powder and a specialized flux medium. The solder powder’s size, shape, and metallic alloy composition determine its melting behavior, while the flux medium’s chemistry dictates its activity level and performance under heat. We will look at this in more depth in the next section.
Solder Paste Composition and Its Impact in Detail
The solder alloy determines the mechanical strength and electrical properties of the resultant solder joint. Smaller powder sizes often lead to better printability, enabling finer pitch applications but may also increase the risk of oxidation, bridging, and voiding.
The flux medium is responsible for removing oxides from metal surfaces, protecting the solder area from further oxidation, and enhancing the wetting process. The composition of the flux medium influences the activity level, viscosity, slump characteristics, and residue properties for a particular type of solder paste. Manufacturers must consider:
- Reliability: The alloy composition of the solder powder, combined with the protective action of the flux, contributes to the long-term reliability of the soldered connections.
- Printability: This property is influenced by the physical characteristics of the solder powder and the rheology of the flux medium. Optimal printability ensures consistent deposition volumes (as measured by solder paste inspection (SPI)), crucial for minimizing defects in fine-pitch applications.
- Reflow Performance: The flux must activate at the right temperature, promoting excellent wetting and spreading of the solder alloy. The paste should also exhibit good coalescence, leading to well-formed solder joints without excessive voiding.
- Residue Characteristics: Post-reflow, the residue left by the flux medium can affect the performance and aesthetics of the PCB. Non-corrosive, no-clean fluxes that leave minimal, benign residues while water soluble and rosin-based fluxes require a cleaning step.
- Environmental Compliance: Solder pastes must comply with environmental regulations. Most applications require lead-free alloys, and some now specify that fluxes be halogen free.
- Operational: Consider shelf life, storage requirements, humidity window, and tack. All these factors will determine how easy the product is to use for your application.
But this is only one small fraction of the total picture. There can be dozens of additional considerations, including customer-specific criteria, all requiring just the right balance.
The radar chart in Figure 1 gives an idea of how you might compare two different flux types across these factors, enabling prioritization of certain features over others for a particular application.
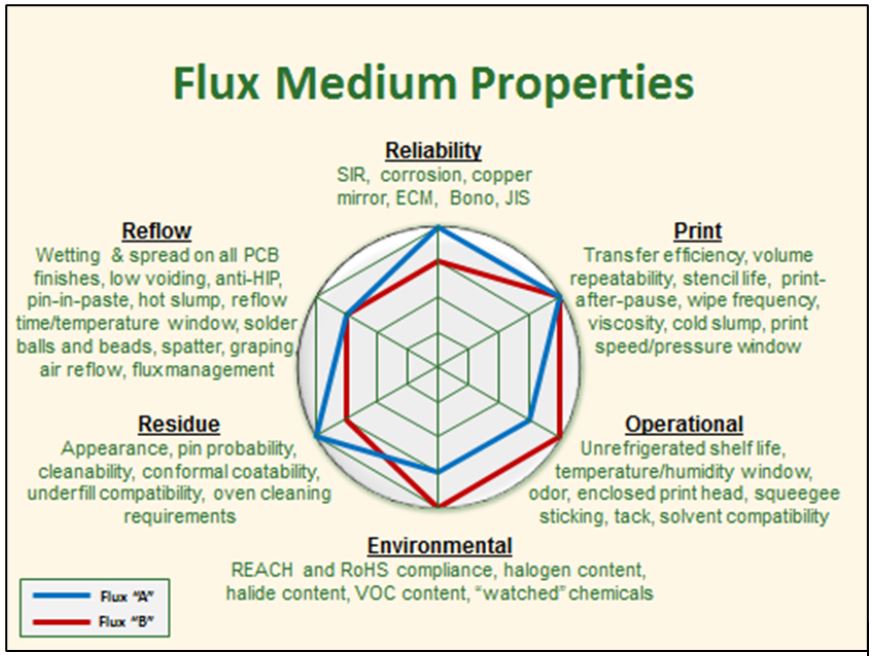
Figure 1. Radar chart of flux medium properties
Staying Within the Assembly Process Window
The choice of substrate, components, solder paste, stencil, and more determines how wide or narrow a particular assembly process window is. While it is often a good idea to make choices which keep that window as wide as possible to account for variations, this must also be balanced with the constraints of the application. Here are steps to follow to navigate this crucial balancing act:
- Develop a Comprehensive Understanding of Requirements: This includes the nature of the components, the types of PCB materials involved, and the environmental conditions in which the assembly will operate.
- Consider Solder Alloy Options: The melting point of the solder should align with the limits of your components and substrate. This includes accounting for extra heating that may be needed for regions of high thermal mass.
- Consider Flux Medium Options: A well-balanced flux can significantly impact the wetting behavior and the integrity of the solder joints. Consider the activity level, the residue characteristics, and the electrochemical reliability of the flux.
- Select the Right Solder Paste: After considering the alloy and the flux medium separately, it is important to dig a little deeper and ensure that the resulting solder paste is known for consistency and reliability. Variations in paste composition can lead to a wide range of assembly issues, making it crucial to choose products from reputable manufacturers known for maintaining high standards.
- Evaluate Solder Paste Performance: Because the final interaction of the paste with the process can lead to unanticipated outcomes, it is important to evaluate the paste’s performance in your production environment. Measure the volume of solder paste deposits, assess the voiding percentage, and look for other defects after reflow. You should also examine any residue left by the flux to ensure it meets specifications and can be cleaned if necessary.
- Adjust as Needed: Finally, adjust process parameters until desired results are obtained.
Final Thoughts
Mastering the assembly process window helps optimize solder paste applications. By understanding the interplay between paste properties and the broader assembly environment, professionals can enhance flexibility, reduce defects, and maintain a high standard of efficiency and reliability.
Originally published in Circuits Assembly, June 27, 2024.