Preparing for the Next Evolution in Miniaturization
AIM Solder is proud to declare 2025 as “The Year of Type 5,” recognizing the growing importance of this powder size and the shift it represents in the industry. While Type 5 solder paste won’t replace Type 4 as the industry standard this year, its adoption is accelerating, driven by demand for precise, consistent soldering.
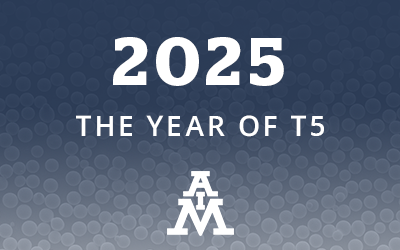
This blog explores the journey to Type 5, the factors influencing its use, and how manufacturers can prepare for this emerging standard.
The Evolution of Solder Paste Standards
It wasn’t too long ago that Type 3 paste was the go-to standard for many applications. Then the rise of smaller components, such as 0402 and 0201 packages, necessitated a shift to the now-common Type 4 powders. But with even smaller components like 01005s and 008004s gaining traction, manufacturers are once again looking to the next smaller paste size.
The recent SMTA Ultra High-Density Interconnect (UHDI) Symposium provided a glimpse into the near future of electronics manufacturing. Boards are getting more complex, traces smaller and closer together, and likewise, SMT components must follow suit. Presentations on next-generation stencil designs as well as evolving standards for solder paste performance, made it clear that the industry is pushing the boundaries of what’s possible.
There were some great discussions around the five-ball rule—a well-known way to estimate the smallest printable aperture for a given solder paste type. Opinions are conflicted as to whether this rule applies past Type 4, which is one of many reasons AIM is engaging in ongoing studies exploring the rule’s limits and the need for updated guidelines.
Overall, the symposium reinforced the importance of Type 5 solder paste as a stepping stone for navigating the challenges of miniaturization.
When Should You Transition to Type 5?
Deciding when to switch to Type 5 solder paste isn’t always straightforward. Aperture size is a key factor, but it’s not the only consideration. Variables like stencil design, paste performance under real-world conditions, and component placement demands all play a role.
For example, a rounded square aperture design can improve transfer efficiency and allow Type 4 paste to work well in borderline applications. However, as apertures shrink further or require greater consistency, Type 5 becomes the new requirement.
But beyond print performance, finer powders demand tighter controls in reflow processes and storage conditions. One talk at the symposium revealed that many production lines still operate with unacceptably high variations in print performance, an issue that must be addressed to achieve the precision required for emerging designs.
AIM Solder’s Commitment to Supporting the Transition
With decades of experience producing high-quality solder pastes, including Types 4, 5, and 6, AIM is uniquely positioned to guide customers through the transition to finer powders.
We develop our products with a focus on consistency, reliability, and process optimization and then couple that with technical support engineers at the ready to help our customers with just about anything.
We’ll be holding a webinar in April to provide further guidance on when to downsize your solder paste and you can look for additional technical papers and articles as we continue to advance our products and process recommendations.
Some Practical Tips for Working with Type 5
To get you started, here are just a few practical tips to help make the transition to Type 5:
- Optimize Stencil Design:
- Use nano-coated stencils to improve paste release and prevent clogging.
- Reduce stencil thickness to accommodate smaller apertures and consider using step stencils to ensure sufficient paste volume for robust joints.
- Dial in Reflow Parameters:
- Implementing nitrogen reflow can help minimize oxidation and improve coalescence. While not strictly required for Type 5, nitrogen becomes a necessity at Type 6 and finer.
- Adjust thermal profiles to account for the higher flux requirements of Type 5 pastes, ensuring proper wetting and joint integrity.
- Handle and Store Paste Properly:
- Store Type 5 paste under refrigeration to slow oxidation and extend shelf life.
- Limit paste exposure to air during production to maintain viscosity and performance.
- Monitor and Test Consistently:
- Use advanced inspection systems to evaluate print quality and consistency, particularly for fine-pitch components.
- Regularly assess transfer efficiency and deposition volume to identify process improvements.
Embracing the Future of Electronics Manufacturing
As the electronics industry continues its journey toward miniaturization, Type 5 solder paste is emerging as a critical tool for addressing the challenges of smaller, more intricate designs. At AIM Solder, we stand ready to support manufacturers through this evolution, offering expertise, innovative products, and unparalleled customer support.
For more information on AIM’s solder paste offerings or to discuss your transition to Type 5, contact us today.