As industry needs evolved, so did solder alloys, addressing specific performance requirements and setting new benchmarks. This article embarks on a chronological exploration of this alloy evolution journey, highlighting pivotal developments and the future trajectory of solder alloy innovation.
Historically, the introduction of regulations like RoHS (Restriction of Hazardous Substances) prompted a shift away from Pb-based solders. This necessitated the development of safer, yet equally effective, soldering materials. First-generation lead-free solder came in the form of SAC305, known for its robust application across various industries. But it was not without its challenges.
First Generation Pb-Free Alloys: The Dawn of SAC305
In July of 2006, RoHS regulations required solder alloys for many applications to contain less than 0.1% lead. This marked a significant shift in alloy development since the standard for decades had been eutectic tin-lead (Sn63Pb37) solder.
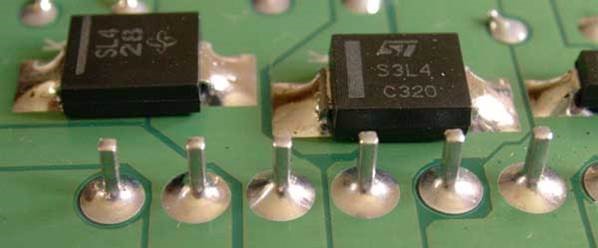
Sn63Pb37 is still used in some exempt sectors today. Its benefits include:
- A low melting point, which ensures minimal thermal stress on components during assembly
- Quick transition from liquid to solid due to eutectic nature, reducing the likelihood of defects
- Excellent wetting properties which ensure good solderability across various surfaces
Unfortunately, the health risk posed was considered too great for its continued use in most applications.
In the lead up to July 2006, many new alloys were tried and tested as Pb-free alternatives. The emergent leader at the time was SAC305, a tin-based alloy containing 3% silver and 0.5% copper.
SAC305’s initial appeal was rooted in its compatibility with existing manufacturing processes and lead components. However, as its usage proliferated, the industry began to recognize inherent flaws. High costs (due to the silver content), challenges with copper dissolution, and concerns over mechanical properties like drop shock performance and micro-crack resistance came to light.
Additionally, wetting performance issues, the propensity for tin whisker growth, and unpredictable aging performance underscored the need for further innovation.
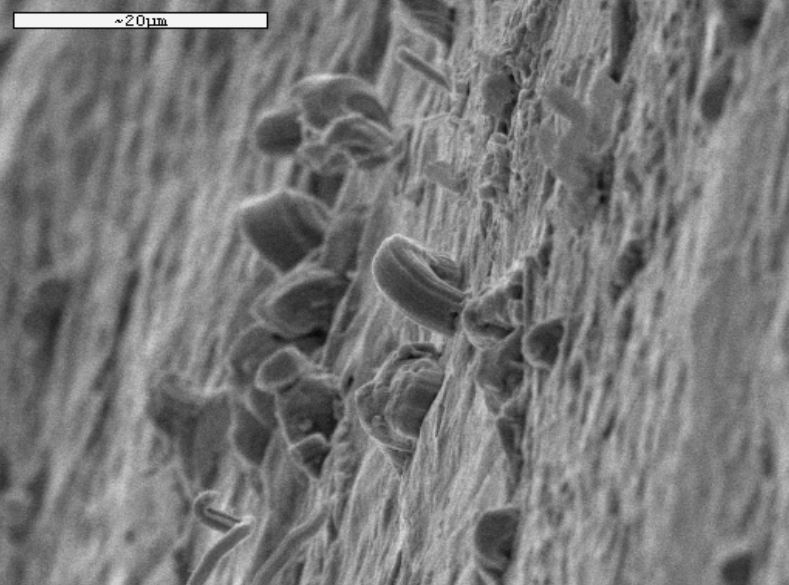
Second Generation Alloy Evolution: Variations of SAC
As the industry sought solutions to the limitations of SAC305, second-generation lead-free alloys emerged. Among these were SAC105, SAC0307, and SN100C.
SACX
The lower silver content of SAC105 and SAC0307 (consisting of 1% and 0.3% silver respectively) made them cost-effective alternatives to the higher-silver SAC305. However, their slightly higher melting ranges were a concern. SMT manufacturers already considered the melting temp of SAC305 to be high at 217-220C, especially in comparison to SnPb’s 183C.
Many low-silver SACX alloys also suffer from reduced mechanical strength, making them less suitable for high-stress or high-temperature applications.
SN100C®
Another contender that is still popular today was SN100C®. Developed by Nihon Superior, this tin-based alloy contains 0.7% copper, 0.05% nickel, and trace amounts of germanium. Known for its high fluidity, it offers excellent wetting characteristics, reducing defects and improving joint strength.
But while SN100C® provided a durable and reliable solution for various applications, its slightly higher melting point remained a drawback.
While these second-generation alloys did find a home in many wave soldering applications where problems related to higher temperatures don’t apply, SMT applications still preferred SAC305, despite its flaws.
Third Generation Alloy Evolution: High-Reliability Alloys
The advent of third-generation Pb-free alloys signified a monumental leap in solder technology and allow evolution, especially for industries where reliability is paramount, such as automotive, aerospace, and military applications. These cutting-edge alloys, developed through microalloying techniques, introduce minor elements to the base metal, enhancing specific properties without compromising the alloy’s fundamental characteristics.
One promising combination of microelement additions that AIM researchers discovered early on was bismuth and antimony. Bismuth significantly reduced the melting point, minimizing thermal stress during soldering, and Antimony enhanced mechanical strength.
At AIM our third-generation high reliability offerings include alloys called REL61TM and REL22TM. REL22TM contains tin, bismuth, silver, copper, antimony, nickel, and trace amounts of elemental grain structure refiners. It has proven extremely durable in harsh environments and offers improved wetting and thermal cycling performance. It also melts at a lower temperature than SAC305.
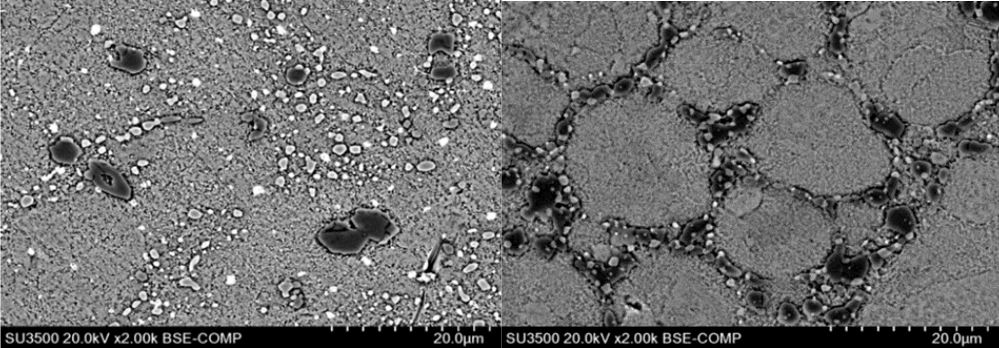
REL61TM is AIM’s lower cost high reliability alloy. While its performance doesn’t match that of REL22TM, it has proven superior to SAC305 across the board and comes at a lower price point as well.
The unique compositions of these alloys make them ideal for applications where endurance, longevity, and peak performance are non-negotiable. The table below shows some of AIM’s research data comparing REL22TM and REL61TM to SAC305.
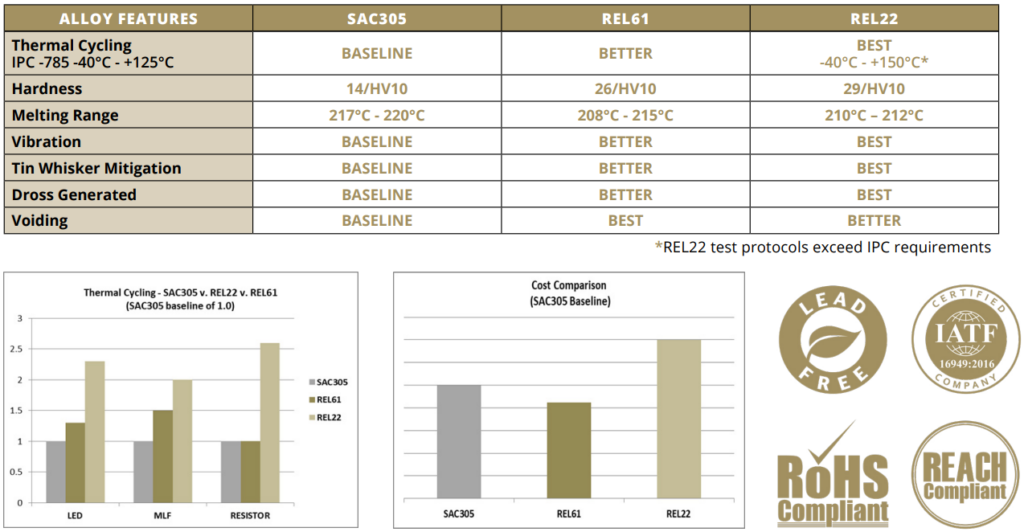
Looking Ahead
The journey from SAC305 to advanced lead-free alloys reflects the electronics industry’s adaptability and commitment to innovation. With each generation, from the first to the latest high-reliability alloys like AIM’s REL22TM and REL61TM, solder materials have become more sophisticated, meeting the increasing demands for performance, reliability, and environmental consciousness.
Another active area of research is low melting temperature alloys – ones that are closer to the melting point of tin-lead. However, there seems to be a trade-off in this domain when it comes to reliability. The holy grail remains a truly high reliability low temperature solder.