Dross formation is an inevitable byproduct of the wave soldering process, but excessive dross can lead to unnecessary material waste, increased costs, and process inefficiencies.
This blog post gives some insight into dross, including common questions and steps you can take to reduce dross formation in your solder pot.
What is Dross?
Dross is the oxidized metal waste that forms on the surface of molten solder during the soldering process, particularly in wave soldering and selective soldering. It consists of a combination of metal oxides and other contaminants that result from the reaction between molten solder and oxygen in the air.
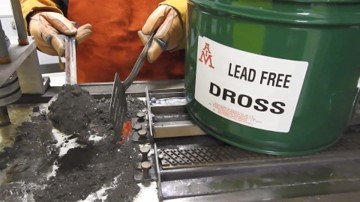
How Much Dross is Normal?
We often get questions around how much dross is normal, and how to reduce the amount of dross.
Well, the answer to the first question is “it depends”.
How much dross is “normal” depends on the alloy, the wave turbulence, and the process settings. You can look for another blog post here in the future examining that question in more detail. For now, let’s focus on the second question – the one people often really want answered anyway when they ask the first one.
How Do I Reduce Dross Formation?
The infographic below (downloadable here as a sharable PDF) outlines four key strategies for reducing dross formation:
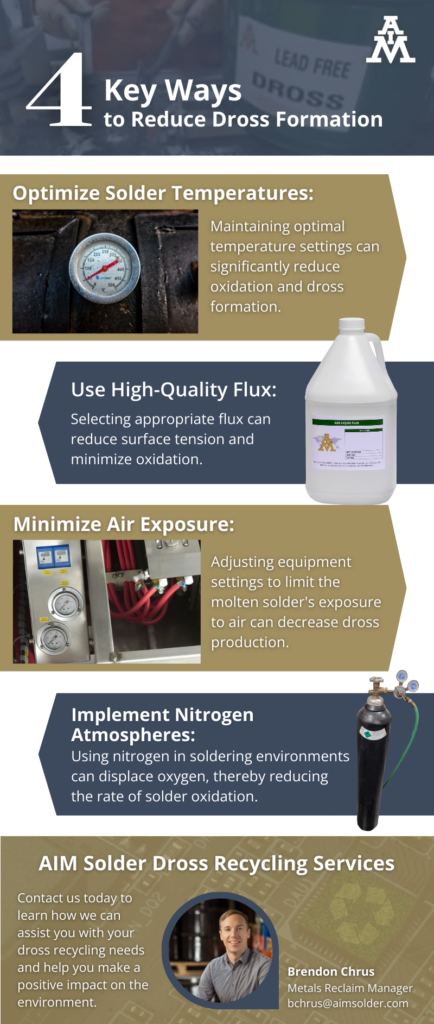
Still have questions? AIM is here to help! Contact our technical support team today.