AIM Alloys & Bar Solder
Optimized & Industry-ready Solutions
AIM Solder Alloys
AIM provides high quality solder alloys and complimentary materials to the electronics industry. AIM’s variety of solder alloys provide solutions for issues commonly found within the SMT assembly industry.
Zero defect wave soldering requires consistent solder quality. Contaminants and high oxide levels in bar solder can result in a variety of wave soldering defects such as bridging, projections, and poor wetting. To avoid these issues, AIM products are produced using AIM’s proprietary ElectropureTM process to produce a high-purity product exceeding IPC, JEDEC and IEC requirements.
AIM Electropure™ bar solder is processed from high-quality, virgin metals in a proprietary method that removes contaminants and reduces dissolved oxides. AIM’s Electropure™ technique results in an extremely pure, low-drossing solder bar that increases throughput and decreases defects.
AIM’s solder alloys are engineered to be compatible with a variety of PCB assembly products including solder paste, solder wire, and flux.
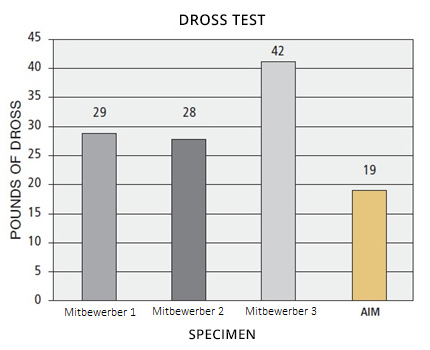
Dross Comparison of AIM Electropure Bar vs. Competitors
500 pounds of each type of alloy was heated in a wave solder pot at 500°F for 6 hours. The pot was de-drossed every 3 hours. After 6 hours the amount of dross generated from each type of solder was weighed. AIM’s bar solder has proven to reduce drossing as compared to competitive brands.
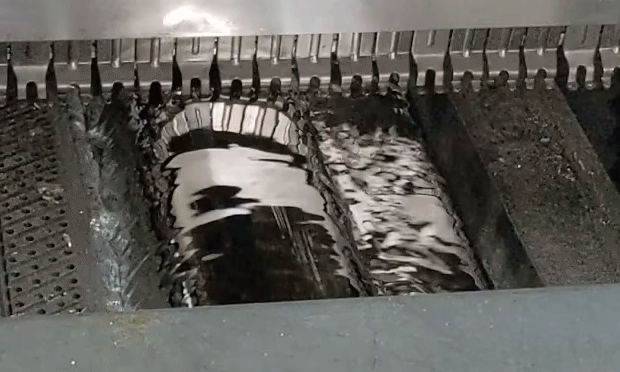
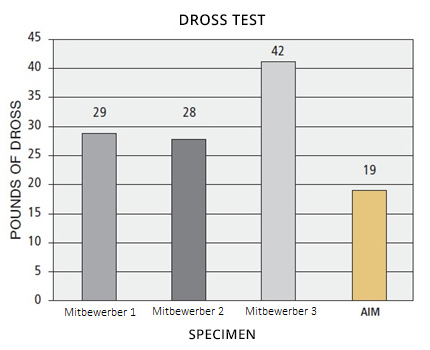
Dross Comparison of AIM Electropure Bar vs. Competitors
500 pounds of each type of alloy was heated in a wave solder pot at 500°F for 6 hours. The pot was de-drossed every 3 hours. After 6 hours the amount of dross generated from each type of solder was weighed. AIM’s bar solder has proven to reduce drossing as compared to competitive brands.
AIM’s high reliability alloys offer enhanced durability for use in extremely harsh environments. AIM’s REL22TM high reliability alloy provides superior thermal cycling performance, improved wetting, and high mechanical strength. AIM’s high reliability alloys can mitigate tin whisker formation and reduce voiding compared to other high reliability alloys. AIM’s high reliability alloys comply with IPC, RoHS, and REACH standards.
SAC alloys have become the standard alloy choice throughout the electronics assembly industry, most commonly SAC305. AIM’s SAC alloys provide excellent solder joint reliability, fatigue resistance and copper dissolution rates. AIM’s SAC alloys comply with IPC, JEDEC, RoHS, and REACH lead-free soldering standards.
AIM’s low and no silver alloys provide high performance options compared with the SAC type alloys but with a significant cost saving. AIM’s low and no silver alloy offerings are headlined by next generation REL61TM and the patented SN100C alloy. Both alloys are lower cost options with similar or superior soldering and reliability characteristics compared to SAC alloys. AIM’s low and no silver alloys comply with IPC, RoHS, and REACH standards.
AIM’s low temperature soldering materials includes low and reduced temperature reflow requirements. AIM’s lead-free low temperature alloys provide a melting temperature of 140°C-170°C reducing peak reflow temperatures by as much as 50°C. AIM low temperature fluxes have been specially formulated to work in combination with Sn/Bi (X) alloys to provide excellent processing characteristics as well as excellent wetting and joint strength.
AIM’s leaded solder alloys offer a low melting point and increased reliability over lead free solder alternatives. AIM’s leaded (Pb-bearing) solder alloys continue to be used/specified in medical, military, and aerospace applications.
Solder Alloy Selection Guide:
AIM offers a broad range of alloys for SMT, wave soldering, hand soldering, and various applications. Commonly used alloys for the electronics industry are shown below. *Other alloys and solder forms are available upon request.
Alloy | Melting Point °C | Product Attributes | Solder Form Availability* | |||
---|---|---|---|---|---|---|
Solder Paste | Bar Solder | Cored Wire | Solid Wire | |||
LOW TEMPERATURE | ||||||
Sn42/Bi58 | 138 | For low temperature soldering applications. Alloys containing high amount of bismuth have unique properties that may require special considerations. | ✓ | ✓ | ✓ | |
Sn42/Bi57/Ag1 | ||||||
Sn63/Pb37 | 183 | Not RoHS/REACH compliant. | ✓ | ✓ | ✓ | ✓ |
HIGH RELIABILITY | ||||||
REL22™ | 210-212 | High reliability, high strength lead-free solder alloy. Exceptionally durable for extreme service environments. | ✓ | ✓ | ✓ | ✓ |
CASTIN® | 217-219 | Improved drop-shock performance versus SAC305. | ✓ | ✓ | ✓ | ✓ |
TIN-SILVER/TIN-SILVER-COPPER (SAC) | ||||||
SAC305 | 217-220 | Industry standard for SMT and through hole soldering. High purity and high performance alloy. | ✓ | ✓ | ✓ | ✓ |
LOW/NO SILVER LEAD-FREE | ||||||
REL61™ | 208-215 | Enhanced reliability, high strength/low silver, lead-free solder alloy. Exhibits good wetting. Mitigates tin whisker formation. | ✓ | ✓ | ✓ | ✓ |
SAC0307 | 217-227 | Cost effective alternative to SAC alloys. Primarily used in wave, selective and hand soldering due to higher melting temperatures. High purity and high performance alloy | ✓ | ✓ | ✓ | ✓ |
SN100C | 227 | Near eutectic, low/no silver, cost effective alternative for wave soldering and hand soldering applications. | ✓ | ✓ | ✓ | ✓ |
Sn99.3/Cu0.7 |